1. Introduction to DC Motor Core and Its Importance
1.1 Understanding the Role of a DC Motor Core
At the heart of every DC motor is the motor core, a critical assembly that greatly influences the motor’s performance, efficiency, and reliability. The motor core typically includes two main parts: the stator core and the rotor. Specifically, the stator core serves as a stationary component that provides a magnetic path, enabling efficient magnetic flux distribution. Made from laminated sheets of electrical steel, stator cores are designed to minimize energy losses, particularly those resulting from eddy currents and hysteresis.
In practical applications, whether in automotive systems, industrial machinery, or robotics, the stator core ensures that magnetic fields generated by electrical currents translate effectively into mechanical torque. For instance, in electric vehicles, a high-quality stator core helps deliver consistent and efficient propulsion, directly impacting vehicle range and battery efficiency.
1.2 Why the Quality of the Stator Core Matters
The quality of a stator core is crucial because imperfections in lamination stacking, inferior material choices, or inconsistent manufacturing processes can significantly degrade motor performance. Poor stator core construction can cause excessive heat generation, increased electromagnetic interference, and accelerated wear, all of which shorten motor lifespan and raise maintenance costs.
For example, industrial equipment manufacturers frequently encounter reliability issues stemming from substandard stator cores, such as motor overheating and premature bearing failure. These failures lead to costly downtime, negatively impacting operational productivity. Conversely, manufacturers that adopt precision-engineered stator cores typically experience reduced energy losses, lower operating temperatures, and enhanced motor durability.
In summary, the selection of a stator core should be approached with caution and informed diligence. Understanding how stator core quality affects DC motor operation and reliability allows engineers and purchasing managers to make better-informed decisions, ultimately optimizing equipment performance, reducing unexpected downtime, and enhancing long-term cost-effectiveness.
2. Surprising Impact #1: Enhanced Thermal Performance
2.1 How Quality Stator Cores Improve Heat Management
Thermal management is a critical yet frequently overlooked factor in determining DC motor performance and reliability. At the center of effective heat dissipation within DC motors lies the quality and precision of the stator core lamination. High-quality stator cores are typically manufactured using thin sheets of electrical steel, meticulously laminated to reduce unwanted energy losses. The careful stacking of these laminations creates a uniform structure, significantly decreasing heat generation caused by eddy currents and hysteresis.
When stator cores lack uniformity or contain imperfections—such as gaps, misalignment, or inconsistent insulation coatings—these issues contribute directly to increased heat buildup. Poor thermal management can degrade motor performance, shorten component lifespan, and raise maintenance frequency. On the contrary, stator cores made with precision techniques offer efficient heat conduction and reduce localized hot spots, ensuring stable motor operation under diverse load conditions.
2.2 Benefits of Improved Heat Dissipation in DC Motors
Improved heat dissipation in DC motors due to enhanced stator core quality brings substantial operational benefits. For example, in industrial conveyor systems, motors often run continuously under heavy loads, generating significant heat. A precisely manufactured stator core can significantly reduce operating temperatures, prolonging the motor’s lifespan and decreasing the likelihood of unexpected equipment downtime.
Additionally, electric vehicle manufacturers emphasize optimized thermal management as a critical performance factor. High-quality stator cores help maintain optimal temperatures even during intense acceleration and regenerative braking scenarios. This directly translates into higher efficiency, improved battery usage, and overall reliability.
Therefore, by investing in superior stator cores, engineers and equipment manufacturers can significantly enhance motor longevity and performance consistency. Recognizing and addressing thermal management proactively not only safeguards DC motors against premature failure but also contributes to greater efficiency and sustainability in industrial and commercial applications.
3. Surprising Impact #2: Significant Reduction of Eddy Current Losses
3.1 Eddy Current Formation and Its Consequences
Eddy currents are loops of electrical current induced within conductive materials by changing magnetic fields. Within the context of DC motors, especially in the stator core, these currents represent unwanted energy loss that manifests primarily as heat. Eddy currents arise when laminated cores are insufficiently insulated or when the thickness and arrangement of laminations are suboptimal. If unchecked, these currents can significantly degrade motor efficiency, elevate operational temperatures, and accelerate component aging.
Practically speaking, motors operating under frequent acceleration or variable loads—such as automated production lines or electric vehicles—are particularly susceptible to performance issues resulting from eddy currents. For example, industrial manufacturers often observe decreased efficiency and increased operating costs due to inadequate stator lamination practices, highlighting the importance of precision in the manufacturing and assembly processes.
