Explore how Tesla, Nissan, and BMW leverage advanced EV motor technologies to enhance electric vehicle performance and efficiency. This comparative analysis delves into innovations in stator core laminations and motor designs shaping the future of EVs.
1. Introduction
1.1 Overview of Electric Vehicle Motor Technologies
a. Importance of EV Motor Technologies in Performance
Electric vehicle (EV) motor technologies stand at the forefront of the automotive industry’s shift towards sustainable transportation. The design and efficiency of EV motor technologies are critical determinants of a vehicle’s overall performance, influencing factors such as acceleration, top speed, energy consumption, and driving range. Advanced EV motor technologies, including innovations in stator core laminations and motor cores, play a pivotal role in reducing energy losses and enhancing torque output. These improvements not only lead to better vehicle performance but also contribute to longer battery life and reduced operational costs. As consumers increasingly prioritize efficiency and environmental impact, the importance of sophisticated EV motor technologies continues to grow.
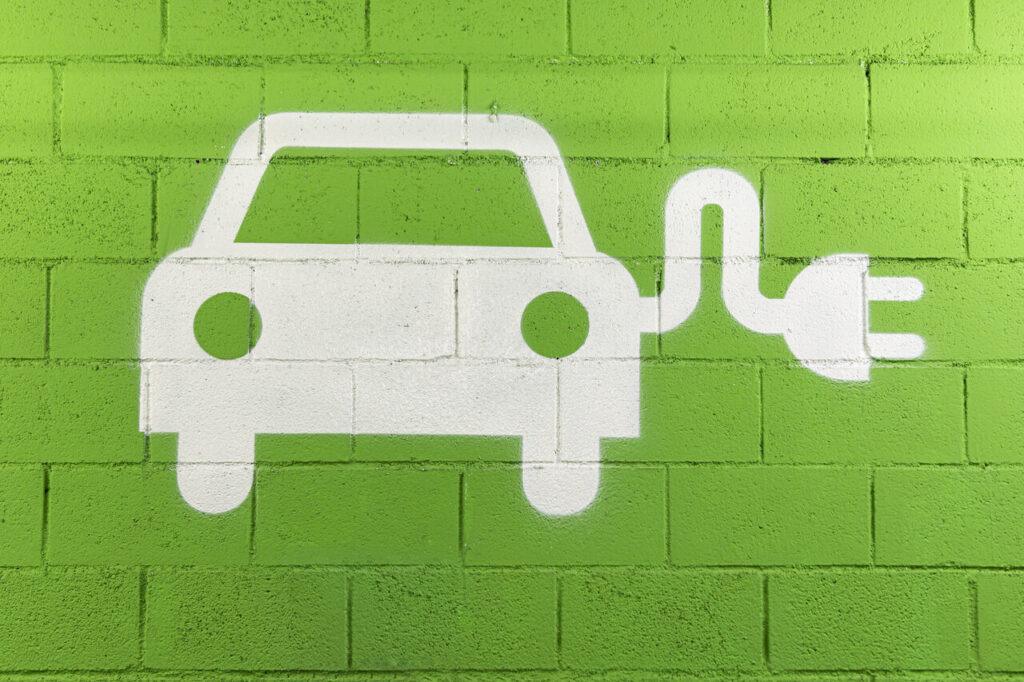
1.2 Purpose of the Comparative Analysis
a. Highlighting Innovations in EV Motor Technologies by Leading Manufacturers
This article aims to provide a comprehensive comparative analysis of the EV motor technologies employed by three leading manufacturers: Tesla, Nissan, and BMW. By exploring each company’s unique approach to EV motor technologies—particularly their use of stator core laminations and motor cores—we seek to highlight the innovations that set them apart in a competitive market. Understanding these advancements offers valuable insights into how these manufacturers optimize performance, efficiency, and cost-effectiveness in their vehicles. Additionally, this analysis sheds light on current trends and future directions in EV motor technologies, providing readers with a deeper appreciation of the engineering feats driving the evolution of electric transportation.
2. Tesla’s Motor Technology
2.1 Evolution of Tesla’s EV Motor Technologies
a. From Induction Motors to Permanent Magnet EV Motor Technologies
Tesla has been a pioneer in electric vehicle innovation, and a significant aspect of its success lies in the continuous evolution of its EV motor technologies. Initially, Tesla utilized alternating current (AC) induction motors, notably in the Tesla Roadster and early Model S vehicles. These induction motors were praised for their simplicity and robustness but had limitations in efficiency at lower speeds.
Recognizing the need for greater efficiency and performance, Tesla transitioned to permanent magnet synchronous reluctance motors in later models like the Model 3 and updated versions of the Model S and Model X. These advanced EV motor technologies offer higher efficiency across a wider range of speeds and are lighter and more compact than their induction counterparts. This shift allowed Tesla to enhance acceleration, extend driving range, and reduce energy consumption, solidifying its position as a leader in EV motor technologies.
2.2 Use of High-Grade Silicon Steel Laminations in EV Motor Technologies
a. Enhancing Efficiency and Reducing Energy Losses
A critical factor in Tesla’s EV motor technologies is the use of high-grade silicon steel laminations in the stator core. Silicon steel is known for its excellent magnetic properties and low core loss, which is essential for minimizing energy losses due to hysteresis and eddy currents. By incorporating thin laminations of this material, Tesla reduces the formation of unwanted currents that generate heat and waste energy.
These high-quality laminations are meticulously stacked and insulated to form the stator core, ensuring optimal magnetic flux and minimal losses. This attention to material selection and engineering precision contributes to the motors’ superior performance, allowing for greater power output without compromising efficiency. The result is an electric motor that delivers impressive torque and acceleration while maximizing the vehicle’s driving range.
2.3 Innovations in Stator Core Lamination
a. Impact on Performance and Range
Tesla’s innovations extend beyond material selection to the manufacturing processes of stator core laminations within their EV motor technologies. The company employs advanced techniques such as laser cutting and automated stacking to achieve precise dimensions and alignment of the laminations. This precision reduces gaps and inconsistencies in the stator core, enhancing the overall magnetic efficiency of the motor.
Additionally, Tesla explores proprietary bonding methods to secure the laminations without increasing their thickness or adding excessive weight. These methods improve the structural integrity of the motor while maintaining optimal magnetic properties. By pushing the boundaries of stator core lamination technology, Tesla effectively increases motor efficiency, which directly translates to improved vehicle performance and extended range. These innovations not only set Tesla apart from competitors but also drive the industry forward by demonstrating the tangible benefits of advanced EV motor technologies.
3. Nissan’s Motor Technology
3.1 The Motor Design of the Nissan Leaf’s EV Motor Technologies
a. Emphasis on Affordability and Efficiency
Nissan has been a pioneer in making electric vehicles accessible to the mass market, and the Nissan Leaf is a testament to that commitment. Introduced in 2010, the Leaf was one of the first widely available all-electric cars aimed at everyday consumers. The motor design of the Nissan Leaf focuses on affordability without sacrificing efficiency in its EV motor technologies. It utilizes an AC synchronous electric motor that provides a smooth and quiet driving experience. The emphasis is on delivering sufficient power for daily commuting while maintaining energy efficiency to maximize the vehicle’s range. By prioritizing cost-effective solutions, Nissan has made electric mobility more attainable for a broader audience, encouraging the adoption of environmentally friendly transportation.
3.2 Material Selection for Stator Core Laminations
a. Strategies to Minimize Eddy Current Losses
In enhancing motor efficiency, Nissan pays meticulous attention to the materials used in the stator core laminations of the Leaf’s EV motor technologies. The company selects high-quality electrical steel with specific magnetic properties to reduce energy losses. These laminations are thin and coated with insulating layers to prevent eddy currents, which are loops of electrical current induced within the conductor by a changing magnetic field. Eddy currents can generate unnecessary heat and decrease efficiency. By minimizing these losses through careful material selection and lamination design, Nissan improves the overall performance of the motor. This strategy allows the Leaf to achieve a respectable driving range while keeping production costs in check.
3.3 Manufacturing Techniques in EV Motor Technologies
a. Balancing Cost-Effectiveness with Performance
Nissan employs advanced manufacturing techniques to produce the stator core laminations and assemble the electric motors efficiently within their EV motor technologies. Automation and precision stamping are utilized to create consistent and high-quality laminations at scale. By optimizing the manufacturing process, Nissan balances cost-effectiveness with the need for performance and reliability. The use of automated assembly lines reduces labor costs and minimizes human error, ensuring that each motor meets strict quality standards. Additionally, Nissan’s investment in scalable manufacturing technologies allows for economies of scale, further reducing the cost per unit. This approach ensures that the Leaf remains competitively priced in the market while delivering the performance and efficiency that consumers expect from an electric vehicle equipped with advanced EV motor technologies.
4. BMW’s Motor Technology
4.1 Advanced Motor Systems in the BMW i3’s EV Motor Technologies
a. Focus on Performance and Driving Dynamics
BMW has built a reputation for delivering vehicles that offer exceptional performance and engaging driving experiences, and this philosophy extends to their electric models like the BMW i3. The i3 features an advanced synchronous electric motor that provides instantaneous torque, allowing the vehicle to accelerate smoothly and swiftly. With a focus on performance, BMW designed the i3’s motor to deliver a dynamic driving experience comparable to their traditional combustion engines. The electric motor generates approximately 170 horsepower and 184 lb-ft of torque, enabling the i3 to accelerate from 0 to 60 mph in just over seven seconds. This emphasis on driving dynamics ensures that the transition to electric mobility does not come at the expense of the exhilarating performance that BMW drivers expect from cutting-edge EV motor technologies.
4.2 Innovative Use of Materials
a. Lightweight Construction and High-Strength Laminations
A key aspect of BMW’s approach to electric vehicle design is the innovative use of lightweight materials to enhance efficiency and performance in their EV motor technologies. In the BMW i3, the company employs a combination of carbon fiber-reinforced plastic (CFRP) for the passenger cell and aluminum for the chassis. This lightweight construction reduces the overall weight of the vehicle, which in turn improves acceleration, handling, and energy efficiency.
When it comes to the motor itself, BMW utilizes high-strength electrical steel for the stator core laminations. These laminations are meticulously engineered to be thin yet robust, minimizing energy losses due to eddy currents and hysteresis. By optimizing the thickness and quality of these laminations within their EV motor technologies, BMW enhances the magnetic efficiency of the motor, resulting in better performance and longer range. The use of such advanced materials demonstrates BMW’s commitment to pushing the boundaries of electric motor technology.
4.3 Precision Manufacturing Processes
a. Automation and Laser Cutting Technologies
BMW integrates state-of-the-art manufacturing processes to ensure the precision and quality of their electric motors within their EV motor technologies, as highlighted in recent innovations reported by Automotive News. Automation plays a crucial role in assembling the intricate components of the motor with high accuracy and consistency. Robotic systems handle tasks such as winding the stator coils and assembling the motor parts, reducing the likelihood of human error and increasing production efficiency.
By combining automation with advanced manufacturing techniques, BMW enhances the performance and reliability of their electric motors. These processes enable the production of high-quality components that meet the stringent standards required for modern electric vehicles. BMW’s investment in precision manufacturing underscores their dedication to delivering electric vehicles that excel in both performance and efficiency, powered by innovative EV motor technologies.
5. Comparative Analysis
5.1 Performance Metrics Comparison
a. Efficiency, Power Output, and Range
When comparing the EV motor technologies of Tesla, Nissan, and BMW, several key performance metrics emerge: efficiency, power output, and driving range. Tesla’s electric motors are renowned for their exceptional efficiency, often exceeding 90% during operation. This high efficiency contributes to Tesla vehicles achieving some of the longest driving ranges in the industry, with models like the Model S boasting ranges over 400 miles on a single charge. The use of high-grade silicon steel laminations and advanced EV motor technologies allows Tesla to maximize power output while minimizing energy losses, resulting in impressive acceleration and top speeds.
Nissan’s approach with the Leaf emphasizes efficiency within the context of affordability. The Leaf’s motor delivers sufficient power for daily commuting, with an efficiency that enables a driving range between 150 to 226 miles, depending on the battery configuration. While the power output is modest compared to Tesla, Nissan balances performance with cost-effectiveness, making electric vehicles accessible to a broader market without significantly compromising on range or efficiency in their EV motor technologies.
BMW’s i3 focuses on delivering a dynamic driving experience, with its motor producing approximately 170 horsepower. The efficiency of the i3 is enhanced by the vehicle’s lightweight construction, contributing to a driving range of around 153 miles. Although the range is shorter than some competitors, BMW prioritizes performance and handling, offering swift acceleration and agility suited for urban environments. The precise engineering of the motor, including the use of high-strength laminations, ensures that efficiency complements the vehicle’s performance-oriented design.
5.2 Material and Design Approaches
a. Impact on Motor Efficiency and Vehicle Performance
The material selection and design philosophies of each manufacturer significantly impact motor efficiency and overall vehicle performance within their EV motor technologies. Tesla’s use of high-grade silicon steel laminations reduces hysteresis and eddy current losses, enhancing the motor’s magnetic efficiency. Their innovative stator core designs and proprietary manufacturing techniques result in motors with high power density and efficiency, directly contributing to superior vehicle performance and extended range.
Nissan employs materials and designs that strike a balance between efficiency and cost. By selecting appropriate electrical steel for the stator laminations and optimizing lamination thickness, Nissan minimizes energy losses while keeping production costs low. This pragmatic approach ensures that the Leaf offers reliable performance and efficiency at a price point accessible to many consumers.
BMW’s innovative use of lightweight materials, such as carbon fiber-reinforced plastic for the vehicle body and high-strength steel in the motor laminations, reduces overall weight and enhances efficiency within their EV motor technologies. The precise manufacturing of thin, high-quality laminations improves magnetic properties and reduces losses. These material and design choices enable the i3 to deliver responsive performance and agility, aligning with BMW’s emphasis on driving dynamics.
5.3 Manufacturing and Cost Implications
a. Influence on Pricing and Market Positioning
Manufacturing techniques and material choices directly affect production costs, influencing each manufacturer’s pricing strategy and market positioning in the realm of EV motor technologies. Tesla’s investment in advanced materials, proprietary motor designs, and automated manufacturing processes results in higher production costs. Consequently, Tesla positions its vehicles as premium products, offering cutting-edge EV motor technologies and performance at a higher price point.
Nissan’s focus on cost-effective manufacturing allows the Leaf to be competitively priced in the mass market. By streamlining production processes and optimizing material use, Nissan reduces manufacturing expenses. This cost efficiency enables Nissan to offer the Leaf at a lower price, appealing to cost-conscious consumers seeking an entry point into electric vehicle ownership.
BMW balances advanced manufacturing techniques with the use of premium materials, accepting higher production costs to maintain brand prestige and performance standards. Automation and precision processes like laser cutting enhance quality but add to expenses. BMW positions the i3 as a premium urban electric vehicle, targeting consumers willing to invest more for superior build quality, performance, and the brand’s hallmark driving experience.
In summary, the comparative analysis highlights how Tesla, Nissan, and BMW tailor their EV motor technologies to align with their brand identities and target markets. Tesla pushes technological boundaries to offer top-tier performance, Nissan emphasizes practicality and affordability, and BMW focuses on delivering a premium driving experience. Each manufacturer’s approach to materials, design, and manufacturing reflects their strategic priorities in the evolving electric vehicle landscape.
6. The Role of Stator Core Laminations in EV Motor Technologies
6.1 Common Techniques Across Manufacturers
a. Reducing Energy Losses and Improving Efficiency
Stator core laminations are fundamental components in EV motor technologies, playing a crucial role in enhancing efficiency and reducing energy losses. Tesla, Nissan, and BMW all employ common techniques in the design and manufacture of these laminations to address issues like eddy current and hysteresis losses. By using thin sheets of high-quality electrical steel, stacked and insulated from each other, they effectively minimize the pathways for eddy currents, which are undesirable currents induced within the motor’s core that generate heat and waste energy. The thin laminations reduce hysteresis losses by ensuring that the magnetic domains within the steel can realign more easily with the changing magnetic fields during motor operation. This common approach helps all three manufacturers improve the magnetic efficiency of their motors, leading to better performance, increased range, and enhanced reliability of their electric vehicles.
