1. Introduction
1.1 Importance and Scope of Motor Laminations
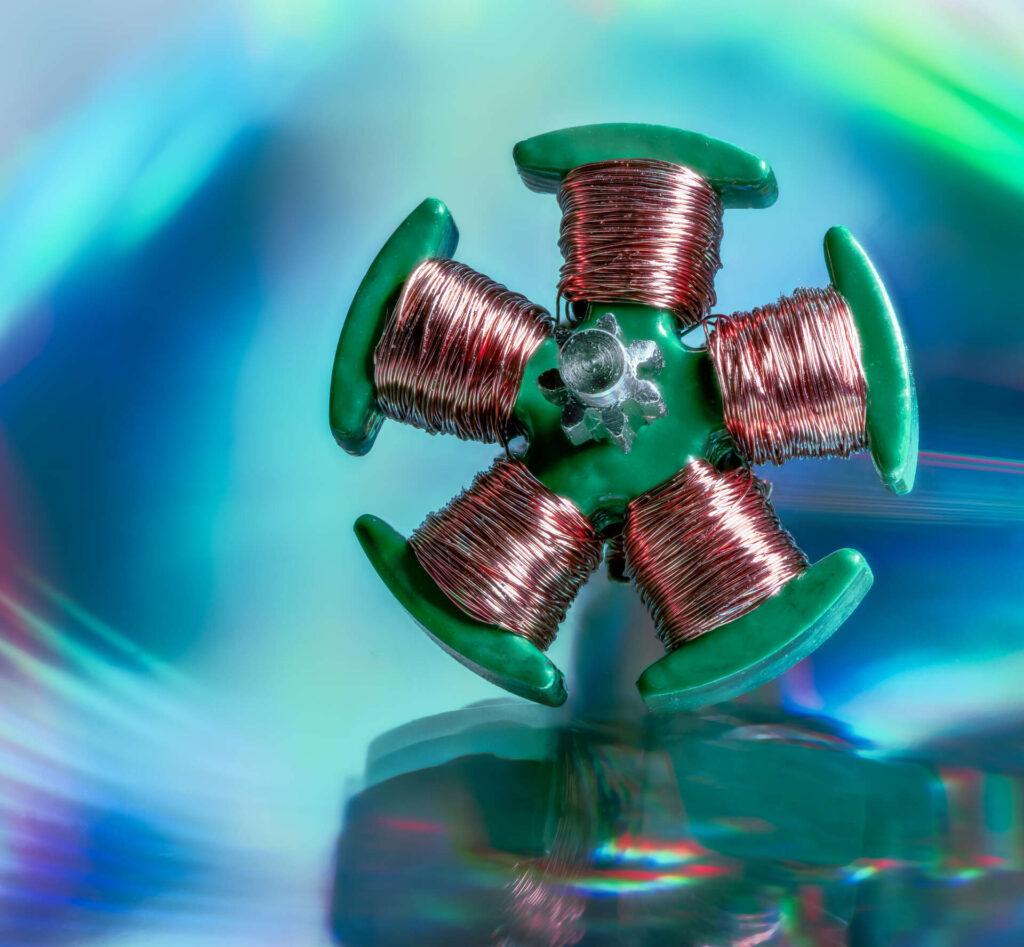
Motor laminations are indispensable components in modern electrical engineering, playing a crucial role in enhancing motor efficiency and reducing energy consumption. Typically made from silicon steel, known for its excellent magnetic properties and low core loss, silicon steel helps to minimize heat and energy loss during motor operation, thereby enhancing overall efficiency. Motor laminations are extensively used in various motor designs, including but not limited to home appliances, electric vehicles, industrial machinery, and power generation systems. The specific requirements for the performance and quality of motor laminations dictate the choice of materials and processes in their manufacturing.
1.2 Article Overview
This article delves into the manufacturing processes of motor laminations, exploring stages from material selection and fabrication to post-processing. We will detail how these stages impact the performance of motor laminations and their significance in ensuring the highest product quality standards. Through this article, readers will gain a comprehensive understanding of the core technologies and processes involved in motor lamination manufacturing, which is invaluable for professionals in related industries.
2. Basic Concepts of Motor Laminations
2.1 Definition of Motor Laminations
Motor laminations, also known as electric core laminations, are precisely manufactured thin, wide strips of silicon steel used to form the magnetic path in motors or generators. These laminations have high magnetic permeability, primarily functioning to reduce energy loss during motor operation. The use of silicon steel is crucial due to its low silicon content, which significantly reduces hysteresis and eddy current losses, key to enhancing motor efficiency.
2.2 Function and Role of Motor Laminations
The primary function of motor laminations is to form an effective magnetic circuit, minimizing magnetic reluctance, which is vital for enhancing the overall efficiency of the motor. During motor operation, these laminations help reduce heat generation, thereby extending the motor’s lifespan and enhancing energy efficiency. Moreover, well-designed motor laminations can also reduce noise and vibration, making the motor operate more smoothly and quietly. The design and manufacturing quality of the laminations directly impact motor performance, thus precise manufacturing techniques and material selection are extremely important.
3. Manufacturing Process of Motor Laminations
3.1 Material Selection
Choosing the right materials is the first step in the manufacturing of motor laminations. Typically, silicon steel is the preferred material for motor laminations due to its excellent magnetic properties and high electrical resistance, effectively reducing energy loss. The thickness, silicon content, and crystal structure of the silicon steel can all affect the final performance of the laminations. High-quality silicon steel can enhance the magnetic permeability of the laminations and reduce energy consumption, crucial for ensuring motor efficiency and durability.
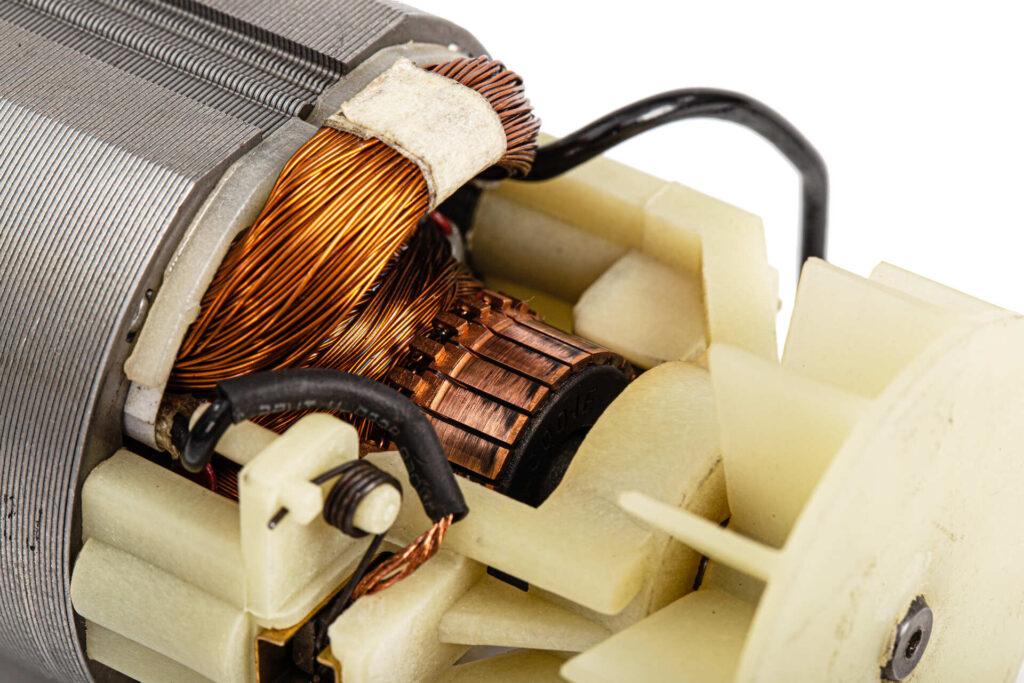
3.2 Manufacturing Techniques
The manufacturing of motor laminations typically involves precision stamping processes, which require specialized dies to cut and shape the silicon steel. The accuracy of the stamping process directly affects the dimensional accuracy and edge smoothness of the laminations, which are key determinants of motor performance. Additionally, some manufacturing processes employ laser cutting technology to enhance cutting precision and reduce material waste.
3.3 Surface Treatment
After stamping, motor laminations usually undergo surface treatment to enhance their corrosion resistance and insulation properties. A common treatment method is the application of an insulating varnish layer, which not only prevents short circuits between cores but also enhances overall environmental adaptability. Additionally, this protective coating helps reduce hysteresis losses during operation, further enhancing the motor’s efficiency and lifespan.