3.2 How Stator Core Quality Mitigates Eddy Current Losses
The reduction of eddy current losses largely depends on the quality and precision of stator core laminations. High-quality cores use thin laminations of electrical steel with insulating coatings to effectively isolate each layer. These precise laminations disrupt current paths, minimizing energy losses caused by circulating currents. Moreover, employing thinner steel laminations directly reduces the eddy current path length, thereby cutting down total losses significantly.
Real-world examples demonstrate these improvements clearly. Consider high-performance motors used in CNC machining equipment, where precision and efficiency are paramount. Here, manufacturers using stator cores with precision-engineered laminations typically experience enhanced energy efficiency, lower heat generation, and improved overall reliability. Such motors not only perform more consistently but also benefit from an extended service life, ultimately delivering cost savings over the motor’s operational lifetime.
In short, careful attention to stator core lamination design and assembly techniques significantly reduces eddy current losses, leading to improved motor efficiency, enhanced reliability, and lower long-term operational costs.
4. Surprising Impact #3: Improved Mechanical Strength and Durability
4.1 Mechanical Integrity and Stator Core Construction
Mechanical strength is a vital yet frequently undervalued aspect of electric motor reliability. The mechanical integrity of the stator core, influenced largely by the precision and quality of its lamination stacking, is central to long-term motor performance. Stator cores crafted from carefully selected electrical steel sheets, accurately aligned and securely stacked, offer improved resistance to mechanical stress, vibrations, and operational wear. Conversely, cores constructed from inferior materials or assembled with uneven stacking techniques often experience loosened laminations or deformation under operational loads, negatively affecting the motor’s reliability.
From a technical perspective, the mechanical robustness of a stator core is significantly enhanced by consistent lamination thickness and precision alignment during assembly. Proper stacking not only stabilizes the magnetic flux path but also reduces the likelihood of vibration-induced damage or mechanical fatigue, common in motors subjected to fluctuating loads or harsh operating environments.
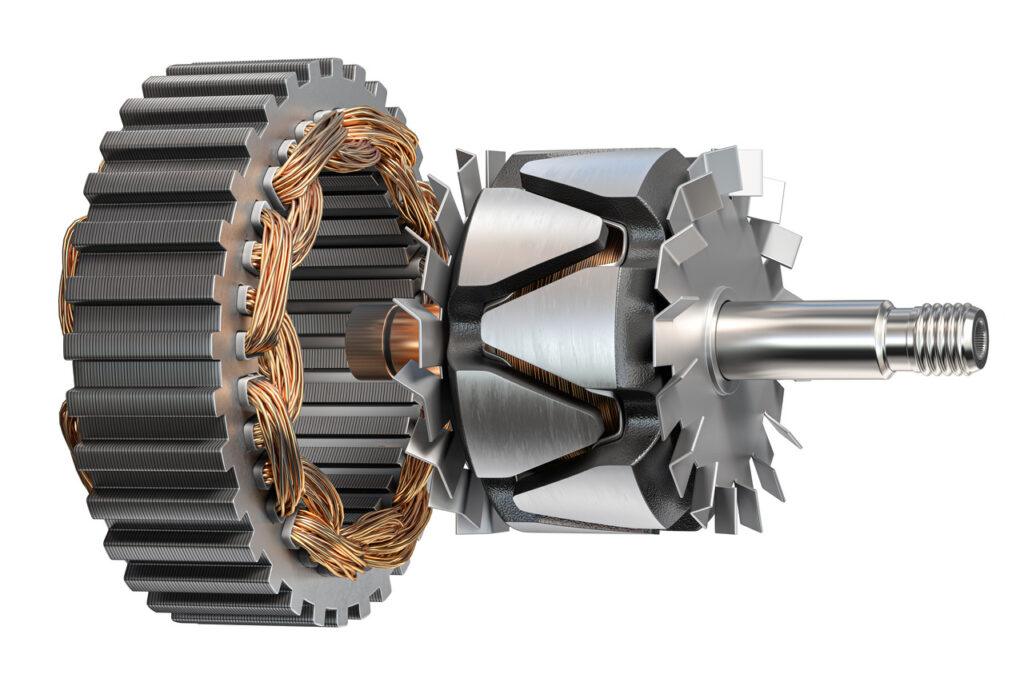
4.2 Long-Term Advantages of Mechanical Durability
The practical advantages of enhanced mechanical durability in stator cores extend far beyond immediate performance improvements. In industrial settings, for instance, motors operating machinery such as pumps, compressors, or automated assembly lines face continuous mechanical stress. Stator cores with superior mechanical strength and accurately stacked laminations offer greater resilience, resulting in fewer maintenance interventions and reduced downtime.
