1. Introduction
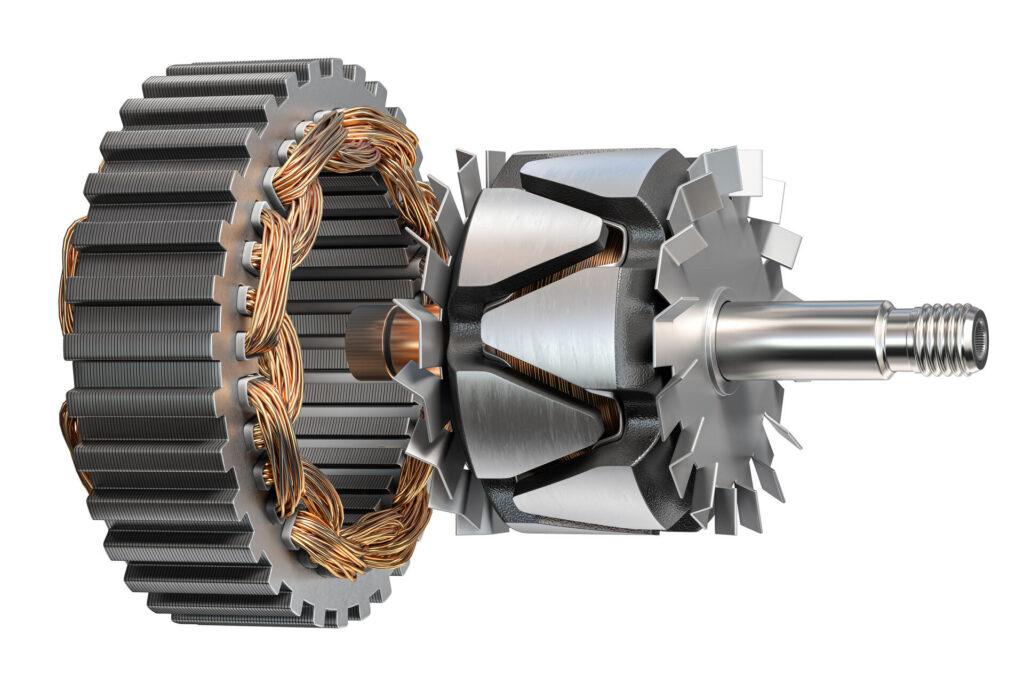
1.1 Overview of High Efficiency Electric Motors
High-efficiency electric motors are specifically designed to convert electrical energy into mechanical energy with minimal losses. These motors have become increasingly important due to their ability to save energy, reduce operational costs, and lower greenhouse gas emissions. In fact, electric motors account for nearly 45% of global electricity consumption, making their efficiency a critical factor in industrial, commercial, and residential applications. By reducing energy consumption, high-efficiency motors not only cut costs but also contribute to environmental sustainability by minimizing carbon footprints.
At the heart of every electric motor lies the motor core, which plays a crucial role in determining the motor’s overall efficiency. The core, usually made of ferromagnetic materials, is responsible for guiding and amplifying the magnetic fields needed to generate torque. A high-efficiency motor core minimizes losses related to magnetization, such as hysteresis and eddy current losses, and ensures that the motor operates with minimal wasted energy. Thus, optimizing the motor core is key to achieving superior motor efficiency.
1.2 Purpose of the Blog Post
The purpose of this blog post is to provide an in-depth understanding of what a high-efficiency motor core is and why it is vital for modern electric motors. We will explore its design, material composition, and performance characteristics, offering insights into how these cores contribute to enhanced efficiency in various applications, from industrial motors to electric vehicles. This post will also discuss the implications of high-efficiency motor cores for energy savings, regulatory compliance, and the future of electric motor technology. By the end of this article, readers will have a clearer understanding of the critical role motor cores play in the efficiency and performance of electric motors across different industries.
2. Understanding the Basics of Electric Motor Cores
2.1 What is an Electric Motor Core?
An electric motor core is a critical component within an electric motor responsible for creating and maintaining the magnetic fields necessary for operation. The core typically consists of two major parts: the stator and the rotor. The stator is the stationary part that generates the magnetic field, while the rotor is the moving part that interacts with the magnetic field to produce rotational motion, generating mechanical energy.
