Simple-die stamping is a cost-effective and flexible solution for producing custom electric motor core laminations. Learn how this method optimizes manufacturing efficiency while maintaining design precision for specialized motor applications.
1. Introduction
1.1 Purpose of This Blog Post
In the realm of electric motor manufacturing, the quality and consistency of core laminations can make or break overall performance. This blog post aims to shed light on simple-die stamping, a manufacturing process well-suited for producing these critical components. By exploring how simple-die stamping compares to other stamping techniques, we hope to provide readers with a clearer understanding of when it makes sense to adopt this method for custom motor core projects.
Simple-die stamping can often reduce costs and lead times, especially for small-to-medium production runs. However, it is important to remain practical about its capabilities and constraints. Throughout this discussion, we will highlight both the advantages and considerations of relying on simple-die stamping. Our goal is to give you the information you need to determine if it aligns with your specific manufacturing requirements.
1.2 Overview of Electric Motor Core Laminations
Electric motor core laminations are thin steel sheets stacked together to form the stator and rotor components within a motor. Their primary purpose is to minimize electrical losses and ensure efficient magnetic flux paths. In everyday applications—such as home appliances, HVAC systems, and small industrial motors—well-formed laminations contribute to energy savings, reduced heat generation, and improved torque performance.
When manufacturing these lamination stacks, precision is key. Minor deviations in thickness or shape can lead to decreased efficiency or unwanted vibration. This is where simple-die stamping comes into play. Unlike more complex approaches (e.g., progressive stamping), simple-die stamping relies on a straightforward die design to punch out shapes one at a time. This not only simplifies tooling but also makes it easier to prototype and refine a design before committing to high-volume production.
By understanding the role of laminations and the unique capabilities of simple-die stamping, manufacturers can make more informed decisions about which method best fits their production goals.
2. Understanding Simple-Die Stamping in the Context of Custom Core Laminations
2.1 What is Simple-Die Stamping?
Simple-die stamping is a straightforward metal forming process where a single die set punches out parts in one operation. Unlike progressive stamping—which involves multiple stations and continuous material feed—simple-die stamping relies on a simpler tooling concept that can be ideal for short production runs or specialized geometries. For example, when producing custom rotor or stator laminations, engineers can design a single die to cut each piece accurately, then manually or semi-automatically feed in the raw material sheet. Although this approach may not match the high-volume throughput of progressive stamping, it offers more flexibility for design changes and smaller-scale projects, reducing unnecessary tooling expenses.
2.2 Process Flow: From Metal Sheet to Finished Lamination
In a simple-die stamping process, sheets of electrical steel (or another suitable material) are fed into a stamping press equipped with the custom-designed die. Upon activation, the press exerts force to punch out the lamination shape, producing a single piece at a time. After each punch, the operator (or an automated feeder) repositions the sheet for the next cut, continuing until the required batch size is complete. This step-by-step approach allows for close monitoring of part quality, making it easier to catch potential issues—like burr formation or incorrect alignment—before they escalate.
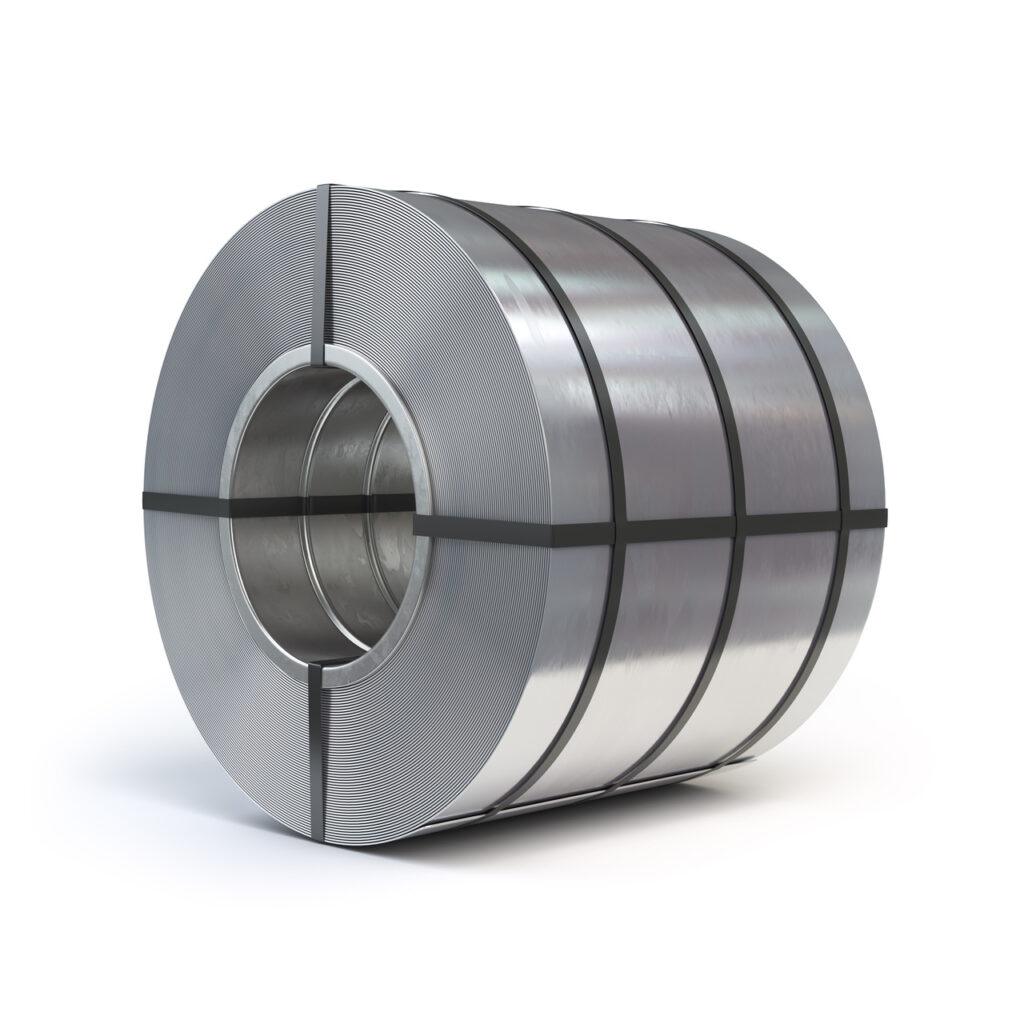
2.3 Common Applications and Relevance to Electric Motor Cores
Simple-die stamping is especially useful for prototyping, low- to medium-volume runs, and custom electric motor designs that require frequent adjustments. Industries such as aerospace, automotive, and renewable energy often rely on tailored motor cores for specialized performance needs. In these scenarios, a complex multi-station die might not be cost-effective or necessary. Simple-die stamping meets the demand for precision while keeping tooling investments in check, ensuring that manufacturers can quickly adapt lamination designs to evolving performance or compliance requirements.
3. 3 Convincing Reasons to Choose Simple-Die Stamping
3.1 Reason 1: Cost-Effectiveness in Custom Production
One notable advantage of simple-die stamping is its relatively low tooling cost. Because the process relies on a single die to cut each lamination, there is less complexity in the setup compared to multi-stage or progressive dies. For manufacturers who need to produce custom rotor or stator laminations in limited quantities, investing in a single, simpler die often proves more economical than creating multiple dies for each stage of production.
Additionally, simple-die stamping can help reduce waste. If a design requires minor adjustments—such as a small tweak in slot geometry—only one die needs to be modified, rather than an entire series of tooling stations. This cost advantage is particularly evident in short-to-medium production runs, where cutting down on tooling expenses can significantly impact overall project budgets.
3.2 Reason 2: Design Flexibility and Rapid Tooling Modifications
When working on specialized electric motor projects, frequent design changes may be unavoidable due to testing feedback or evolving performance requirements. Simple-die stamping accommodates these shifts by allowing relatively quick alterations to a single die. In real-world applications—like prototype motors for aerospace systems—engineers often refine lamination dimensions multiple times before finalizing a design. With a simple-die approach, each iteration involves fewer engineering hours and a faster turnaround, because only one tool requires modification.
Moreover, this flexibility helps teams gather practical data about form, fit, and function without overcommitting to complex tooling. Many companies find that the ability to pivot swiftly during product development can be a decisive advantage when time-to-market is critical.
3.3 Reason 3: Streamlined Production and Short Lead Times
While simple-die stamping may not match the volume output of progressive systems, it often leads to faster lead times for custom orders. This can be key for limited-run motors or urgent replacement parts. Since die setup and maintenance are less involved, manufacturers can transition quickly from one project to another. In practice, this agility supports tighter project timelines—an important consideration for businesses seeking to bring new or updated motor designs to market without delay.
