1. Introduction
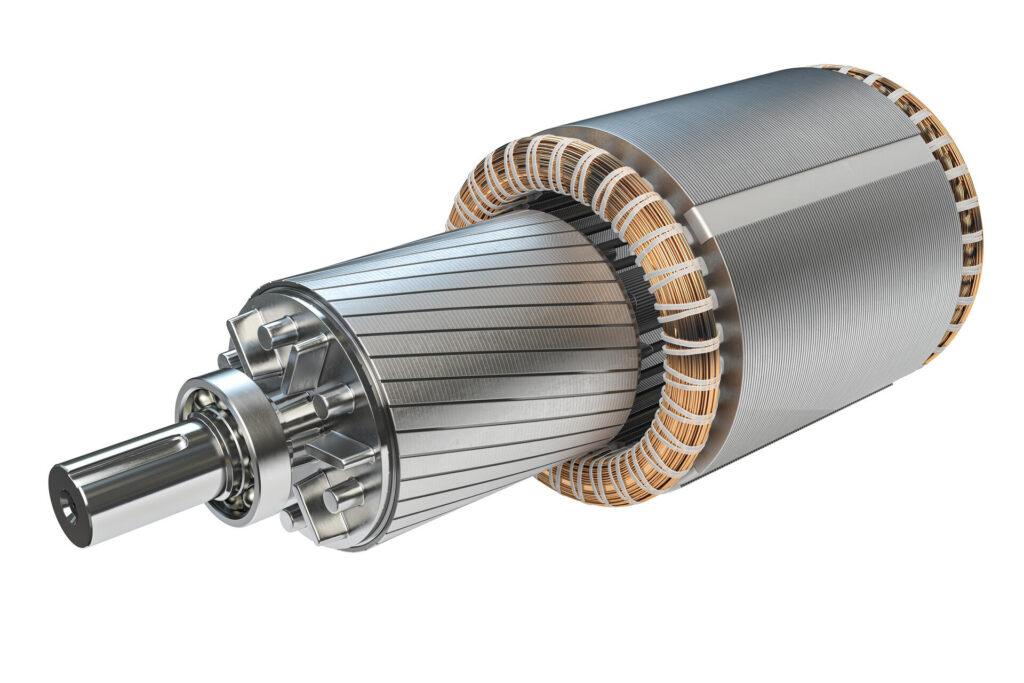
1.1 Importance of Regular Maintenance
High efficiency motor cores play a critical role in modern industry and daily life, with their efficiency directly impacting equipment performance and energy consumption. Regular maintenance of key motor components, such as brushes and commutators, helps ensure optimal operation and prevents efficiency loss. Neglecting these components can result in poor electrical conductivity, overheating, and even motor failure, leading to increased repair costs and downtime.
1.2 Overview of Key Components
Brushes and commutators are core components of brushed DC motors. Brushes, typically made of carbon or graphite, are responsible for transferring current from an external power source to the rotating commutator. The commutator, composed of multiple copper segments mounted on the rotor shaft, facilitates the switching of current direction to ensure continuous rotor rotation.
Additionally, Motor Core Laminations are crucial in supporting motor efficiency by reducing eddy current losses and improving overall performance.
Understanding the functions and interactions of these components helps identify potential issues and enables appropriate maintenance measures to ensure long-term stability and efficiency of the motor.
2. Detailed Maintenance Steps
2.1 Inspecting Motor Brushes
2.1.1 Identifying Signs of Wear
Wear on motor brushes is a major cause of efficiency loss and failure. When inspecting motor brushes, look for the following key indicators:
- Reduction in Size: A noticeable decrease in brush height can result in insufficient contact area, leading to poor conductivity.
- Uneven Wear: Some parts of the brush wearing faster than others may indicate an uneven commutator surface or inconsistent spring pressure.
It is recommended to use calipers or measuring tools to check the brush dimensions and ensure they meet the manufacturer’s standards. By carefully observing the brush surface, you can predict whether further maintenance or replacement will soon be necessary.
2.1.2 Inspection Frequency
The frequency of inspection depends on the motor’s application. For example:
- Industrial Motors: Inspect approximately every 1,000 hours of operation.
- Household or Light-Load Motors: Inspect every six months.
Regular inspections help identify issues early, preventing costly repairs and efficiency losses.
2.2 Cleaning the Commutator
2.2.1 Importance of Cleaning
The commutator is the critical contact point between the brushes and the electrical current. Accumulated dirt and carbon dust can obstruct current flow, increase friction, and cause higher temperatures, leading to reduced motor efficiency.
2.2.2 Safe Cleaning Methods
When cleaning the commutator, use non-abrasive brushes or specialized solvents to avoid scratching the copper segments. Follow these safe cleaning steps:
- Turn off the power and remove the motor casing.
- Use a clean brush or compressed air to remove surface dust.
- Gently wipe the commutator with a non-corrosive cleaner and finish by drying with a clean cloth.
Avoid using overly sharp tools during the process to prevent damage to the commutator surface.
2.3 Replacing Worn Brushes
2.3.1 When to Replace
Replace brushes immediately when you notice:
- Height near the minimum standard: Brushes can no longer provide stable contact pressure.
- Rough or damaged contact surfaces: These can lead to increased sparking and unstable current flow.
2.3.2 Choosing the Right Replacement Brushes
When selecting replacement brushes, consider compatibility with the motor model and the material properties of the brushes, such as carbon or graphite. Using mismatched brushes may lead to more severe performance issues or even damage other components.
By properly performing these steps, you can significantly extend the motor’s lifespan and maintain high efficiency.
3. Benefits of Regular Maintenance
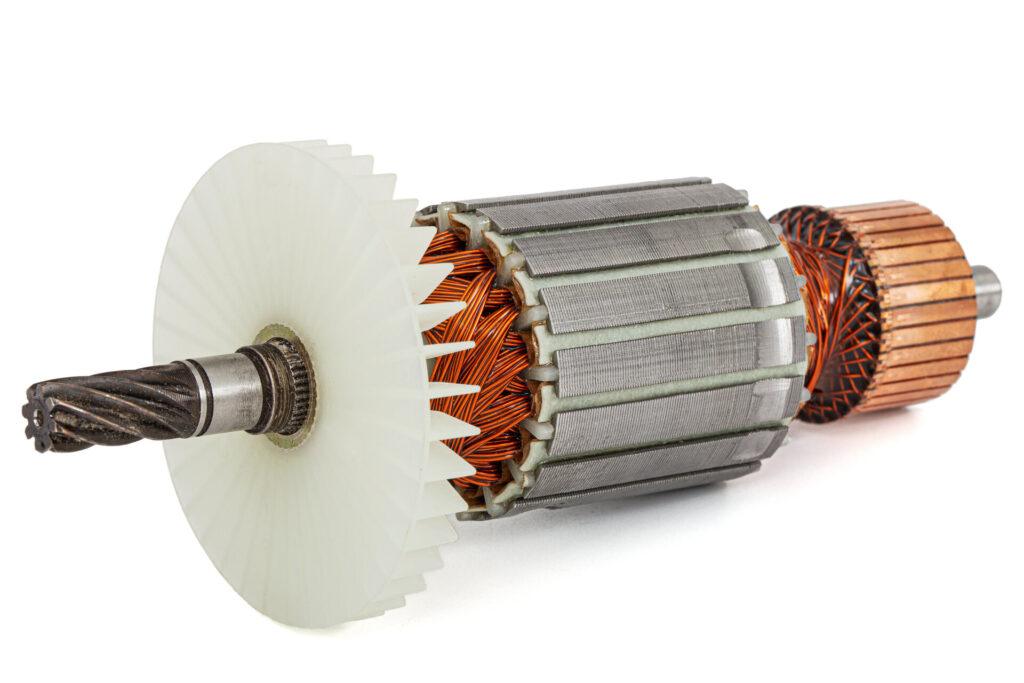
3.1 Improved Efficiency
Regular maintenance of motor brushes and commutators can significantly enhance the operational efficiency of electric motors. Cleaning the commutator surface and inspecting the condition of the brushes reduces losses during current conduction, enabling the motor to operate more efficiently. Research indicates that motor efficiency can improve by 15% to 20% with regular maintenance, which is especially important for industrial equipment that operates continuously.
Maintenance also reduces issues such as electrical instability, excessive sparking, or output fluctuations, thereby maintaining motor performance and lowering energy losses during operation.
3.2 Extended Motor Lifespan
The lifespan of an electric motor is closely tied to the health of its critical components. Wear on the commutator and aging brushes are common causes of motor failure. Regular maintenance can delay these issues. For instance, cleaning the commutator minimizes surface damage, and timely replacement of brushes prevents poor conductivity, which helps protect other essential components.
Data shows that motors with regular maintenance can have their operational lifespan extended by over 30%. This not only decreases the frequency of equipment replacement but also reduces downtime and repair costs caused by failures.
3.3 Reduced Energy Consumption
Regular maintenance also plays a key role in reducing energy consumption. When the commutator is kept clean and brush pressure is optimal, the motor operates with lower electrical resistance, thereby reducing power demand.
