1. Introduction
1.1 Importance of Lamination in Permanent Magnet Motors
a. Brief Overview
Permanent magnet motors are crucial in modern technology, powering everything from household appliances to advanced industrial equipment. These motors rely on magnetic fields generated by permanent magnets, and their efficiency is significantly influenced by the core components known as laminations. Laminations are thin layers of steel or magnetic alloys stacked together, forming the motor’s core. They play a vital role in minimizing energy losses and enhancing the motor’s performance by reducing eddy current losses and improving magnetic flux.
b. Purpose of the Article
This article aims to elucidate the significance of advanced lamination technologies in the production of permanent magnet motors. By delving into various lamination techniques, the article will highlight how these innovations contribute to higher efficiency and reliability in motor performance. Understanding these advanced technologies is crucial for manufacturers seeking to optimize their motor designs and improve overall product quality.
2. Types of Advanced Lamination Technologies
2.1 Progressive Stamping
a. Definition and Process
Progressive stamping is an advanced manufacturing technique used to produce motor laminations efficiently. This process involves feeding a strip of metal through a series of progressive dies. Each die performs a specific operation, such as cutting, bending, or punching, incrementally shaping the metal strip into the desired lamination form. The sequence of operations is meticulously planned, ensuring that each step builds on the previous one, resulting in a high-precision final product.
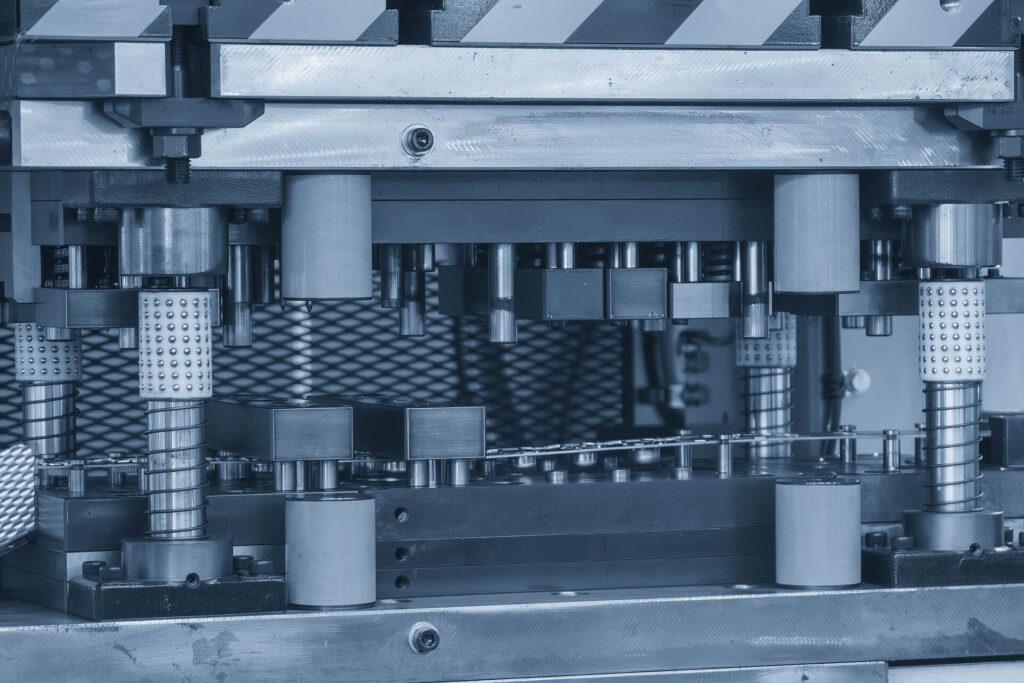
b. Benefits
Progressive stamping offers numerous advantages, including precision and consistency. The method ensures that each lamination produced is identical to the others, maintaining tight tolerances crucial for motor efficiency. Additionally, progressive stamping is cost-effective due to its high-speed production capabilities and minimal material waste, making it an ideal choice for large-scale manufacturing.
2.2 Compound Stamping
a. Definition and Process
Compound stamping is another sophisticated technique used in the creation of motor laminations. Unlike progressive stamping, compound stamping involves performing multiple operations, such as cutting and forming, in a single press stroke. This simultaneous action allows for the creation of complex and intricate designs in a single operation.
b. Benefits
The primary benefits of compound stamping include its ability to produce detailed and intricate designs with high efficiency. By consolidating multiple steps into one, compound stamping reduces production time and increases throughput. This method is particularly useful for manufacturing components that require high precision and complex geometries.
2.3 Rotary Notching
a. Definition and Process
Rotary notching is a high-speed manufacturing process used to cut notches into motor laminations. This method employs a rotating tool that makes precise notches as the metal strip moves through the machine. The process is continuous, allowing for rapid production of notched laminations.
b. Benefits
Rotary notching offers several benefits, including high-speed production and exceptional accuracy. The continuous nature of the process ensures a consistent output, making it suitable for large-volume production runs. Additionally, the precision of rotary notching helps maintain the integrity of the lamination design, which is essential for optimal motor performance.