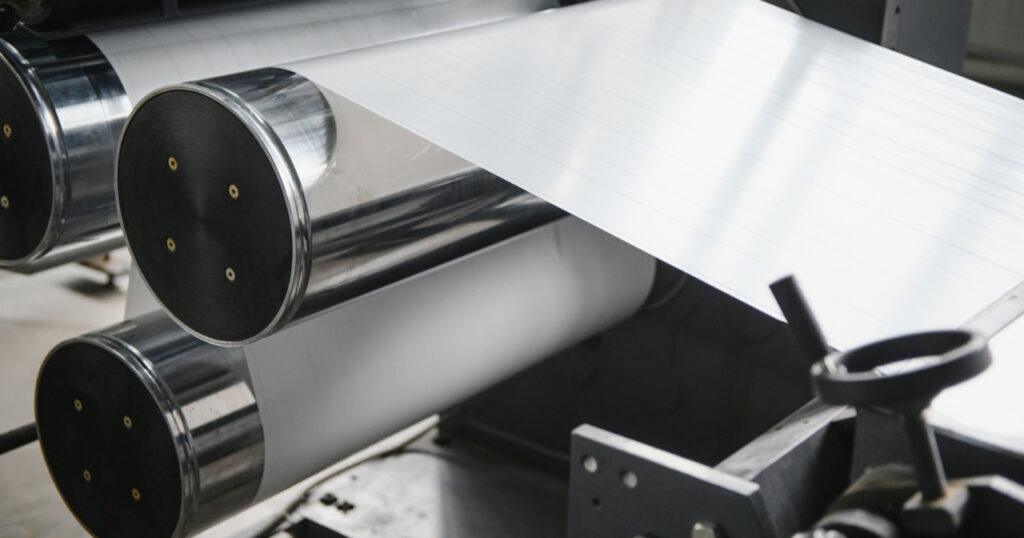
4. Product Information: Specifications & Material Considerations
4.1 Selecting the Right Materials for Simple-Die Stamping
Material choice is critical for achieving optimal magnetic performance and mechanical strength in electric motor core laminations. In many cases, manufacturers use silicon steel or other specialized electrical steels with low core loss to improve efficiency. The thickness of these steels can vary—from around 0.15 mm for high-efficiency designs up to 0.65 mm or more for less demanding applications. When using simple-die stamping, it is important to consider how the selected material’s ductility and hardness may affect edge quality and die wear. For instance, high-silicon content steels can offer excellent electrical properties but may require closer attention to cutting clearances and press tonnage.
4.2 Tolerances, Accuracy, and Dimensional Consistency
Tight tolerances are often necessary to ensure the stacked laminations align properly in both stators and rotors. Although progressive stamping systems can achieve very high consistency, simple-die stamping can also maintain respectable accuracy levels when properly managed. Key factors include die design, press stability, and rigorous maintenance of cutting tools. For instance, maintaining a consistent clearance between the punch and die helps minimize burr formation and ensures each lamination meets the required dimensional specifications. In real-world production scenarios, manufacturers might perform frequent inspections with calipers, coordinate measuring machines (CMMs), or laser-based systems to confirm that each batch remains within acceptable tolerance ranges.
4.3 Quality Assurance and Testing
A disciplined quality assurance program is vital for motor core projects, given that laminations directly influence motor efficiency and overall performance. Many manufacturers employing simple-die stamping conduct in-process checks to detect issues such as excessive burrs or uneven lamination thickness. Visual inspections, magnetic property measurements, and flatness tests are common methods for verifying part quality. While simple-die setups may not process parts at the same speed as multi-stage lines, they often allow operators to catch and address potential concerns quickly. By combining robust testing with ongoing die maintenance, manufacturers can maintain the reliability and consistency needed for high-performance custom motor cores.
5. Practical Applications and Real-World Examples
5.1 Common Use Cases in the Electric Motor Industry
Many manufacturers rely on simple-die stamping when handling specialized or limited-run electric motor laminations. For instance, small industrial motors used in robotic arms or conveyor systems often require iterative refinements to rotor or stator geometries based on performance feedback. Unlike progressive stamping, which typically suits high-volume output, single-die configurations are more flexible and cost-effective for smaller batches or evolving design needs.
In household appliance production, this method often proves beneficial for high-efficiency fans or compact compressors. Even minor changes to slot profiles or lamination thickness can yield measurable improvements in energy consumption, torque characteristics, and noise reduction. By employing a single die, these modifications can be tested promptly, sparing manufacturers from the expense and lead times of multi-stage stamping processes. This streamlined approach is particularly valuable in markets such as home appliances or HVAC systems, where product innovation and rapid development are essential to remain competitive.
Moreover, simple-die stamping accommodates frequent design iterations without the extensive retooling typically associated with progressive lines, which can help companies respond promptly to feedback from test runs or evolving customer requirements. Overall, it caters to industries seeking a balance of adaptability, cost-effectiveness, and quality control—making it a practical choice for custom electric motor laminations.
Further Reading: