1. Introduction to Progressive Die Stamping
1.1 Overview of the Technique
a. Definition and Purpose
Progressive Die Stamping is a highly efficient metal forming process essential in modern manufacturing. This technique involves a series of precise operations performed sequentially on a metal strip, which moves through multiple stations within a die. Each station performs a specific task, such as bending, cutting, or punching, transforming the raw material into a finished component. This method is particularly advantageous for producing complex parts at high volumes, ensuring both speed and precision.
b. Importance in Modern Manufacturing
In today’s industrial landscape, Progressive Die Stamping is indispensable due to its ability to meet the demanding requirements of various sectors, including automotive, electronics, and aerospace. The process allows manufacturers to produce large quantities of parts quickly and consistently, making it ideal for high-volume production. Its capability to work with various metals, including steel, aluminum, and copper, adds to its versatility. Moreover, the precision of this technique ensures that each part is identical, meeting stringent quality standards. As a result, Progressive Die Stamping not only enhances production efficiency but also reduces costs, making it a preferred choice for manufacturers aiming for excellence in both performance and profitability.
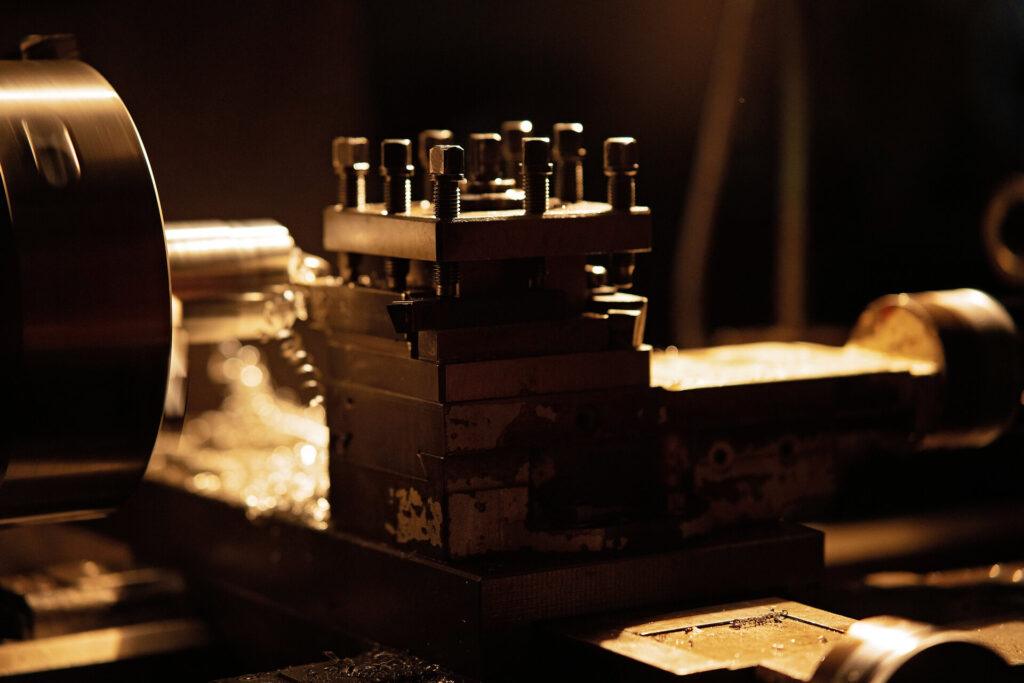
2. The Progressive Die Stamping Process
2.1 Step-by-Step Breakdown
a. Stock Strip Layout and Design
The Progressive Die Stamping process begins with the careful design of the stock strip layout. This initial step involves using advanced modeling techniques to plan out the sequence of operations that will occur within the die. Each station in the die is strategically designed to perform a specific task, such as cutting, bending, or punching. This meticulous planning ensures that the metal strip is transformed efficiently and accurately as it progresses through the die, ultimately achieving the desired shape and dimensions.
b. Tool Steel and Die Set Machining
Following the design phase, the next step involves machining the die set from robust tool steel. Tool steel is chosen for its durability and resistance to wear, which is crucial for maintaining precision over long production runs. During this phase, die blocks are crafted to exact specifications, ensuring each one can perform its designated function within the process. Quality control measures are strictly adhered to, verifying that each die block meets the necessary standards before moving on to the next stage.
c. Grinding and Heat Treating
Once the die blocks are machined, they undergo grinding and heat treating. Grinding is essential for achieving the high dimensional accuracy required for the process. Heat treating, on the other hand, enhances the material’s hardness and durability, enabling it to withstand the stresses of repeated use. These treatments are critical for maintaining the precision and longevity of the die components, ensuring consistent quality in the stamped parts.