For example, a well-maintained industrial motor can save 5% to 10% in annual electricity costs, which is significant for equipment used over long periods. Additionally, reducing energy consumption not only saves costs but also lowers carbon emissions, contributing to more sustainable production processes.
In summary, the high efficiency, durability, and energy-saving benefits provided by regular maintenance are critical advantages that cannot be overlooked.
4. Conclusion
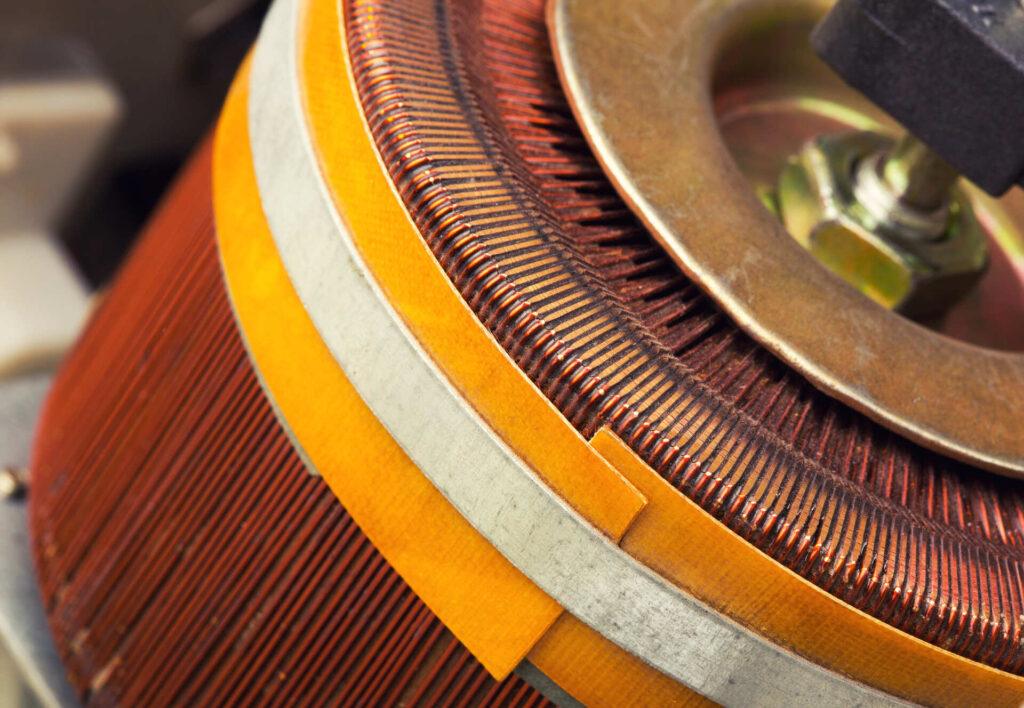
4.1 Key Takeaways
Regular maintenance of motor brushes and commutators not only helps prevent efficiency loss but also extends the lifespan of the motor and reduces energy consumption. This article introduced three maintenance steps—inspecting brushes, cleaning the commutator, and replacing worn brushes—that are foundational to maintaining motor performance and improving efficiency.
These steps help users minimize friction losses, reduce heat buildup, and ensure stable electrical conductivity. Specifically, regular inspections and cleaning can decrease efficiency losses by 15% to 20%, while timely brush replacement can prevent major failures caused by poor conductivity. For equipment that operates for extended periods, these maintenance practices are crucial for significantly enhancing overall operational efficiency.
4.2 Call to Action
To ensure long-term, efficient operation of electric motors, users are encouraged to take immediate action by incorporating regular maintenance of brushes and commutators into their routine schedules. Whether for industrial applications or household devices, the following measures can help achieve optimal results:
- Develop a maintenance schedule for inspections and cleaning based on motor usage, whether monthly, quarterly, or annually.
- Use the appropriate tools and methods during maintenance to avoid damaging components due to improper handling.
- If maintenance cannot be performed independently, seek assistance from professional technicians to ensure all steps are carried out to standard.
Finally, users are reminded that good maintenance habits not only save energy and operating costs but also reduce environmental impact, contributing to sustainable development goals. Regular maintenance is not only key to extending equipment lifespan but also essential for improving efficiency and mitigating operational risks. Take action now to keep your equipment in optimal condition!
※Further Reading: What is a High Efficiency Electric Motor Core? In 8 Key Points
External Links: https://www.researchgate.net/publication/386042390_Multi-Criteria_Analysis_of_Electric_Vehicle_Motor_Technologies_A_Review