1. Motor Core Introduction
Motor laminations are key components in the manufacturing of electric motors and generators. This introduction lays the foundation for understanding the critical role motor laminations play in enhancing motor performance and efficiency.
1.1 Overview of Motor Laminations
Motor laminations involve using thin metal sheets, typically silicon steel, stacked and bonded together to form the core of electric motors or generators. These laminations perform several essential functions, including reducing energy losses due to eddy currents, improving magnetic performance, and providing structural integrity.
1.1.1 What are Motor Laminations ?
Motor laminations refer to the process of creating the core components of electric motors or generators by stacking multiple layers of thin magnetic conductive materials, typically silicon steel. These thin sheets minimize eddy currents—circular electric currents induced by changing magnetic fields—leading to energy loss and heat within the core.
1.1.2 Importance of Motor Laminations
The efficiency of an electric motor largely depends on the quality of its laminations. Proper laminations ensure minimal energy loss in the form of heat, thus optimizing motor performance. Additionally, well-designed laminations improve the motor’s magnetic flux density, enabling it to deliver higher torque at the same power input.
1.2 Key Functions and Benefits of Motor Laminations
Motor laminations play a crucial role in achieving high efficiency and performance in motors and generators. Their design and material composition directly affect the overall performance of these machines.
1.2.1 Structural Support
Motor laminations provide strong structural support for various internal components of the motor. By securing parts such as the rotor, stator, coils, and casing, the laminations prevent mechanical failure due to vibration or operational pressure, ensuring smooth motor operation under various conditions.
1.2.2 Magnetic Field Enhancement
One of the primary functions of motor laminations is to enhance the magnetic performance of the motor. The lamination design focuses the magnetic field generated by the motor coils. This concentration of the magnetic field increases motor efficiency, effectively converting more electrical energy into mechanical energy.
This introduction sets the stage for an in-depth exploration of the specific functions of motor laminations and the technological innovations aimed at optimizing motor performance. As we further explore the critical role of motor laminations, we will reveal how this foundational element not only supports but actively enhances the operational capabilities of modern electric motors and generators.
2. Functions and Benefits of Motor Laminations
Motor laminations not only provide structural support to the motor but also enhance overall performance by optimizing the magnetic flux path. The following section will delve into how laminations reduce magnetic resistance and improve permeability.
2.1 Optimization of Magnetic Flux Paths
The design of motor laminations is crucial to ensuring the efficiency of magnetic flux paths, directly impacting motor performance and energy efficiency.
2.1.1 Design Methods for Reducing Magnetic Resistance
The shape and material selection of laminations are critical for reducing magnetic resistance. High-permeability silicon steel can effectively lower magnetic resistance, thus improving magnetic flux efficiency. Precise cutting and arrangement of the laminations reduce air gaps, a key step in improving magnetic path continuity and lowering magnetic resistance. Empirical data shows that optimized lamination design can increase magnetic flux efficiency by 10% to 15%.
2.1.2 Case Study: Efficiency Gains from Optimized Magnetic Flux Paths
For instance, in high-performance motor design, using thinner laminations with more precise stacking techniques significantly reduces losses in the magnetic path. A study indicated that improving lamination arrangement can reduce magnetic resistance by about 20%, particularly important for industrial motors requiring high torque output.
2.2 Improved Structural Stability and Vibration Reduction
The structural design of motor laminations is critical in enhancing motor operational stability and lifespan.
2.2.1 How Lamination Structure Improves Mechanical Stability
The mechanical stability of laminations ensures the reliability of the motor under high-speed or heavy-load conditions. Silicon steel laminations, with high strength and good elasticity, absorb and dissipate vibrations during operation, preventing structural damage due to fatigue.
2.2.2 Design Considerations for Noise Reduction
Proper lamination design significantly reduces the noise generated during motor operation. For instance, using acoustic simulation software to optimize lamination geometry can predict and minimize noise production, especially in household appliances and office equipment.