The motor core is made up of thin layers of magnetic material, commonly referred to as laminations, stacked together to minimize energy losses caused by eddy currents. These laminations are often made of ferromagnetic materials such as silicon steel, which have excellent magnetic properties and help reduce hysteresis losses (energy lost in reversing the magnetic field direction). The overall performance of the electric motor is heavily dependent on the quality and efficiency of its core.
2.2 The Relationship Between Motor Core and Efficiency
The design and material quality of the motor core have a direct influence on the motor’s efficiency. Two main types of losses affect the motor core’s efficiency: hysteresis losses and eddy current losses. Hysteresis losses occur as the magnetic field within the core reverses direction during motor operation, resulting in energy dissipation in the form of heat. Eddy current losses arise from circulating currents induced within the core due to changing magnetic fields, also causing energy loss in the form of heat.
High-efficiency motor cores are designed to minimize these losses by using materials with lower hysteresis and electrical resistivity, such as silicon steel. Additionally, the thickness of the laminations plays a crucial role in reducing eddy currents—thinner laminations reduce the size of the circulating currents, thereby minimizing losses. By improving these factors, high-efficiency motor cores can significantly boost the overall energy efficiency of electric motors, leading to better performance and lower operating costs across various applications.
3. Characteristics of a Energy-efficient Motor Core
3.1 Low Core Losses
A defining feature of high-efficiency motor cores is their ability to minimize core losses, which are primarily made up of hysteresis and eddy current losses. To reduce these losses, high-efficiency motor cores use materials with high electrical resistivity and optimized magnetic properties. One common solution is the use of silicon steel, which has a high resistivity that helps mitigate eddy current formation. Additionally, the thickness of the laminations is reduced, with thinner layers being more effective at lowering eddy currents, as they limit the size of these circulating currents within the core.
3.2 Superior Magnetic Properties
High-efficiency motor cores are designed with superior magnetic properties, such as high magnetic permeability and low coercivity, to ensure efficient energy conversion. Magnetic permeability is the core material’s ability to support the formation of magnetic fields, while coercivity refers to the material’s resistance to demagnetization. Materials with high permeability allow for the easy generation of magnetic fields with minimal energy input, while low coercivity materials reduce the energy required to reverse the magnetic fields during operation.
These properties are critical for maintaining motor efficiency across different load conditions. For example, materials like grain-oriented silicon steel are specifically engineered for superior magnetic alignment, which minimizes losses and enhances performance, particularly in high-demand applications like transformer cores.
3.3 Heat Management and Thermal Efficiency
Effective heat management is essential for high-efficiency motor cores, as excessive heat can reduce performance and shorten motor lifespan. The core’s design and material choice directly affect the motor’s ability to dissipate heat. High-efficiency cores are typically constructed from materials with excellent thermal conductivity, such as laminated silicon steel, which can efficiently manage heat generation during operation.
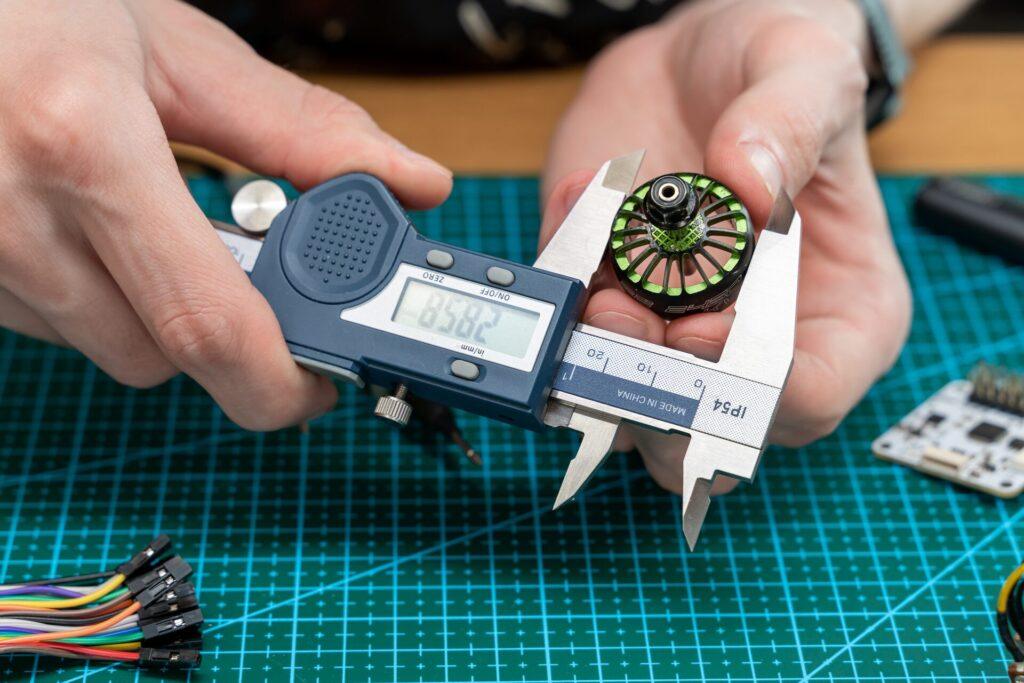
Laminated cores are particularly effective in heat management because they limit eddy currents and their associated heat production. Additionally, high-efficiency cores are designed to reduce internal friction and losses, further decreasing heat buildup. By managing heat effectively, these cores enhance motor reliability, performance, and durability, even under heavy-duty conditions.