A real-life example highlighting this advantage can be observed in heavy-duty robotic systems in manufacturing environments. High-quality stator cores ensure motors withstand repetitive mechanical stress and vibration without deformation or structural weakening. Motors equipped with precision-manufactured cores exhibit longer service intervals, improved operational uptime, and lower overall lifecycle costs.
In conclusion, prioritizing mechanical strength and durability when selecting or designing stator cores delivers significant long-term benefits, including reduced maintenance frequency, prolonged motor lifespan, and improved reliability across various challenging applications.
5. Surprising Impact #4: Optimized Magnetic Flux Leading to Consistent Torque Output
5.1 Relationship Between Stator Core Quality and Magnetic Flux
Optimizing magnetic flux is essential to achieving stable and consistent torque output in electric motors. The quality of the stator core directly influences how efficiently magnetic flux travels within the motor. Ideally, high-quality cores are carefully laminated using precision-cut electrical steel sheets that reduce magnetic reluctance—the resistance to magnetic flux. When laminations are properly aligned and uniformly stacked, magnetic flux distribution becomes stable and predictable, enhancing overall motor performance.
Conversely, imperfections or inconsistencies in the stator core—such as uneven laminations, air gaps, or poorly insulated layers—can disrupt magnetic flux paths. This disruption results in irregular flux patterns, reduced torque consistency, and decreased operational efficiency. Consequently, motors with compromised flux distribution often struggle with unpredictable torque variations, leading to inefficiency or operational instability under varying loads.
5.2 Consistent Torque Output and Motor Reliability
The consistency of torque output has direct implications for motor reliability, particularly in applications requiring precise control and consistent mechanical power. For instance, electric vehicles depend heavily on stable torque delivery for smooth acceleration, optimal performance, and predictable range management. A precisely manufactured stator core contributes significantly to these performance requirements by ensuring stable magnetic flux paths, resulting in predictable and uniform torque output.
Similarly, industrial automation equipment, such as robotic arms or precision machinery, demands reliable torque consistency to execute accurate movements and maintain production efficiency. High-quality stator cores, through optimal flux management, allow motors to achieve the necessary control and repeatability required in these environments.
In practical scenarios, choosing a stator core designed for optimized magnetic flux can yield measurable operational improvements. Users typically experience lower variability in performance, increased reliability in high-precision applications, and reduced downtime from maintenance or recalibration, ultimately translating into substantial long-term cost savings and improved operational stability.
6. Conclusion: Key Insights on the Importance of Stator Core Quality
6.1 Summary of the 4 Surprising Impacts
Throughout this exploration, we have underscored several often-overlooked yet significant ways in which the quality of the stator core affects DC motor reliability. Firstly, enhanced thermal performance through careful lamination practices ensures efficient heat dissipation, minimizing overheating issues that commonly plague motors in demanding applications. Secondly, meticulous core lamination substantially reduces eddy current losses, directly translating into improved efficiency and lower energy consumption.
Additionally, we’ve recognized that precision in core assembly leads to improved mechanical strength and durability. Motors incorporating robust stator cores experience fewer structural issues, better withstand operational stresses, and thus exhibit prolonged lifespans. Lastly, optimized magnetic flux pathways resulting from accurately stacked cores provide consistent torque output—critical for applications requiring precise performance and stable operation, such as industrial automation or electric vehicles.
6.2 Encouraging Informed Decisions on Stator Core Selection
When choosing or designing a motor system, acknowledging the importance of core quality helps stakeholders make informed decisions. Rather than viewing the core merely as a basic structural component, engineers and procurement managers can significantly improve overall equipment performance by paying closer attention to lamination quality and assembly precision.
Real-world experience consistently validates this approach. For example, automotive manufacturers increasingly prioritize lamination precision in their motors, witnessing improved reliability, increased performance efficiency, and reduced operational costs. Similarly, factories employing high-quality motor cores report reduced downtime and lower maintenance expenditures over time.
In conclusion, while the motor core—particularly the stator component—might seem like a small part of a larger system, investing in its quality is a strategically wise choice. Doing so leads not only to immediate performance enhancements but also substantial long-term reliability and cost benefits. Adopting this mindful, quality-focused approach provides meaningful advantages across a wide variety of motor-driven applications.
Further Reading: