Discover the future of motor core technology and its impact on electric motors and generators. Explore advancements in materials like soft magnetic composites, innovative manufacturing techniques, and integration with emerging technologies. Stay ahead with insights on how these trends enhance efficiency, performance, and sustainability in the evolving landscape of motor cores.
Introduction
Overview of Motor Core Technology
Importance in Electric Motors and Generators
The motor core serves as the heart of electric motors and generators, fundamentally influencing their efficiency, performance, and reliability. Composed typically of laminated magnetic materials like silicon steel, the motor core facilitates the magnetic flux essential for converting electrical energy into mechanical motion and vice versa. Its design and material composition are crucial, affecting everything from torque generation to thermal management within these machines.
Current Challenges and Limitations
Despite significant advancements, current motor core technologies face challenges that limit their performance. Energy losses due to hysteresis and eddy currents within the core material lead to decreased efficiency and increased heat generation. Traditional materials may not sufficiently support the miniaturization and higher power densities required in modern applications, such as electric vehicles (EVs) and renewable energy systems. Moreover, manufacturing processes often grapple with precision and consistency issues, resulting in performance variations and reduced longevity.
Innovative Manufacturing Techniques
Advanced Stamping and Lamination Processes
Precision Improvements
Innovations in manufacturing techniques, particularly advanced stamping and lamination processes, are enhancing motor core production. High-speed stamping technologies employing progressive dies and fine blanking methods produce intricate and uniform laminations with tight tolerances. This precision ensures consistent magnetic flux within the motor core, reducing losses due to irregularities and boosting overall efficiency. The use of laser cutting and computer numerical control (CNC) machining further refines manufacturing, enabling complex geometries previously unattainable.
Automation and Quality Control
Automation plays a crucial role in modern motor core manufacturing, improving efficiency and quality control. Automated stacking systems assemble laminations with precise alignment, minimizing human error. Real-time monitoring through sensors and imaging technologies allows immediate detection of defects, reducing waste and enhancing productivity. The integration of Industry 4.0 principles enables machines to communicate and adjust autonomously, optimizing operations without manual intervention.
Design Optimization Through Computational Methods
Computational Modeling and Simulation
Finite Element Analysis (FEA)
Finite Element Analysis (FEA) is pivotal in optimizing motor core designs. By breaking down complex geometries into smaller finite elements, FEA allows engineers to conduct detailed electromagnetic and thermal analyses. This method helps identify and mitigate issues like flux leakage and hotspots, which are critical for improving efficiency and extending motor lifespan. Virtual prototyping through FEA accelerates the design process, reducing the need for multiple physical prototypes.
Magnetic Field Optimization
Advanced simulation software enables engineers to model and adjust magnetic properties within the motor core. By fine-tuning factors such as air gaps and winding configurations, designers can minimize losses due to hysteresis and eddy currents. Visualizing magnetic flux paths helps achieve uniform flux distribution, crucial for enhancing torque and reducing noise and vibration in electric motors.
Artificial Intelligence and Machine Learning
Predictive Design Adjustments
Artificial Intelligence (AI) and Machine Learning (ML) are transforming motor core design by introducing predictive analytics. ML models trained on extensive datasets can predict how changes in materials or geometries will impact efficiency and reliability. This capability allows rapid iteration and optimization, significantly reducing development time and costs. AI-driven tools suggest design adjustments that enhance performance metrics like power density and thermal stability.
Enhancing Performance and Longevity
AI and ML also play a vital role in enhancing operational performance and longevity. Predictive maintenance systems utilize AI algorithms to analyze real-time data from sensors within the motor core. These systems forecast potential failures by detecting anomalies, allowing for proactive maintenance scheduling. Implementing AI in motor monitoring leads to reduced downtime and maintenance costs, optimizing performance over time.
Integration with Emerging Technologies
Internet of Things (IoT) and Smart Grids
Smart Motor Cores for Enhanced Connectivity
The convergence of motor core technology with IoT and smart grids is revolutionizing electric motors and generators. Smart motor cores embedded with sensors enable real-time data exchange with control systems. This connectivity allows precise monitoring of operational parameters like temperature and vibration. Enhanced connectivity facilitates improved operational efficiency and predictive maintenance strategies, optimizing energy consumption and reducing downtime.
Real-time Monitoring and Maintenance
Real-time monitoring, enabled by IoT integration, significantly improves maintenance practices. Sensors within the motor core collect continuous data, analyzed using advanced algorithms to detect wear or anomalies. Predictive maintenance powered by real-time analytics reduces maintenance costs and eliminates unexpected breakdowns. This proactive approach extends motor lifespan and enhances safety and reliability across various applications.
Electrification of Transportation
Motor Cores in Electric Vehicles (EVs)
The electrification of transportation accelerates the demand for advanced motor core technologies tailored for EVs. Motor cores in EVs must deliver high efficiency, compact size, and lightweight characteristics to maximize performance and range. Advancements in materials and designs, such as using SMCs and optimized lamination techniques, contribute to higher power densities and reduced losses, essential for automotive applications.
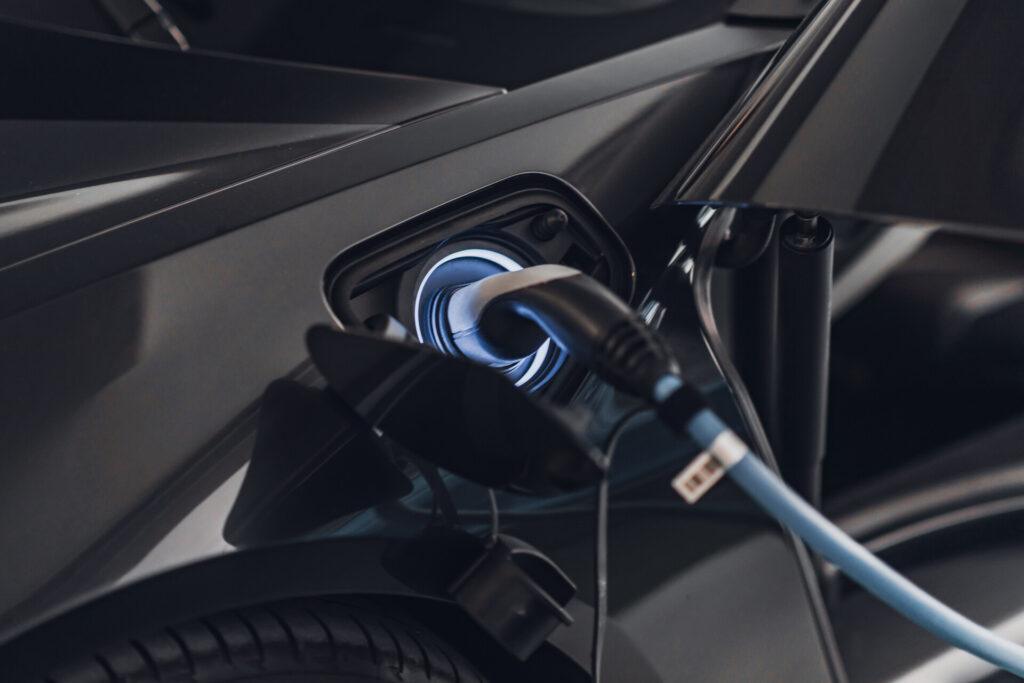
High-efficiency Designs for Extended Range
High-efficiency motor core designs are pivotal in extending EV driving ranges—a key factor in consumer adoption. Minimizing energy losses through advanced materials and computational optimization allows manufacturers to produce motors that use less energy for the same output. Improvements in motor efficiency not only increase range but also reduce battery size requirements, lowering vehicle costs and enhancing sustainability.
Energy Efficiency and Environmental Impact
Compliance with Global Energy Standards
Regulatory Drivers for Innovation
Global efforts to reduce carbon emissions drive the implementation of stringent energy standards, propelling innovation in motor core technology. Regulatory bodies like the International Electrotechnical Commission (IEC) set efficiency requirements that electric motors and generators must meet. Enhancing motor efficiency significantly decreases global electricity consumption, emphasizing the urgency for manufacturers to innovate. These regulations compel companies to explore advanced materials and design techniques to create motor cores that comply with or exceed energy efficiency standards.
Impact on Motor Core Development
Compliance with global energy standards profoundly impacts motor core development. Manufacturers invest in research to discover materials with superior magnetic properties, reducing core losses. Design optimization enhances efficiency, contributing to lower energy consumption and operational costs. Compliance is not just about meeting regulations but also about gaining a competitive edge by offering high-efficiency products appealing to environmentally conscious consumers.
Sustainable Materials and Recycling
Eco-friendly Production Methods
Sustainability in manufacturing is essential, and motor core production is no exception. Eco-friendly methods focus on reducing environmental impact by minimizing waste, lowering emissions, and conserving energy. Incorporating sustainable practices, such as using water-based insulation coatings and energy-efficient machinery, significantly reduces a factory’s carbon footprint. Sourcing raw materials responsibly and opting for recycled or renewable materials enhance sustainability, contributing to environmental conservation and cost savings.
End-of-life Management of Motor Cores
Effective end-of-life management for motor cores is crucial for environmental sustainability. Proper recycling and disposal prevent hazardous materials from harming the environment. Guidelines like the European Commission’s Waste Electrical and Electronic Equipment (WEEE) Directive encourage manufacturers to design motor cores with disassembly and recyclability in mind. This approach supports a circular economy, where materials are reused, reducing the need for new raw materials and minimizing environmental impact.
Future Outlook and Industry Impact
Predicted Advancements in Motor Core Technology
Long-term Vision for the Industry
Long-term, the industry envisions motor cores integrating smart materials and AI to create self-optimizing motors. Future motor cores may incorporate embedded sensors and IoT connectivity to autonomously optimize performance and energy consumption. Advances in nanotechnology could lead to new magnetic materials with unprecedented properties, further reducing losses and enhancing efficiency. Sustainability will continue to drive innovation, focusing on recyclable materials and circular economy principles.
Market Growth and Opportunities
Influence on Electric Motors and Generators Market
Advancements in motor core technology are expected to significantly influence the electric motors and generators market. Enhanced performance and efficiency will open new applications and drive demand across industries like renewable energy, EVs, and industrial automation. As energy efficiency becomes paramount, motors with advanced cores will be preferred for both new installations and retrofits. The market is projected to witness substantial growth due to these technological advancements.
Competitive Advantages for Early Adopters
Companies adopting advanced motor core technologies early stand to gain significant competitive advantages. Early adopters can differentiate themselves by offering products with superior efficiency, reliability, and sustainability. This differentiation can lead to increased market share, customer loyalty, and the ability to command premium pricing. Early adoption also allows companies to align proactively with regulatory trends, avoiding compliance issues and positioning themselves as industry leaders.
Conclusion
Summary of Key Trends
The future of motor core technology is bright, with advancements in materials, manufacturing, design optimization, and integration with emerging technologies driving the industry forward. Innovations like SMCs and amorphous alloys are enhancing efficiency and performance, while advanced manufacturing techniques improve precision and reduce costs. Computational methods and AI are optimizing designs and operations, and integration with IoT is making motors smarter and more adaptable. Emphasis on energy efficiency and sustainability is shaping development, aligning with global efforts to reduce environmental impact.