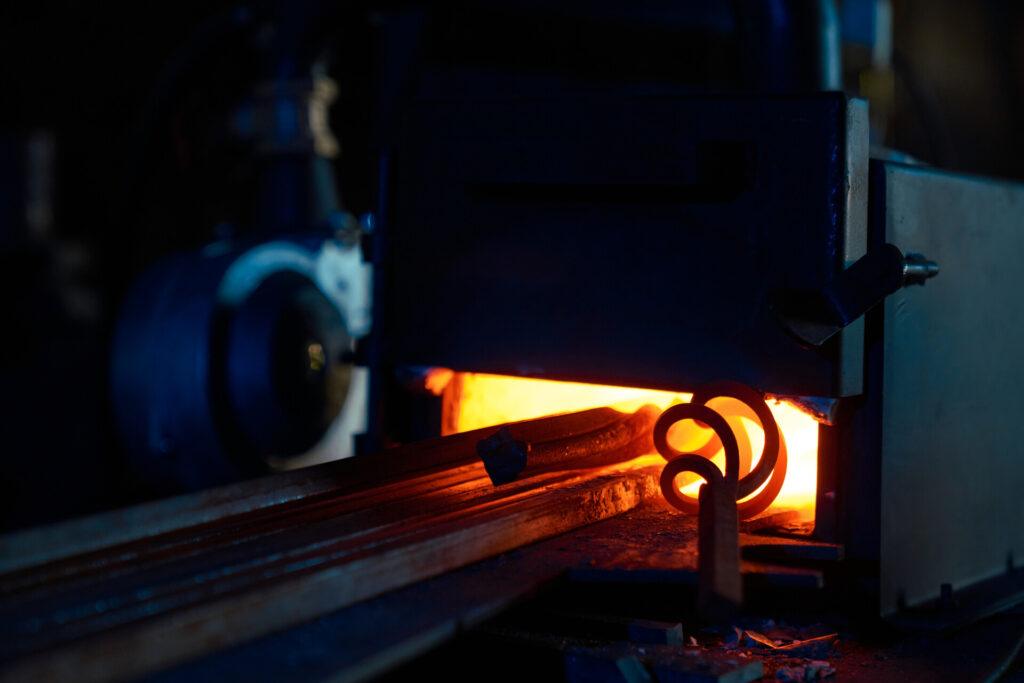
3. Key Benefits of Progressive Die Stamping
3.1 Efficiency and Cost-Effectiveness
a. Increased Production Speed
One of the most significant advantages of Progressive Die Stamping is its ability to drastically increase production speed. This process utilizes a continuous feed mechanism, allowing the metal strip to move through multiple stations within the die without interruption. Each station performs a specific operation, such as cutting or bending, in a single pass, enabling the production of complex components in a fraction of the time required by traditional methods. This continuous flow not only boosts production rates but also minimizes downtime, making it ideal for high-volume manufacturing.
b. Reduced Setup Time
Progressive Die Stamping also excels in reducing setup time compared to other metal forming techniques. The use of a single die to perform multiple operations means that manufacturers do not need to switch out tools or dies for different stages of the process. This streamlines production, reduces labor costs, and minimizes the potential for errors that can occur during tool changes. As a result, manufacturers can achieve faster turnaround times, which is crucial for meeting tight production schedules and responding quickly to market demands.
c. Minimal Material Waste
The process is highly efficient in material usage, which significantly reduces waste. Progressive Die Stamping is designed to maximize the use of the metal strip, carefully planning each operation to minimize scrap. This efficiency is particularly beneficial when working with expensive materials, as it helps lower overall production costs. The precision of the die design ensures that each part is made with exact specifications, reducing the need for additional processing and further conserving resources.
4. Applications and Industries
4.1 Automotive Industry
a. Key Components Manufactured
Progressive Die Stamping plays a critical role in the automotive industry, where precision and efficiency are paramount. This technique is used to manufacture a wide range of components essential to vehicle performance and safety. Key parts include brake calipers, structural frames, and motor cores, all of which require high accuracy and durability. The ability to produce these components in large quantities with consistent quality makes Progressive Die Stamping invaluable for automotive manufacturers. The process allows for the creation of complex geometries and high-strength parts that are crucial for vehicle reliability and efficiency.