2.3 Heat Management Strategies
Proper lamination design is also critical for effective heat management, which directly affects motor efficiency and lifespan.
2.3.1 Application of Cooling Techniques
Laminations improve heat conduction paths, aiding the motor in more efficient heat dissipation. The high thermal conductivity of silicon steel enhances magnetic performance and accelerates heat dissipation from the core components to the exterior, preventing overheating and extending motor lifespan.
2.3.2 New Materials and Heat Dissipation Solutions
Ongoing research explores new materials such as carbon fiber or high-thermal conductivity plastics for laminations, offering better heat dissipation performance, particularly crucial for motors operating in extreme environments.
3. Reducing Energy Losses
Precise motor lamination design is essential in minimizing energy losses, particularly in reducing eddy current and hysteresis losses, which can significantly improve overall electrical efficiency.
3.1 Controlling Eddy Currents and Hysteresis Losses
The eddy current and hysteresis losses generated during motor operation are two major factors affecting efficiency. These losses can be significantly reduced through improvements in lamination design and material selection.
3.1.1 How to Reduce Eddy Current Losses
Eddy current losses occur when changing magnetic fields induce currents in the laminations, generating heat that leads to energy loss. Using thin, high-permeability silicon steel laminations can effectively reduce such losses. Studies show that thinner laminations can reduce eddy current losses by 25%, as thinner laminations limit the path of eddy currents, reducing heat loss.
3.1.2 Strategies for Lowering Hysteresis Losses
Hysteresis losses result from the periodic reversal of the magnetic field, related to the material’s hysteresis curve. Using silicon steel with high permeability and low silicon content reduces hysteresis losses. Research indicates that proper heat treatment and cold rolling processes improve the microstructure of silicon steel, reducing hysteresis losses by about 15%.
3.2 Improving Electrical Efficiency
Optimizing lamination design not only reduces losses but also improves the motor’s electrical efficiency.
3.2.1 Impact of Lamination Design on Electrical Efficiency
A well-designed lamination ensures uniform magnetic field distribution, enhancing current efficiency in the coils. For example, a uniform magnetic field ensures even current distribution in the coils, reducing local overheating and thus improving electrical efficiency. Practical applications show that this design can boost electrical efficiency by at least 10%.
3.2.2 Impact of Efficiency Gains on Motor Lifespan
Improved electrical efficiency also extends the motor’s operational lifespan. Increased efficiency reduces thermal stress during operation, critical for extending the lifespan of the laminations and the entire motor assembly. Statistics show that each 1% increase in efficiency can extend motor life expectancy by 5%.
4. Enhancing Structural Stability and Vibration Damping
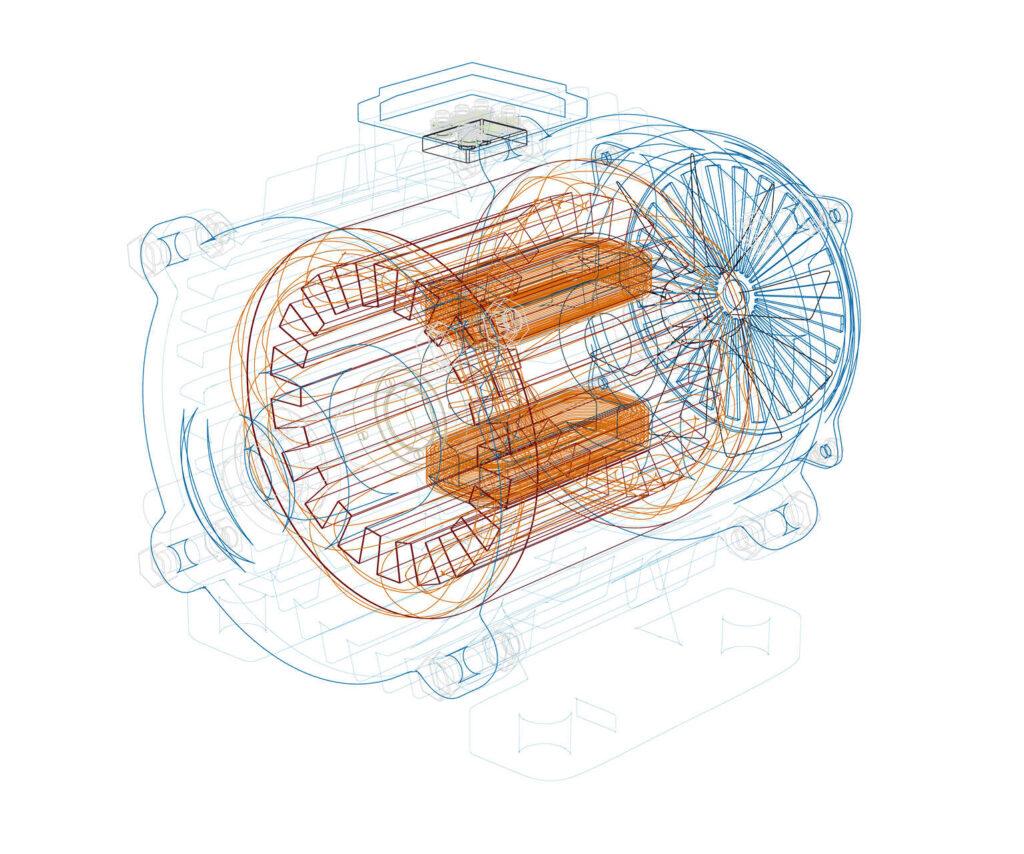
Optimizing motor lamination design not only improves energy efficiency but also plays a crucial role in ensuring motor structural stability and vibration damping during high-load operations. This section explores how laminations enhance operational stability and reduce noise and vibration through their structural design.
4.1 The Importance of Structural Stability
Structural stability is the foundation for ensuring long-term reliable motor operation, particularly under high-speed or high-load conditions.
4.1.1 How Laminations Provide Structural Stability
Motor laminations form a solid core structure through precise stacking, providing necessary support for rotating parts inside the motor. This design reduces movement and wear of components during operation, improving overall mechanical strength and extending motor lifespan.
4.1.2 Design Strategies for Preventing Mechanical Failures
Advanced technologies such as Computational Fluid Dynamics (CFD) and Finite Element Analysis (FEA) can be used during the design phase to predict and minimize potential structural issues, such as material fatigue caused by vibration or thermal stress.
4.2 Design Considerations for Noise Reduction
Precise lamination design is key to reducing noise and vibration during motor operation, critical for improving user experience and satisfaction.
4.2.1 Application of Vibration Damping Technologies
Each layer of silicon steel laminations is typically insulated, preventing short circuits and helping absorb operational vibrations, reducing noise. In some high-end motors, special damping materials are integrated into the lamination structure to further reduce vibration.
4.2.2 Structural Innovations for Noise Reduction
Modern motor design increasingly employs modal analysis to optimize lamination shape and configuration. This method predicts and avoids resonance frequencies that may cause vibration during operation, effectively reducing operating noise.
5. Heat Management Strategies
Effective heat management is crucial for maintaining motor efficiency and longevity. By designing motor laminations with precision and selecting appropriate materials, the heat generated during motor operation can be effectively controlled, preventing overheating and improving performance.
5.1 Application of Cooling Techniques
Heat generation is inevitable during motor operation, but effective cooling techniques can greatly improve the motor’s operational efficiency and safety.
5.1.1 Importance of Heat Dissipation Mechanisms
Motor laminations enhance heat dissipation by increasing thermal conductivity. Using high-thermal conductivity materials such as silicon steel helps quickly transfer internal heat to the motor’s exterior, reducing the risk of sudden temperature rises and protecting internal components from damage.