4. Most Common Materials Used in Energy-efficient Motor Cores
4.1 Silicon Steel
Silicon steel is one of the most widely used materials for high-efficiency motor cores due to its excellent magnetic properties and cost-effectiveness. It is an alloy of iron and silicon, with silicon content typically ranging between 2% to 4%. The addition of silicon enhances the electrical resistivity of the steel, which helps to reduce eddy current losses within the motor core. Silicon steel also improves the magnetic permeability of the core, allowing the motor to generate stronger magnetic fields with less energy, thus increasing the overall efficiency.
There are two main types of silicon steel used in motor cores: grain-oriented and non-grain-oriented. Grain-oriented silicon steel is engineered to have superior magnetic properties in a specific direction, making it ideal for transformers and certain types of motors that operate with constant magnetic field directions. On the other hand, non-grain-oriented silicon steel has uniform magnetic properties in all directions, which makes it more suitable for motors where the magnetic field changes directions frequently, such as in industrial motors and electric vehicles. The thin laminations of silicon steel also contribute to reducing hysteresis and eddy current losses, ensuring the motor core operates at high efficiency.
5. How Energy-efficient Motor Cores Are Manufactured
5.1 Precision Manufacturing Techniques
Precision manufacturing is crucial for creating high-efficiency motor cores, as even small imperfections can lead to increased energy losses. One of the manufacturing techniques is Wire EDM cutting, which ensures that the laminations used in motor cores are cut with precision. This process minimizes burrs and imperfections along the edges, reducing the chances of energy losses caused by uneven magnetic fields or increased eddy currents. The precision offered by Wire EDM cutting is particularly beneficial for small-batch production demands.
Thin lamination stacking is another vital manufacturing process used to improve efficiency. The laminations, typically made from silicon steel or other advanced materials, are stacked together to form the core. Thin laminations are essential for minimizing eddy currents because they reduce the pathways available for circulating currents within the core. The use of thin laminations, often as small as 0.2mm or less, can significantly enhance the motor’s overall efficiency by reducing both eddy current and hysteresis losses.
5.2 Advanced Coating and Insulation Methods
Advanced coating and insulation techniques are employed to further improve the performance of high-efficiency motor cores by minimizing losses and preventing electrical shorts. Insulating films, typically made from varnishes or polymers, are applied between the thin laminations during manufacturing. These films help to reduce the formation of eddy currents by electrically isolating the individual laminations. Additionally, coatings such as epoxy varnishes are often applied to the surface of the core to provide an extra layer of protection against environmental factors like moisture and heat, which could otherwise degrade the motor’s performance over time.
Another emerging technique is the application of nano-coatings, which can be used to enhance both insulation and thermal management properties. These ultra-thin coatings provide exceptional resistance to heat buildup and electrical losses, making them ideal for motors that operate under high stress or in extreme environments.
6. Applications of Energy-efficient Motor Cores
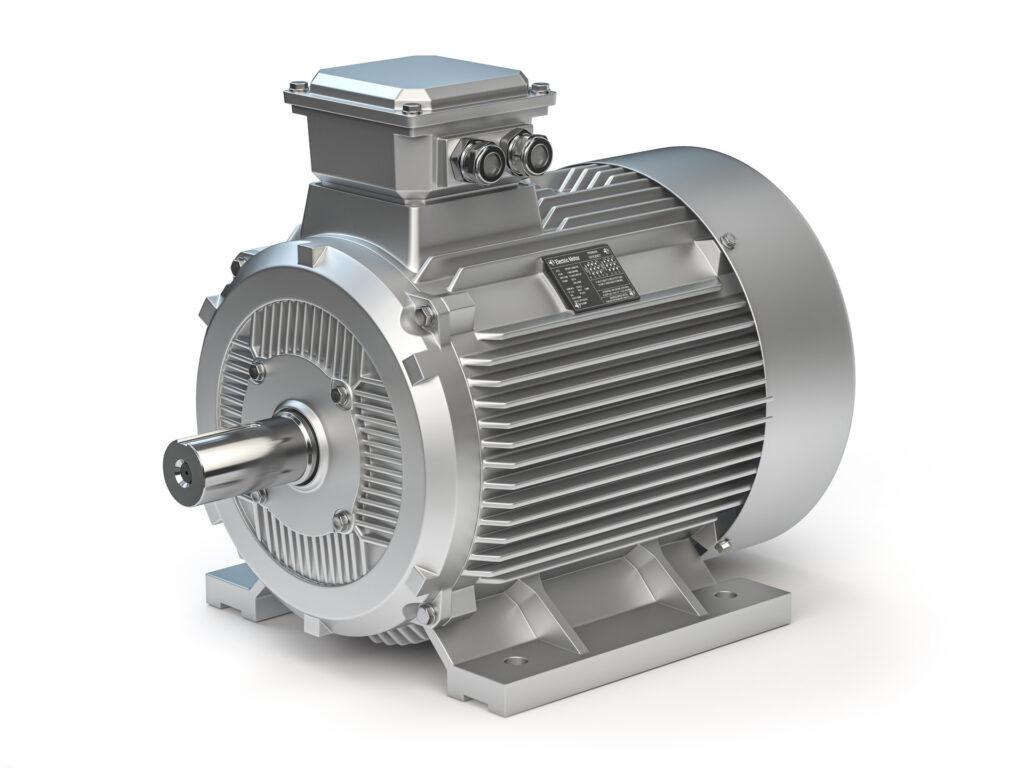
6.1 Industrial Motors
Energy-efficient motor are extensively used in industrial motors, where energy savings, reliability, and compliance with regulatory standards are crucial. Industrial motors are widely used in applications such as manufacturing, HVAC systems, and heavy machinery, and they operate continuously under varying loads. Motors in these applications must adhere to efficiency standards like IE3 (Premium Efficiency) and IE4 (Super Premium Efficiency), which demand low energy losses and high performance.
By using energy-efficient motor lamination made from materials like silicon steel, industrial motors can significantly reduce energy consumption. These cores help minimize losses from hysteresis and eddy currents, allowing the motors to maintain performance even in harsh operating conditions. Additionally, the improved thermal management properties of energy-efficient cores extend the lifespan of the motors, reducing downtime and maintenance costs for industries.
6.2 Electric Vehicles (EVs)
In electric vehicles (EVs), the role of energy-efficient motor cores is vital to enhancing range, reducing battery consumption, and ensuring optimal performance under various driving conditions. EVs rely on electric motors to convert electrical energy from the battery into mechanical energy that powers the vehicle. Energy-efficient motor cores reduce energy losses in this conversion process, allowing for more effective use of the battery, which directly contributes to increased driving range.
6.3 Renewable Energy Systems
High-efficiency motor cores play an important role in renewable energy systems such as wind turbines and solar power installations. In these applications, energy efficiency is paramount to maximize power generation and minimize losses during energy conversion. For example, wind turbines use electric motors with high-efficiency cores to convert mechanical energy from the wind into electrical energy. Similarly, solar power systems use motors with efficient cores to manage energy storage and distribution.
By incorporating high-efficiency motor cores, renewable energy systems can operate more effectively, delivering greater energy outputs while reducing waste. This contributes to both lower operational costs and a smaller environmental impact, helping to promote the adoption of renewable energy solutions worldwide.
8. Conclusion
8.1 Recap of Key Points
Energy-efficient motor cores are critical to optimizing the performance of electric motors across various applications, including industrial motors, electric vehicles, and renewable energy systems. These cores minimize energy losses, improve magnetic properties, and manage heat more effectively, thanks to advanced materials like silicon steel. Precision manufacturing techniques, such as Wire EDM and thin lamination stacking, further enhance their efficiency and reliability.
If you’re looking for products or support about high-efficiency electric motor cores, our team is ready to assist. Contact us today!
※Further Reading: Advanced Lamination Technologies: The Key to Enhancing Permanent Magnet Motor Performance