3. Lamination Stacking Techniques
3.1 Interlocking
a. Definition and Process
Interlocking is a lamination stacking technique where individual laminations are designed with tabs and slots that fit together like a puzzle. During assembly, these interlocking features align precisely, creating a stable and secure stack without the need for additional fasteners or adhesives. This method ensures that each lamination is perfectly positioned, maintaining the overall integrity of the motor core.
b. Benefits
The primary benefits of interlocking include precise alignment and enhanced stability. The interlocking tabs ensure that each layer is consistently positioned, which is crucial for the motor’s magnetic properties. Additionally, this technique simplifies the assembly process and reduces the need for additional materials, making it a cost-effective solution for producing high-quality laminations.
3.2 Gluing and Self-Bonding
a. Definition and Process
Gluing involves applying adhesive between laminations to bond them together, while self-bonding utilizes a special coating that activates and bonds under heat and pressure. Both methods aim to create a unified stack that maintains its structural integrity throughout the motor’s operational life. The gluing process involves careful application to ensure even coverage, while self-bonding requires precise control of temperature and pressure to achieve optimal bonding.
b. Benefits
The benefits of gluing and self-bonding include enhanced structural integrity and reduced vibrations and noise. These methods ensure that the laminations stay securely in place, which is essential for maintaining the motor’s efficiency and performance. The reduction in vibrations and noise also contributes to the overall reliability and longevity of the motor.
3.3 Laser Welding
a. Definition and Process
Laser welding is a precision technique that uses a focused laser beam to join laminations. This process involves directing the laser at the joint area, melting the material to form a strong bond. The high precision of laser welding allows for clean and accurate welds, making it ideal for applications requiring tight tolerances.
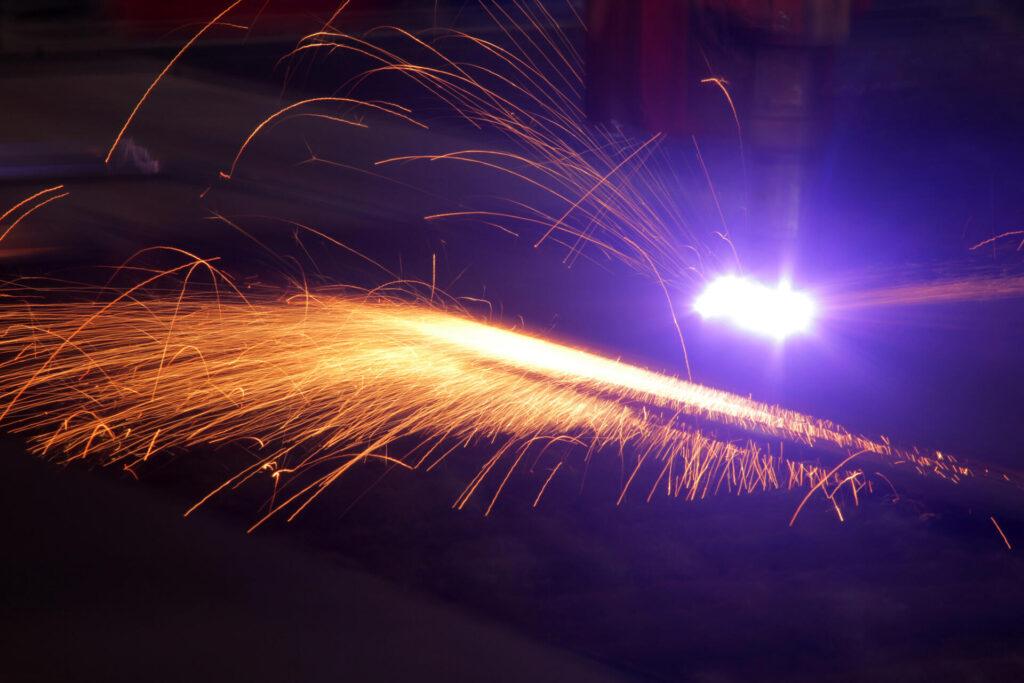
b. Benefits
Laser welding offers robust bonding and improved heat dissipation. The strength of the weld ensures that the laminations remain securely fastened, even under high stress. Additionally, the precise control over the welding process minimizes thermal distortion, which can improve the motor’s efficiency and performance by ensuring optimal alignment and contact between laminations.
3.4 TIG and MIG Welding
a. Definition and Process
TIG (Tungsten Inert Gas) and MIG (Metal Inert Gas) welding are both arc welding processes used to join laminations. TIG welding uses a non-consumable tungsten electrode to produce the weld, while MIG welding uses a consumable wire electrode. Both processes involve creating an electric arc between the electrode and the workpiece to melt and join the materials.
b. Benefits
The benefits of TIG and MIG welding include durable joints and versatility in applications. TIG welding is known for its high-quality welds and precision, making it suitable for intricate lamination designs. MIG welding, on the other hand, offers faster production rates and is more forgiving of minor surface contaminants, making it ideal for large-scale production.