5.1.2 Innovations in Lamination Design for Heat Dissipation
Modern lamination design considers the optimal path for heat flow. By altering the arrangement and shape of laminations, the flow of heat from the source to the cooling surface is optimized. Some high-performance motors use lamination designs with special ventilation holes to enhance airflow, further promoting heat dissipation.
5.2 New Materials and Heat Dissipation Solutions
With technological advancements, the development of new materials and heat dissipation solutions offers more possibilities for motor thermal management.
5.2.1 Application of New Materials
Research into new materials, such as high-thermal conductivity composites or modified silicon steel, has become a focus of innovation in lamination technology. These materials more effectively manage heat, reducing the risk of performance degradation and failure due to overheating.
5.2.2 Advances in Cooling Technology
Emerging cooling technologies such as the use of phase-change materials or liquid cooling systems are beginning to be applied in high-power motors requiring stringent thermal management. These technologies can address heat dissipation issues without significantly increasing costs.
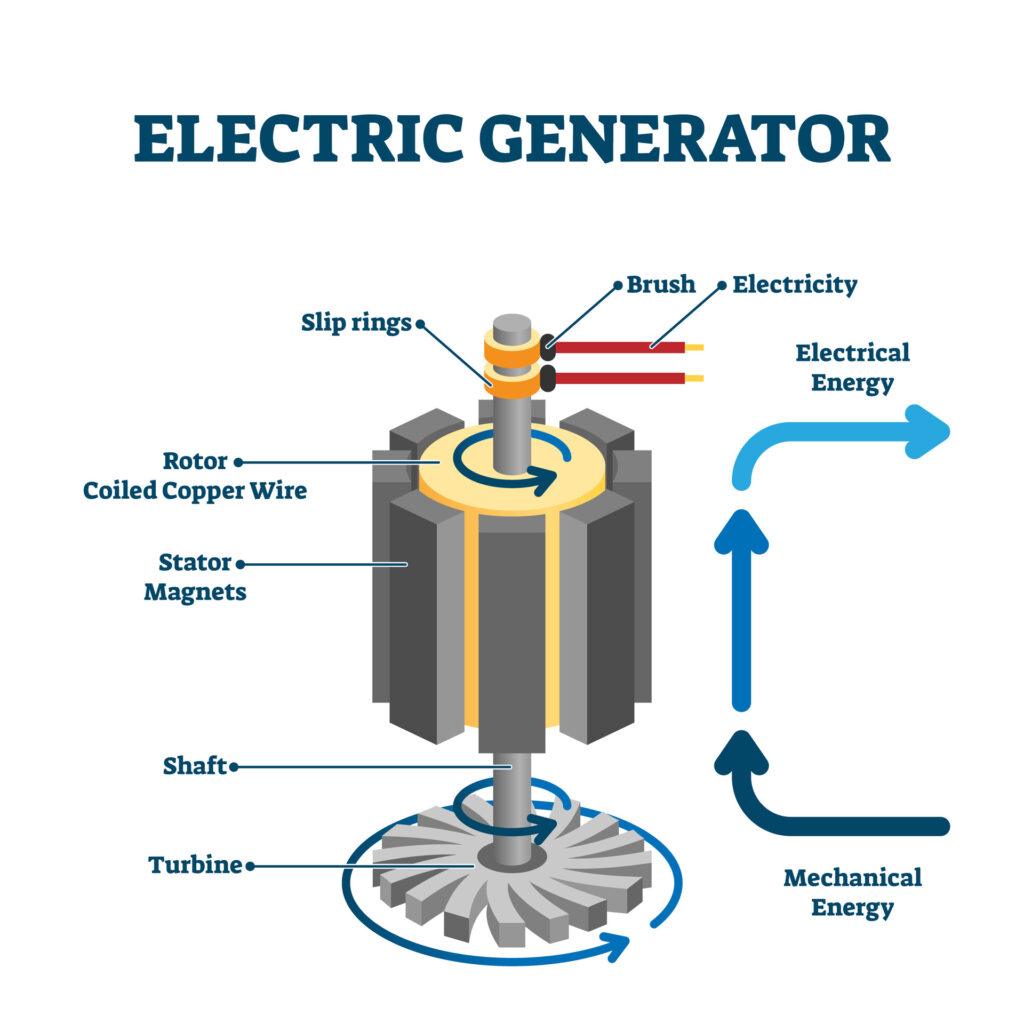
6. Market Applications and Future Outlook
Exploring the application of motor lamination technology across various industries and predicting future development trends helps us understand the market impact and innovation potential of this technology.
6.1 Applications of Motor Laminations in Various Industries
Innovations in motor lamination technology have brought broad application prospects, especially in demanding industrial and consumer electronics markets.
6.1.1 Consumer Electronics and Household Appliances
In household appliances such as washing machines, dryers, and vacuum cleaners, motor laminations must withstand high-temperature and high-vibration environments while maintaining efficient operation. These applications typically require lamination designs that offer excellent heat dissipation and high structural stability to extend product life and reduce maintenance costs.
6.1.2 Industrial Automation and Robotics
Motor laminations in industrial robots and automation equipment demand high precision and repeatability. Lamination technology provides precise magnetic field control and high-efficiency energy conversion, ensuring more stable operation and improved energy efficiency.
6.2 Technological Innovations and Development Trends
With continuous technological progress, innovations in motor laminations not only drive the expansion of existing markets but also create possibilities for emerging applications.
6.2.1 Opportunities in Emerging Markets
As demand for electric vehicles and renewable energy equipment increases, motor lamination technology faces new opportunities and challenges. These applications require extremely high energy conversion efficiency and reliability. Innovations in motor laminations can meet these demands, especially in improving energy efficiency and reducing carbon footprints.
6.2.2 Predictions for Technological Development
In the future, motor lamination technology is expected to evolve toward greater integration and intelligence. Using Internet of Things (IoT) technology, motor laminations can enable smarter data monitoring and performance regulation, significantly improving motor operational efficiency and fault prediction capabilities.
7. Conclusion
This comprehensive discussion of motor lamination technology highlights its key role in improving motor performance and calls for continuous innovation and collaboration within the industry to drive technological progress and market development.
7.1 Reaffirming the Importance of Motor Lamination Technology
Motor lamination technology is the cornerstone of motor and generator performance, with innovations directly impacting equipment efficiency, lifespan, and reliability.
7.1.1 Contributions of Motor Laminations to Performance Improvement
Motor laminations effectively enhance motor performance and energy efficiency through key technologies such as optimizing magnetic flux paths, reducing energy losses, improving structural stability, and heat management. These innovations not only make motor operation more efficient but also extend motor lifespan and reduce maintenance costs.
7.1.2 The Key Role of Motor Lamination Technology in Modern Industry
With the continuous development of industrial automation and smart manufacturing, advancements in motor lamination technology provide more reliable and energy-efficient power solutions across various industries. From household appliances to industrial robots, from electric vehicles to renewable energy systems, motor laminations have widespread applications, directly impacting the market competitiveness of products.
7.2 Call for Continuous Innovation and Research
Continuous innovation and research are essential for maintaining technological leadership and meeting the growing demands of the market.
7.2.1 Emphasizing the Need for Technological Innovation
In the context of global energy conservation and emission reduction, innovations in motor lamination technology are particularly important. Future developments must balance improving energy efficiency with reducing environmental impact, requiring the industry to continually explore new materials, processes, and designs.
7.2.2 Promoting the Importance of Industry-Academia Collaboration
Strengthening collaboration between enterprises, universities, and research institutions is crucial for the research and application of new technologies. Sharing resources and conducting cooperative research can accelerate the transition from laboratory to market, promoting the healthy development of the entire industry.
This conclusion highlights the critical role of motor lamination technology in driving improvements in motor performance and meeting the demands of modern industries. It also calls for continuous technological innovation and deeper collaboration. With ongoing advancements and diversified market demands, motor lamination technology holds great potential for future development and is expected to play an even greater role in many key fields.
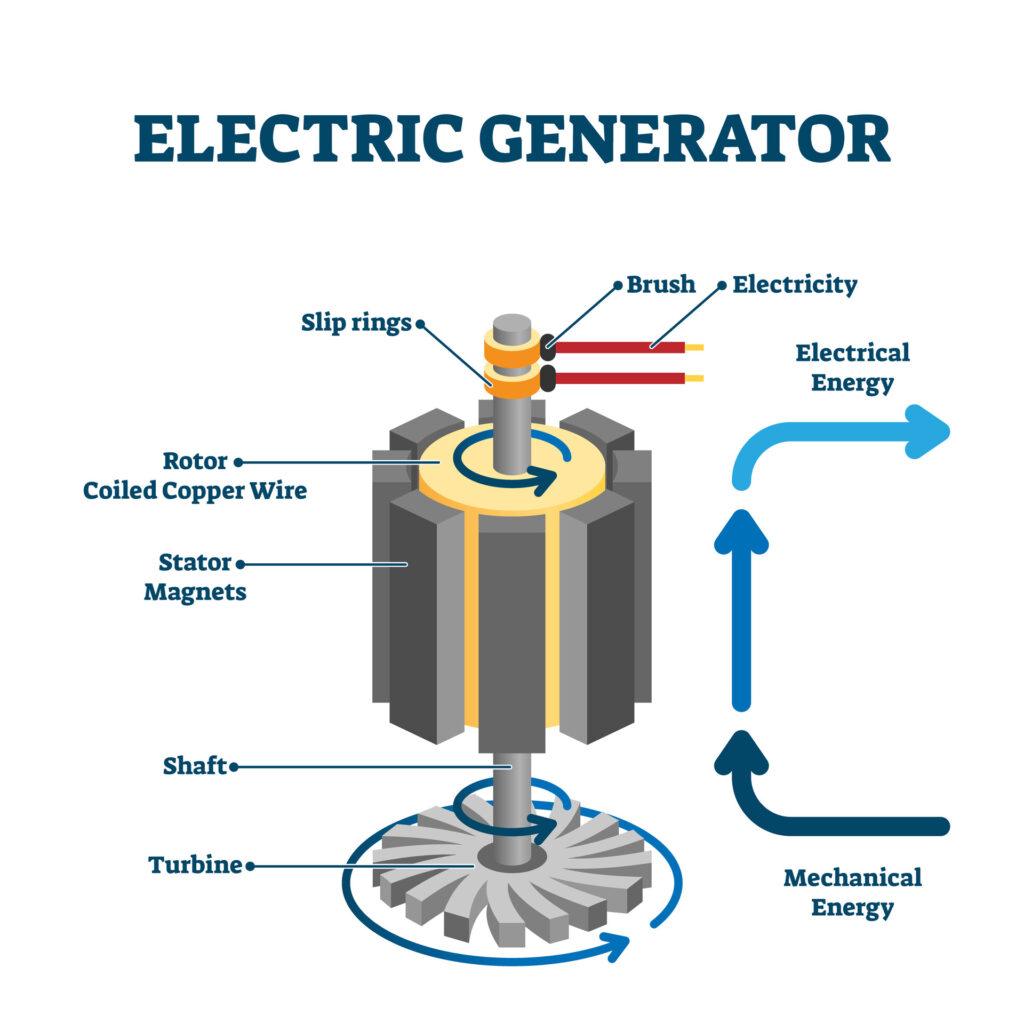
Further Reading: The Future of Urban Mobility: How Electric Motor Cores Are Powering Next-Gen Elevators and Escalators
External Links:https://www.researchgate.net/publication/379520585_Magnetostriction_Vibration_and_Acoustic_Noise_in_Motor_Stator_Cores
Source referenced from www.researchgate.net/