6.2 Unique Innovations
a. Proprietary Technologies and Patents
While the basic principles of stator core lamination are shared, each manufacturer introduces unique innovations within their EV motor technologies to gain a competitive edge. Tesla, for instance, has developed proprietary methods for producing ultra-thin laminations using high-grade silicon steel, which enhances magnetic permeability and reduces losses more effectively than standard materials. Their advanced manufacturing processes, including specialized bonding techniques and automated assembly, are protected by patents that contribute to the superior performance of Tesla motors.
Nissan focuses on cost-effective innovations, such as optimizing the geometry of the laminations to maximize efficiency without incurring high material costs. Their design adjustments and manufacturing efficiencies allow them to produce effective motors suitable for mass-market vehicles like the Leaf, balancing performance with affordability. Nissan’s approach involves meticulous material selection and precise stamping techniques to produce laminations that meet their performance criteria while keeping production expenses low.
BMW leverages precision engineering and cutting-edge technologies allow for complex motor designs that improve efficiency and performance. BMW’s use of unconventional materials and construction methods, often covered by patents, reflects their commitment to innovation and excellence in engineering. Their focus on lightweight yet strong laminations contributes to the dynamic driving experience that BMW vehicles are known for.
These unique innovations demonstrate how each manufacturer builds upon common techniques to develop proprietary solutions that enhance their EV motor technologies. By investing in research and development, they not only improve their own products but also push the boundaries of electric vehicle technology as a whole. This continuous innovation is essential for advancing the industry and meeting the growing demands for efficient, high-performance electric vehicles.
7. Future Trends in EV Motor Technologies
7.1 Impact on the EV Industry
a. How Innovations May Shape Future Electric Vehicles
These innovations are poised to have a profound impact on the electric vehicle industry. Improved EV motor technologies directly translate to extended driving ranges and better performance, addressing two of the most significant consumer concerns regarding EVs. As motors become more efficient and compact, manufacturers can reduce the size of battery packs or enhance vehicle performance without increasing costs, making EVs more accessible and appealing to a broader market.
Moreover, the adoption of advanced materials and manufacturing processes can lead to lighter and more sustainable vehicles. Reduced material usage and energy-efficient production methods contribute to lower environmental footprints, aligning with global efforts to combat climate change. The ability to produce complex motor components using additive manufacturing also allows for rapid prototyping and customization, enabling manufacturers to innovate faster and tailor products to specific market needs.
These technological advancements may also foster increased collaboration between automotive companies and material science experts, driving further innovation in the industry. As EV motor technologies become more efficient and cost-effective, we can expect to see a surge in EV adoption worldwide. This shift not only benefits consumers through improved vehicle options but also contributes to global sustainability goals by reducing reliance on fossil fuels and decreasing greenhouse gas emissions. The continuous evolution of EV motor technologies thus holds the key to the future of transportation, promising a new era of efficient, high-performance, and eco-friendly vehicles.
8. Conclusion
8.1 Summary of Key Insights
a. The Significance of Advancements in EV Motor Technologies
Throughout this comparative analysis of Tesla, Nissan, and BMW, it becomes clear that advancements in EV motor technologies are pivotal to the success and evolution of electric vehicles. Each manufacturer has adopted unique approaches to motor design, material selection, and manufacturing processes, all aimed at enhancing performance, efficiency, and consumer appeal. Tesla’s utilization of high-grade silicon steel laminations and proprietary motor designs has resulted in motors with exceptional efficiency and power, setting new industry standards for range and acceleration. Nissan’s focus on affordability and practicality demonstrates how thoughtful material selection and cost-effective manufacturing can make electric vehicles accessible to a broader market without significantly compromising performance. BMW’s commitment to delivering a premium driving experience is evident in the i3’s advanced motor systems, which leverage lightweight construction and precision engineering to offer dynamic performance and efficiency.
Stator core laminations have emerged as a common thread among these manufacturers, serving as a critical component in reducing energy losses and improving motor efficiency. Techniques such as using thin, insulated laminations made from specialized electrical steel are employed universally to minimize eddy current and hysteresis losses. However, each company infuses unique innovations into their processes—be it Tesla’s ultra-thin laminations and automated assembly, Nissan’s cost-optimized designs, or BMW’s precision laser cutting and use of unconventional materials. These advancements not only enhance the individual performance of their vehicles but also contribute significantly to the broader progression of electric vehicle technology.