Discover advanced strategies to reduce eddy current losses in permanent magnet motors, enhancing efficiency and performance. Learn how innovations in lamination techniques and material selection can minimize losses and improve motor reliability.
1. Introduction
1.1. Background of Eddy Current Losses
Eddy current losses are a critical factor influencing the efficiency of electrical machines. Eddy currents are loops of electrical current induced within conductors when they are exposed to a changing magnetic field, as described by Faraday’s law of electromagnetic induction. These circulating currents generate heat within the material, leading to energy dissipation known as eddy current losses. Historically, as electrical machines have evolved to operate at higher speeds and frequencies, the impact of eddy current losses on motor efficiency has become increasingly significant. These losses not only reduce the performance and efficiency of motors but also contribute to excessive heating, which can damage components and shorten the lifespan of the equipment.
1.2. Importance in Permanent Magnet Motors
In permanent magnet motors, the reduction of eddy current losses is particularly crucial due to the specific challenges inherent in their design. These motors utilize strong permanent magnets to create a constant magnetic field, which interacts with the stator to produce motion. The high magnetic flux densities and rapid changes in magnetic fields within these motors can induce substantial eddy currents in conductive components. This leads to increased energy losses and heat generation, adversely affecting motor performance. Therefore, minimizing eddy current losses is essential for performance enhancement in permanent magnet motor designs. Implementing advanced strategies to reduce these losses results in improved efficiency, higher torque output, reduced thermal stress, and extended motor lifespan. Addressing eddy current losses is a key focus for engineers aiming to optimize the performance and reliability of permanent magnet motors across various applications.
2. Causes of Eddy Current Losses in Permanent Magnet Motors
2.1. Magnetic Field Fluctuations
Eddy current losses in permanent magnet motors are significantly influenced by magnetic field fluctuations within the motor’s core materials. When the magnetic field in the motor changes—due to the rotation of the rotor or variations in current—it induces circulating currents in the conductive parts of the motor, as per Faraday’s law of electromagnetic induction. These induced currents flow in closed loops perpendicular to the magnetic field, generating heat and resulting in energy losses. The frequency of the magnetic field fluctuations plays a crucial role; higher frequencies lead to more rapid changes in the magnetic field, thereby increasing the magnitude of the induced eddy currents. Similarly, variations in flux density—the measure of the strength of the magnetic field over a given area—can exacerbate eddy current formation. Regions with higher flux density variations tend to induce stronger eddy currents, contributing to greater losses and reduced motor efficiency.
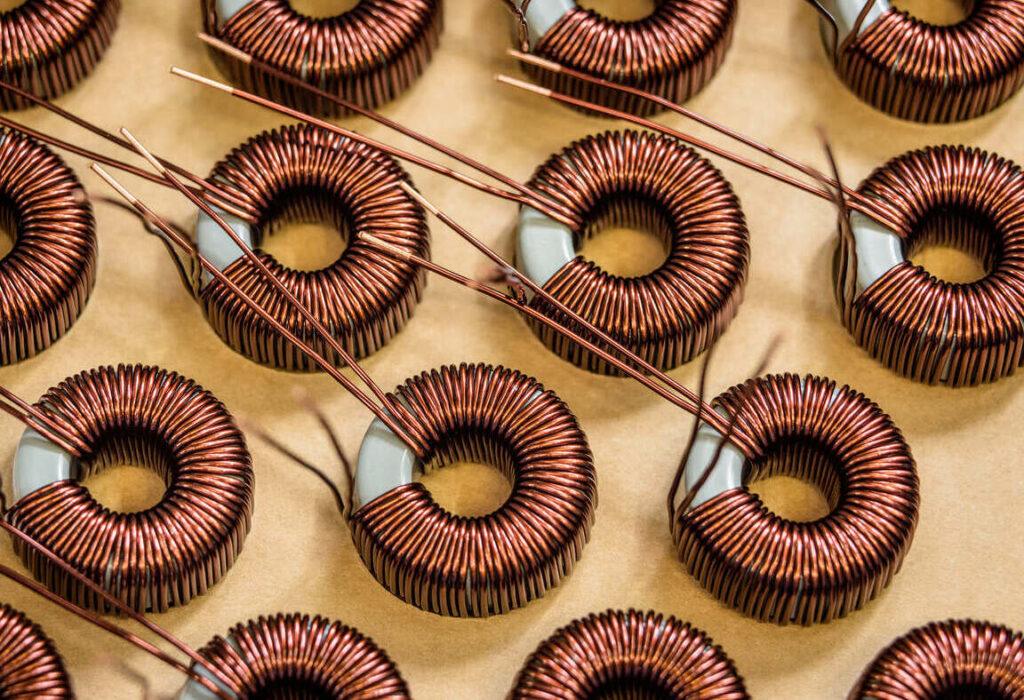
2.2. Material Conductivity
The electrical conductivity of the materials used in a permanent magnet motor directly impacts the extent of eddy current losses. Core materials with high electrical conductivity, such as solid iron, allow induced currents to flow more easily, leading to increased eddy current losses. Conversely, materials with lower conductivity impede the flow of these currents, thereby reducing losses. For example, silicon steel laminations are commonly used in motor cores because the added silicon decreases the material’s conductivity while maintaining desirable magnetic properties. Comparing different conductive materials, such as copper versus aluminum, reveals variations in eddy current formation due to their inherent conductivities. Selecting materials with optimal electrical and magnetic properties is essential for minimizing eddy current losses while ensuring efficient motor operation.
2.3. Geometric Factors
The geometry of the motor components, particularly the thickness and shape of the laminations, significantly affects eddy current pathways and losses. Thicker laminations provide a larger cross-sectional area for induced currents to circulate, resulting in higher eddy current losses. By reducing the lamination thickness, the path for eddy currents is constricted, which diminishes their magnitude and associated losses. Additionally, the shape of the laminations and overall design geometry can create areas where magnetic fields concentrate, leading to localized eddy currents. Sharp corners, irregular shapes, and misalignments can introduce unintended magnetic flux paths, increasing losses. Careful design of the motor geometry, including the use of uniformly thin and precisely shaped laminations, helps in disrupting eddy current pathways and reducing overall losses in permanent magnet motors.
3. Lamination Techniques
3.1. Thin Lamination Stacking
Thin lamination stacking is a fundamental technique for reducing eddy current losses in permanent magnet motor design. By utilizing thinner laminations, the cross-sectional area available for eddy currents to circulate is significantly reduced, which impedes their formation. The advantages of using thinner laminations include enhanced motor efficiency and decreased heat generation, contributing to better overall performance. However, manufacturing challenges arise due to the fragility of thin materials, which can lead to deformation or misalignment during assembly. Solutions to these challenges involve advanced manufacturing processes such as precision stamping and automated stacking equipment that ensure accurate alignment and consistent stacking of the thin laminations without causing damage.
3.2. Self Bonding Methods
Self bonding methods are instrumental in increasing the structural integrity of the motor core while reducing gaps between laminations, which in turn enhances magnetic permeability. This technique involves using special coatings integrated to the laminations that activate under heat and pressure during the stacking process. The result is a solid, unified core with minimized air gaps that can serve as pathways for eddy currents. By eliminating these gaps, self bonding reduces the likelihood of eddy current formation and improves the overall magnetic properties of the motor. Incorporating self bonding electrical steel not only strengthens the motor structure but also contributes to the reduction in eddy current losses, thereby enhancing efficiency and performance.
4. Impact on Motor Performance
4.1. Efficiency Improvements
Reducing eddy current losses significantly enhances the efficiency of permanent magnet motors. By minimizing these losses, the motor converts electrical energy to mechanical energy more effectively, leading to improved performance. Quantitatively, a reduction in eddy current losses can increase motor efficiency by several percentage points, which is substantial in industrial applications where even a 1% improvement can result in considerable energy savings. Real-world examples include manufacturers who have implemented thin lamination stacking and advanced manufacturing methods, observing efficiency gains of up to 5%. A practical example illustrating this impact can be found in the automotive industry. A study on electric vehicle (EV) motors demonstrated that implementing thinner lamination stacks and advanced manufacturing techniques led to a 5% increase in motor efficiency. This enhancement resulted in a 10% extension of the vehicle’s driving range per charge, highlighting the significant benefits of minimizing eddy current losses in permanent magnet motors. These improvements not only reduce operational costs but also contribute to a smaller carbon footprint due to lower energy consumption.
4.2. Thermal Management
Eddy current losses generate unwanted heat within the motor, affecting its thermal balance and potentially leading to overheating issues. By effectively reducing these losses, there is a significant decrease in heat generation. This reduction in internal temperatures enhances the motor’s thermal management, allowing it to operate within optimal temperature ranges. Consequently, the motor experiences less thermal stress, which extends its lifespan by preventing insulation degradation and mechanical wear caused by excessive heat. Improved thermal management also means that cooling systems can be downsized or operate more efficiently, further contributing to energy savings and reliability.
4.3. Cost Implications
While the adoption of advanced strategies to reduce eddy current losses may involve higher initial costs—such as investing in premium materials or sophisticated manufacturing techniques—the long-term financial benefits are substantial. The increased efficiency results in lower energy consumption, leading to significant savings on electricity bills over the motor’s operational life. For industrial facilities using multiple motors, these savings compound, offering a quick return on investment. Additionally, enhanced thermal management reduces maintenance costs and downtime associated with overheating issues. When considering the total cost of ownership, the operational benefits and energy savings from reduced eddy current losses often outweigh the initial expenses, making it a financially sound decision for both small-scale and large-scale applications.
5. Case Studies
5.1. Industrial Applications
In industrial settings, the implementation of advanced strategies to reduce eddy current losses has led to significant improvements in motor performance and energy efficiency. For instance, a manufacturing plant specializing in conveyor systems upgraded its permanent magnet motors by incorporating thin lamination stacking and precision laser cutting techniques. By doing so, they reduced eddy current losses by approximately 15%. This reduction translated into a notable decrease in energy consumption, saving the plant thousands of dollars annually on electricity costs. Additionally, the motors operated at cooler temperatures, which diminished the frequency of maintenance interventions and extended the service life of the equipment. Performance metrics showed an increase in motor efficiency from 88% to 93%, highlighting the tangible benefits of these advanced design strategies in an industrial context.
5.2. Electric Vehicles
In the electric vehicle (EV) industry, reducing eddy current losses in permanent magnet motors is crucial for enhancing vehicle performance and reliability. EV manufacturers have adopted strategies such as using high-resistivity materials and optimizing lamination techniques to minimize these losses. By reducing eddy current losses, the motors generate less heat, which is particularly important in the compact and enclosed spaces of EV designs where thermal management is challenging. This improvement leads to increased motor efficiency and, consequently, extends the driving range of the vehicle—a key selling point for consumers. These advancements not only make electric vehicles more competitive but also support the broader goal of sustainable and energy-efficient transportation solutions.
6. Future Trends and Innovations
6.1. Emerging Materials Research
The quest to further reduce eddy current losses in permanent magnet motors has led to extensive research into emerging materials with superior properties. Scientists and engineers are exploring advanced composites and novel alloys that exhibit high electrical resistivity while maintaining excellent magnetic permeability. The development and commercialization of these materials could revolutionize permanent magnet motor efficiency, leading to more compact, powerful, and energy-efficient machines across various industries.
6.2. Integration with Smart Systems
Another promising avenue for reducing eddy current losses lies in the integration of smart systems within motor designs. The use of sensors and real-time monitoring technologies allows for the detection and analysis of eddy currents as the motor operates. Advanced sensors can measure parameters such as temperature fluctuations, magnetic field variations, and electrical conductivity changes, providing valuable data on eddy current activity. This information enables the implementation of adaptive control systems that adjust operating conditions to minimize eddy current formation dynamically. For example, altering the input frequency or modifying the magnetic field strength in response to sensor data can help reduce losses. Additionally, predictive maintenance becomes more feasible as the system can anticipate issues related to eddy currents before they lead to significant efficiency drops or equipment failure. The integration of smart systems represents a proactive approach to managing eddy current losses, enhancing motor performance, and extending the operational lifespan through intelligent, data-driven adjustments during operation.
7. Conclusion
7.1. Summary of Strategies
Reducing eddy current losses is essential for optimizing the performance and efficiency of permanent magnet motors. This article has explored key methods to achieve this goal, including the use of thin lamination stacking to limit the pathways for eddy currents, self bonding lamination methods to enhance structural integrity and magnetic permeability, and advanced cutting techniques like laser cutting to produce precise, burr-free laminations. These strategies collectively contribute to significant improvements in motor efficiency, thermal management, and cost-effectiveness. Case studies in industrial applications and electric vehicles have demonstrated the real-world impact of these methods, showcasing efficiency gains, extended equipment lifespan, and operational savings. By addressing the causes of eddy current losses—magnetic field fluctuations, material conductivity, and geometric factors—engineers can design motors that perform optimally under various operating conditions.
7.2. Final Thoughts
The continuous innovation in reducing eddy current losses is vital for the advancement of permanent magnet motor technology. As industries demand more efficient and reliable motors, adopting advanced strategies becomes not just beneficial but necessary. Emerging materials research and the integration of smart systems represent the next frontier in this endeavor, promising further enhancements in performance and efficiency. It is imperative for designers, manufacturers, and stakeholders to embrace these innovations, investing in research and development to stay at the forefront of technology. By doing so, they contribute to the creation of motors that meet the evolving needs of modern applications while promoting sustainability through energy efficiency. The commitment to reducing eddy current losses is a step toward a future where electric motors achieve their full potential, driving progress across various sectors.
References
e-Mobility Engineering. (n.d.). Motor Laminations. Retrieved from https://www.emobility-engineering.com/motor-laminations/