3.5 Riveting and Cleating
a. Definition and Process
Riveting involves inserting metal pins or rivets through pre-drilled holes in the laminations to secure them together. Cleating, similarly, uses metal clips or cleats to hold the laminations in place. Both methods rely on mechanical fastening to maintain the stack’s integrity.
b. Benefits
Riveting and cleating provide secure assembly and flexibility in design. These methods are particularly useful when a non-permanent bond is required, allowing for easier disassembly and maintenance. Additionally, the mechanical fastening ensures that the laminations remain tightly secured, contributing to the overall stability and performance of the motor core.
4. Impact on Motor Performance and Efficiency
4.1 Reducing Eddy Current Losses
a. Explanation of Eddy Currents
Eddy currents are loops of electric current induced within conductors by a changing magnetic field. These currents flow in circular paths and can cause significant energy losses in electric motors, leading to decreased efficiency and unwanted heating. In permanent magnet motors, minimizing these losses is crucial for maintaining optimal performance and energy efficiency.
b. How Advanced Technologies Help
Advanced lamination technologies play a critical role in reducing eddy current losses. Techniques such as using thinner lamination stacks, high-quality materials, and precise manufacturing processes help limit the pathways for eddy currents to form. For instance, progressive stamping and laser welding ensure tight tolerances and clean edges, which reduce the areas where eddy currents can develop. This leads to improved motor efficiency and lower operational temperatures, ultimately enhancing the motor’s performance and lifespan.
4.2 Enhancing Magnetic Flux
a. Explanation of Magnetic Flux
Magnetic flux refers to the total magnetic field passing through a given area. In the context of electric motors, higher magnetic flux means more efficient conversion of electrical energy into mechanical energy. The design and quality of the motor laminations significantly impact the magnetic flux, affecting the overall performance of the motor.
b. Contribution of Advanced Technologies
Advanced lamination techniques such as interlocking and gluing/self-bonding contribute to better magnetic flux by ensuring precise alignment and minimal gaps between laminations. These methods create a more cohesive magnetic path, enhancing the magnetic field’s strength and consistency. As a result, the motor operates more efficiently, with higher torque and lower energy consumption. Real-world examples and case studies have shown significant improvements in motor performance when using these advanced technologies, making them a valuable asset in modern motor design.
4.3 Improving Durability and Reliability
a. Importance of Durability
Durability is essential in motor applications because it ensures long-term performance and reduces maintenance costs. Motors that can withstand harsh operating conditions and frequent use without degrading are more reliable and cost-effective over time.
b. Role of Advanced Lamination Techniques
Advanced lamination techniques such as laser welding and TIG/MIG welding provide strong, durable bonds that enhance the structural integrity of the motor core. These methods ensure that the laminations remain securely fastened, even under high stress and thermal cycling. Additionally, techniques like epoxy powder coating offer protection against environmental factors and corrosion, further extending the motor’s lifespan. Real-world examples illustrate how these technologies contribute to motors that are not only more efficient but also more durable and reliable, making them ideal for demanding applications.
5. Conclusion
5.1 Recap of Key Points
a. Summary of Advanced Lamination Technologies
Throughout this article, we’ve explored various advanced lamination technologies and their critical role in enhancing the performance and efficiency of permanent magnet motors. Techniques such as progressive stamping, compound stamping, and rotary notching are fundamental in producing high-quality laminations. Additionally, advanced lamination stacking methods, including interlocking, gluing/self-bonding, laser welding, TIG/MIG welding, and riveting/cleating, ensure precise alignment, structural integrity, and durability of motor cores. These technologies are essential for minimizing eddy current losses, enhancing magnetic flux, and improving the overall reliability of the motors.
b. Impact on Motor Performance
The impact of these advanced lamination technologies on motor performance is substantial. By reducing eddy current losses, these methods help maintain motor efficiency and prevent unnecessary energy waste. Enhancing magnetic flux through precise lamination techniques leads to better energy conversion and higher torque output. Moreover, the durability provided by advanced bonding and stacking methods ensures that motors can withstand harsh operating conditions and maintain their performance over time. Collectively, these benefits translate into more efficient, reliable, and cost-effective motors suitable for a wide range of applications.
5.2 Future Trends and Innovations
a. Emerging Technologies
As the demand for more efficient and reliable motors continues to grow, ongoing research and development in lamination technologies are crucial. Emerging trends include the use of new materials such as advanced alloys and composite laminations that offer superior magnetic properties and reduced losses. Innovations in manufacturing processes, such as additive manufacturing and advanced coating techniques, are paving the way for even more precise and efficient lamination production. These advancements are expected to further enhance motor performance, making them more suitable for demanding applications in various industries.
b. Final Thoughts
The ongoing importance of innovation in motor core lamination cannot be understated. As technologies evolve, so too must the methods and materials used in motor production to meet the increasing demands for efficiency, performance, and reliability. Manufacturers must stay at the forefront of these advancements to ensure their products remain competitive and meet the stringent requirements of modern applications. For those seeking to optimize their motor designs, investing in advanced lamination technologies and staying abreast of emerging trends is essential. By doing so, they can achieve significant improvements in motor performance, reliability, and cost-effectiveness, ensuring their motors are well-suited for the future.