Explore five revolutionary trends in stator core manufacturing technology, focusing on automated winding technology and smart factory innovations, transforming the electric motor industry.
1. Global Growth in Stator Core Manufacturing Technology and Associated Challenges
1.1 The Push from Electric Vehicles and Renewable Energy in Stator Core Manufacturing Technology
As the world transitions towards cleaner energy and more sustainable transportation, electric vehicle (EV) and renewable energy markets are booming. These shifts are creating a demand for more efficient and lighter electric motors, especially those used in electric vehicles and wind turbines. In EVs, for example, the push for longer battery range and higher efficiency means that every component must be optimized for performance, weight, and cost. Stator cores are no exception.
Traditional stator core manufacturing methods, such as stamping and assembling laminated steel cores, have long been reliable for producing high-quality electric motors. However, as demand grows and technology evolves, manufacturers are discovering new ways to supplement these traditional methods with advanced techniques. These enhancements are designed not to replace stamping or lamination but to complement them, offering greater flexibility, customization, and efficiency in meeting new market demands. For more information on how stator core laminations are being applied specifically in electric vehicles, read more here.
1.2 The Need for Future Stator Core Manufacturing Technology
As competition intensifies and performance standards rise, manufacturers must innovate to remain competitive. Companies that find ways to lower production costs while improving precision and scalability will be better positioned for success. Future-facing manufacturing technologies—like automation and smart factory systems—are offering the flexibility needed to respond to this evolving landscape.
These technologies work hand in hand with traditional methods, enhancing manufacturing processes without undermining the reliability of stamping and lamination. For instance, automation can speed up production without sacrificing quality, while smart factory systems can ensure more precise monitoring and control over processes. Together, these advancements help manufacturers meet growing production volumes while offering increased flexibility in prototyping and testing new designs.
2. Application of Automated Winding Technology in Stator Core Production
2.1 Introduction to CNC Automated Winding Technology
One of the most critical processes in stator core production is the winding of copper coils, which create the magnetic fields necessary for motor operation. Traditionally, this task was labor-intensive and susceptible to human error, especially when high precision was required. But with the rise of CNC (Computer Numerical Control) automated winding technology, manufacturers now have a tool that offers incredible precision, efficiency, and repeatability in coil winding.
CNC winding machines control parameters such as wire tension, coil placement, and the number of turns per coil with remarkable accuracy. This ensures that each stator core meets the design’s exact specifications without the inconsistencies that sometimes result from manual winding. Moreover, CNC automation can adapt to different winding patterns and motor designs, providing much-needed flexibility for producing specialized motors.
CNC technology offers a solution for both small- and large-scale production, ensuring consistency in the quality of each unit. The ability to customize coil designs quickly while maintaining production speed makes this technology a key player in modern stator core manufacturing.
2.2 How Automated Winding Technology Improves Production Efficiency
Automation in coil winding does more than just improve precision; it also significantly boosts overall production efficiency. With manual winding, even skilled workers can only reach a certain level of speed and accuracy. In contrast, CNC automated systems can operate continuously with minimal oversight, dramatically increasing throughput.
This increase in production efficiency allows manufacturers to meet growing demand in industries like electric vehicles and renewable energy, where the need for efficient and scalable stator core production continues to rise. Automated systems also reduce the risk of defects, ensuring that each stator core meets the required specifications, minimizing the need for rework.
Automation not only reduces the reliance on manual labor but also provides opportunities to reduce lead times and improve delivery schedules. Manufacturers can handle higher production volumes without sacrificing quality, making automated winding a critical part of the stator core manufacturing process.
Moreover, automation reduces material wastage and operational downtime by detecting and correcting errors early in the process. This further drives down production costs and makes it easier for companies to scale their operations without compromising on quality.
3. Advances in Smart Inspection and Quality Control in Stator Core Manufacturing Technology
3.1 The Role of Advanced Inspection Technologies in Stator Core Manufacturing Technology
As the complexity of stator cores increases, maintaining high quality throughout the production process becomes even more crucial. In this regard, advanced inspection technologies have become essential. By integrating real-time monitoring systems that use sensors and data analytics, manufacturers can track critical production parameters, such as temperature, pressure, and alignment, to detect any deviations early.
Real-time monitoring can identify minor issues during production—like slight misalignments in lamination layers or inconsistencies in coil winding—and allow manufacturers to correct them before they lead to larger defects. This level of precision not only improves overall quality but also reduces waste and rework, cutting down on costs.
These smart systems go beyond merely identifying defects; they offer continuous improvement by collecting valuable data from each production run. This data can then be used to refine processes, improving the quality and efficiency of future production runs.
3.2 The Role of Machine Learning in Stator Core Manufacturing Technology Quality Control
Machine learning is becoming an increasingly important part of the quality control process in stator core manufacturing. By analyzing historical production data, machine learning algorithms can predict when defects are likely to occur or when equipment is likely to fail. This predictive capability allows manufacturers to implement preventive maintenance strategies, minimizing unexpected downtime and enhancing overall production efficiency.
Machine learning systems can detect subtle issues that human inspectors might overlook, such as patterns in coil winding errors or gradual wear in production equipment. These predictive models can then flag components for closer inspection or suggest real-time adjustments to production settings, ensuring that every stator core meets strict quality standards.
The combination of real-time monitoring and machine learning empowers manufacturers to maintain high levels of quality while optimizing production processes. These advanced technologies are transforming quality control from a reactive to a proactive discipline, enabling companies to meet increasingly stringent industry standards.