4. Quality Control in Manufacturing
4.1 Testing and Evaluation
During the manufacturing process of motor laminations, testing and evaluation are crucial for ensuring product quality. Multiple testing methods are used, including dimensional accuracy tests, magnetic performance testing, and electrical insulation tests, to ensure that each lamination meets strict performance standards. Dimensional accuracy tests ensure precise assembly of the laminations, magnetic performance testing evaluates whether the silicon steel’s magnetic permeability meets expected outcomes, and electrical insulation tests ensure the insulating performance between laminations to prevent electrical faults during operation.
4.2 Common Issues and Solutions
Various issues may arise during the manufacturing of motor laminations, such as material defects, imprecise stamping, or uneven surface treatment. Developing effective strategies to address these issues is key. For instance, improving the quality control standards of raw materials can reduce material defects; enhancing stamping equipment and techniques can improve the precision of the finished product; and for surface treatment issues, optimizing the coating process or adjusting the coating material formula can solve the problem. These strategies not only help improve product quality but also reduce production costs and enhance efficiency.
5. Future Trends and Innovations in Motor Laminations
5.1 Technological Innovations
As technology advances, motor lamination manufacturing techniques continue to innovate. A significant trend is the use of high-precision CNC machines and laser cutting technology to improve manufacturing accuracy and material utilization. Additionally, 3D printing technology is beginning to be used for prototyping and small-scale production of motor laminations, which not only accelerates the development process but also allows for more complex designs that are difficult to achieve with traditional manufacturing techniques.
6. Conclusion
6.1 Key Review
This article has detailed the manufacturing process of motor laminations, from material selection and precision manufacturing techniques to strict quality control measures, each step ensuring that motor laminations meet the highest performance standards. High-quality motor laminations not only enhance motor efficiency and lifespan but also reduce energy consumption and operating costs. Additionally, the article explores the innovative trends and sustainability developments in motor lamination technology, which are crucial factors driving industry advancement.
6.2 Future Outlook
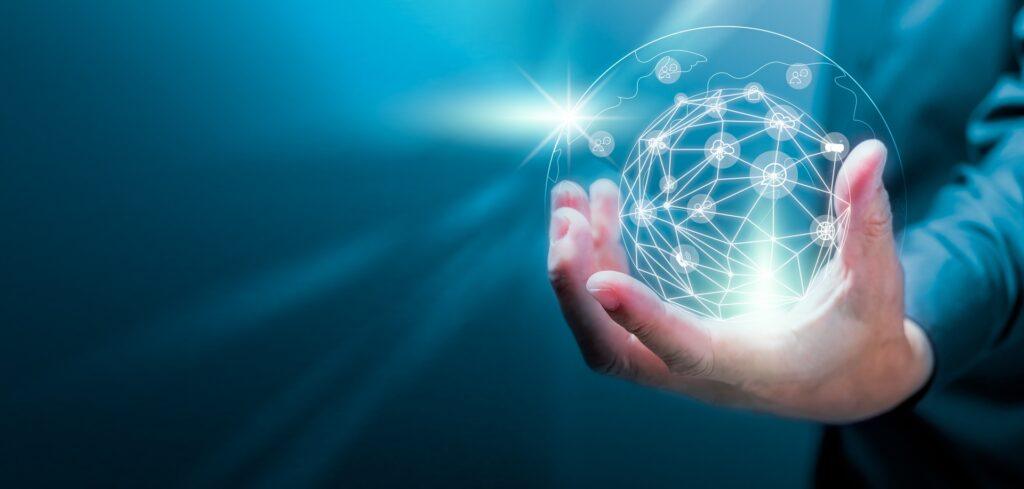
As technology continues to advance and market demands change, motor lamination manufacturing techniques are expected to continue innovating. Future developments may focus on improving production efficiency, reducing costs, and enhancing environmental performance. Additionally, as electric vehicles and renewable energy equipment become more widespread, the demand for high-efficiency motor laminations will further increase. Therefore, mastering these technological trends is essential for professionals in related industries to ensure they can meet future market demands
※Further Reading: What is a Motor Core? A Breakdown of 5 Key Functions
External Links: https://www.researchgate.net/publication/249350123_The_Cortical_Lamination_of_the_Motor_Area_of_the_Brain
Source reference from: https://www.researchgate.net/