4.2 Electronics Industry
a. Intricate Electronic Components
In the electronics industry, Progressive Die Stamping is utilized to produce intricate components that are integral to various devices. This includes connectors, shielding components, and precision parts used in consumer electronics, medical devices, and telecommunications. The process’s high precision is particularly beneficial for producing small parts with tight tolerances, ensuring reliable performance in electronic assemblies. The speed and accuracy of Progressive Die Stamping help meet the high demands of the electronics market, where rapid production cycles and consistent quality are essential.
4.3 Aerospace and Beyond
a. High-Performance Parts
The aerospace industry also benefits significantly from Progressive Die Stamping, where it is used to produce high-performance parts that must withstand extreme conditions. Components such as brackets, housings, and structural elements are manufactured using this method. The process’s ability to handle various metals, including high-strength alloys, makes it ideal for producing parts that require both lightweight properties and high durability. Beyond aerospace, Progressive Die Stamping is employed in industries like medical devices, household appliances, and renewable energy, showcasing its versatility and widespread application.
5. Comparison with Other Metal Forming Techniques
5.1 Progressive Die Stamping vs. Compound Stamping
a. Process Differences
Progressive Die Stamping and Compound Stamping are both vital techniques in metal forming but serve different purposes and are suitable for various applications. Progressive Die Stamping involves a sequence of operations performed at multiple stations within a single die, allowing for the transformation of a metal strip into a finished part in a continuous process. This method is highly efficient for producing complex parts in high volumes, as it can perform multiple operations, such as cutting, bending, and punching, in a single pass through the die.
In contrast, Compound Stamping performs multiple operations in one single press stroke within a single station. This method is often used for simpler parts that require fewer operations, but it can achieve very high precision in each operation. While Compound Stamping is effective for producing components with tighter tolerances and higher accuracy, it is generally less suited for high-volume production compared to Progressive Die Stamping due to the need for more complex dies and longer setup times.
5.2 Choosing the Right Method
a. Factors to Consider
When choosing between Progressive Die Stamping and Compound Stamping, several factors must be considered. The complexity of the part design is a crucial determinant; Progressive Die Stamping is more suited for intricate components with multiple features, while Compound Stamping is ideal for simpler designs requiring high precision. The volume of production also plays a significant role; Progressive Die Stamping is more efficient and cost-effective for large-scale production runs due to its continuous feed mechanism and faster cycle times. Additionally, material considerations, such as the type and thickness of the metal, can influence the choice of technique, as different processes may handle specific materials better.
6. Future Trends in Progressive Die Stamping
6.1 Technological Advancements
a. Automation and Digitalization
The future of Progressive Die Stamping is increasingly being shaped by advancements in automation and digitalization. The integration of automated systems, such as robotic arms and conveyors, is streamlining the handling of materials and parts, significantly enhancing production efficiency. Digital technologies, including computer-aided design (CAD) and computer-aided manufacturing (CAM), are playing crucial roles in the precise design and execution of dies. Additionally, the use of sensors and real-time monitoring systems enables manufacturers to track the stamping process closely, ensuring consistent quality and allowing for immediate adjustments. These advancements not only boost productivity but also reduce the likelihood of errors and downtime, leading to more reliable and cost-effective operations.
6.2 Sustainable Practices
a. Reducing Environmental Impact
As industries worldwide emphasize sustainability, Progressive Die Stamping is evolving to incorporate more environmentally friendly practices. One key trend is the increased focus on minimizing material waste through optimized die design and precise material usage. Advanced simulation tools are being used to predict and reduce scrap rates, leading to more efficient use of raw materials. Moreover, there is a growing shift towards using recyclable materials and eco-friendly lubricants in the stamping process, which helps reduce the overall environmental footprint. Energy efficiency is another critical area of focus, with manufacturers adopting energy-saving technologies and practices, such as efficient press machines and renewable energy sources, to power their operations.
7. Conclusion
Progressive Die Stamping stands as a cornerstone in modern manufacturing, offering unparalleled efficiency and precision. This technique’s ability to produce complex parts in high volumes has made it indispensable across various industries, including automotive, electronics, and aerospace. The ongoing advancements in automation, digitalization, and sustainable practices further enhance its appeal, ensuring that the process meets the evolving demands of today’s industrial landscape. As manufacturers continue to innovate and improve, Progressive Die Stamping remains a critical component in achieving cost-effective and high-quality production, paving the way for future growth and development.
Explore our Progressive Die Setup services, designed to optimize your production process with precision and efficiency. Reach out to learn how we can support your manufacturing goals with our expertise.