4. Future Trends in Stator Core Manufacturing Technology: Smart Factory Innovations
4.1 Smart Factory Innovations and Full Automation in Stator Core Manufacturing
The next major step in stator core manufacturing is the development of smart factories. In a smart factory, every aspect of production is connected through the Internet of Things (IoT), enabling machines to communicate with each other and with centralized control systems. This connectivity ensures that production lines are always optimized for efficiency, reducing waste and improving output quality.
Smart factories leverage real-time data to make adjustments in production workflows. For example, if one machine experiences a delay, others can adjust their operations to maintain overall production efficiency. This interconnectedness ensures that all resources—whether time, energy, or materials—are used as efficiently as possible, driving down costs and improving sustainability.
The adoption of smart factory principles in stator core manufacturing offers numerous advantages. It enhances production flexibility, allowing manufacturers to quickly adapt to new designs or customer requirements. It also enables better control over every step of the manufacturing process, from material procurement to final testing and inspection. For more insights into how smart factories are shaping modern industries, particularly through key players like Siemens and Schneider Electric, you can refer to this Smart Factory Market: Trends and Insights report.
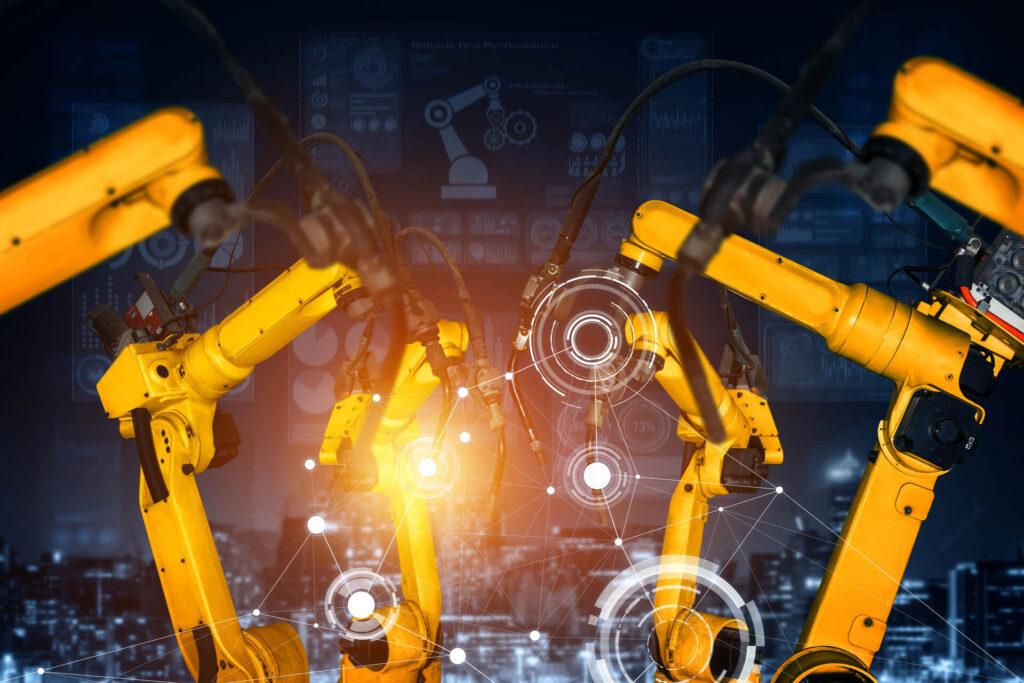
4.2 Environmental Sustainability and Smart Factory Innovations in Stator Core Manufacturing Technology
As industries worldwide focus on reducing their environmental impact, the stator core manufacturing industry is also embracing sustainability initiatives. The integration of eco-friendly manufacturing techniques is becoming a critical focus for companies looking to reduce material waste and energy consumption.
Manufacturers are exploring new ways to recycle and reuse materials in the production process, such as closed-loop systems that reduce waste by reusing excess materials. Additionally, energy-efficient machinery and optimized production processes are helping manufacturers reduce their overall carbon footprint.
Eco-friendly manufacturing techniques not only benefit the environment but also offer significant cost-saving opportunities. By minimizing waste and improving energy efficiency, companies can reduce their operational costs while complying with increasingly stringent environmental regulations.
In the future, sustainability will continue to be a driving force in manufacturing, particularly as industries like electric vehicles and renewable energy grow. Companies that embrace sustainable practices will be better positioned to meet customer expectations and regulatory demands while maintaining their competitiveness in the market.
5. Conclusion
5.1 The Long-Term Impact of Automated Winding Technology and Smart Factory Innovations
Innovative technologies such as automated winding, smart inspection systems, and IoT-powered smart factories are revolutionizing stator core manufacturing. These advancements enable manufacturers to meet the growing demand for high-performance electric motors while maintaining efficiency and product quality.
These innovations are not meant to replace traditional methods like stamping and lamination but instead complement them by offering more flexibility and precision in production. By combining the best of traditional and advanced technologies, manufacturers can improve scalability, customization, and overall performance in their production lines.
5.2 Shaping a More Efficient and Sustainable Future in Stator Core Manufacturing Technology
The future of stator core manufacturing lies in the seamless integration of advanced technologies and sustainable practices. By adopting smart manufacturing techniques and eco-friendly processes, companies can meet the increasing demand for electric motors while reducing their environmental impact.
As sustainability becomes a key driver of innovation, manufacturers will need to balance performance, cost, and environmental responsibility. Those who embrace these emerging trends will be well-positioned to lead the stator core manufacturing industry into a more efficient, flexible, and sustainable future.