1. Introduction to Induction Stator and Rotor
1.1 What are Induction Stators and Rotors?
The induction stator and rotor are fundamental components in induction motors, which are among the most widely used electric motors across various industrial, automotive, and domestic applications. The stator, typically stationary, is responsible for generating a rotating magnetic field through its energized coils. In contrast, the rotor, positioned inside the stator, responds to this magnetic field by spinning, converting electrical energy into mechanical power. The interaction between these two parts directly influences the motor’s overall efficiency and reliability. Common applications include industrial pumps, compressors, HVAC systems, conveyor systems, and electric vehicles—areas where reliability and consistent performance are crucial.
1.2 Importance of Lamination Stacking in Induction Motor Performance
Lamination stacking is the process of layering thin sheets of electrical steel—each insulated to prevent electrical conduction—to form the induction stator and rotor cores. This method significantly reduces energy losses by limiting eddy currents, which occur when magnetic fields change rapidly within solid metal components. When lamination stacking is performed precisely, it optimizes magnetic flux paths, reduces heat buildup, and significantly enhances motor efficiency and performance. For example, precisely stacked laminations can decrease energy loss by up to 15% compared to cores constructed with less accurate stacking methods.
In real-life industrial scenarios, such as manufacturing plants or data centers where motors operate continuously, even minor improvements in lamination stacking accuracy can lead to substantial energy savings and increased equipment lifespan. Furthermore, precision stacking reduces mechanical vibration and noise, enhancing motor reliability. Overall, choosing high-quality, precision-stacked laminations for the induction stator and rotor ensures consistent performance, minimizes maintenance needs, and promotes more sustainable and economical motor operations.
2. Enhanced Motor Performance Through Precision-Stacked Laminations
2.1 Reduced Eddy Current Losses
Eddy currents are loops of electrical currents induced within conductive materials by rapidly changing magnetic fields, and they are an inevitable phenomenon within electric motors. However, their presence directly contributes to energy losses, generating unwanted heat that compromises motor efficiency. The induction stator and rotor can significantly benefit from precision lamination stacking, as thin, insulated laminations restrict the paths of these currents, substantially minimizing eddy current formation. For instance, research indicates motors built with precision-stacked laminations can exhibit up to a 15% improvement in overall efficiency compared to motors utilizing loosely stacked or inaccurately aligned laminations.
A practical example of this is seen in HVAC motors, where improved lamination stacking has led to noticeable reductions in energy consumption and extended equipment lifespans, enabling manufacturers and end-users to reduce operational costs significantly.
2.2 Optimal Magnetic Flux Distribution
Achieving optimal magnetic flux distribution within induction motors is crucial, as imbalances can cause uneven torque delivery, increased wear, and potential motor vibrations. Precision lamination stacking ensures that the induction stator and rotor cores are aligned accurately, promoting uniform and consistent magnetic flux. This optimal alignment is especially valuable in industrial environments, such as conveyor systems and large-scale automation machinery, where steady and predictable torque delivery is essential for maintaining operational reliability.
A specific example can be observed in industrial conveyor belt systems, where precisely stacked cores contribute to smoother operations and reduced downtime. Such accurate alignment and stacking improve flux paths, providing uniform torque and minimizing performance fluctuations, thus ensuring stable, efficient, and predictable motor performance throughout its service life.
By carefully investing in precision-stacked laminations, engineers and manufacturers can confidently achieve enhanced performance, greater reliability, and prolonged equipment longevity.
3. Benefit 2: Improved Durability and Reliability
3.1 Minimized Vibration and Noise
Precision lamination stacking of the induction stator and rotor is essential in achieving reduced vibration and lower acoustic noise levels. Inaccurately stacked laminations can result in uneven gaps or misalignment within the motor core, leading to undesired harmonic vibrations during motor operation. These vibrations not only generate excessive noise but can also cause premature component wear and operational instability. Conversely, precision-stacked laminated cores ensure tight tolerances, uniformity, and optimal alignment of each lamination layer. This consistency minimizes structural imbalances, thereby significantly reducing noise and vibration.
A practical example can be observed in commercial HVAC systems, where precision lamination stacking noticeably reduces motor vibration and operating noise. Facilities utilizing precisely stacked induction motor cores report smoother and quieter operations, contributing to improved working environments and reduced long-term maintenance costs.
3.2 Enhanced Structural Integrity
The structural integrity of the induction stator and rotor directly impacts motor durability and reliability over extended periods of operation. Motor cores with poorly aligned or loosely assembled laminations are susceptible to deformation and mechanical stress, particularly under demanding operational conditions or fluctuating thermal loads. Precision-stacked laminations, by contrast, provide enhanced structural robustness, uniform pressure distribution, and resilience against deformation.
For instance, precision-stacked induction motors in industrial pumps and compressors often operate continuously under high stress and elevated temperatures. Precise lamination stacking ensures these motors maintain their structural integrity, reducing the risks of lamination shifting, loosening, or deformation over time. Furthermore, robust structural integrity significantly improves thermal management by evenly distributing and dissipating heat, thus reducing localized hotspots that could otherwise lead to premature motor degradation.
Overall, precision-stacked laminated cores for induction stators and rotors contribute significantly toward improved durability, decreased operational risks, and extended equipment service life.
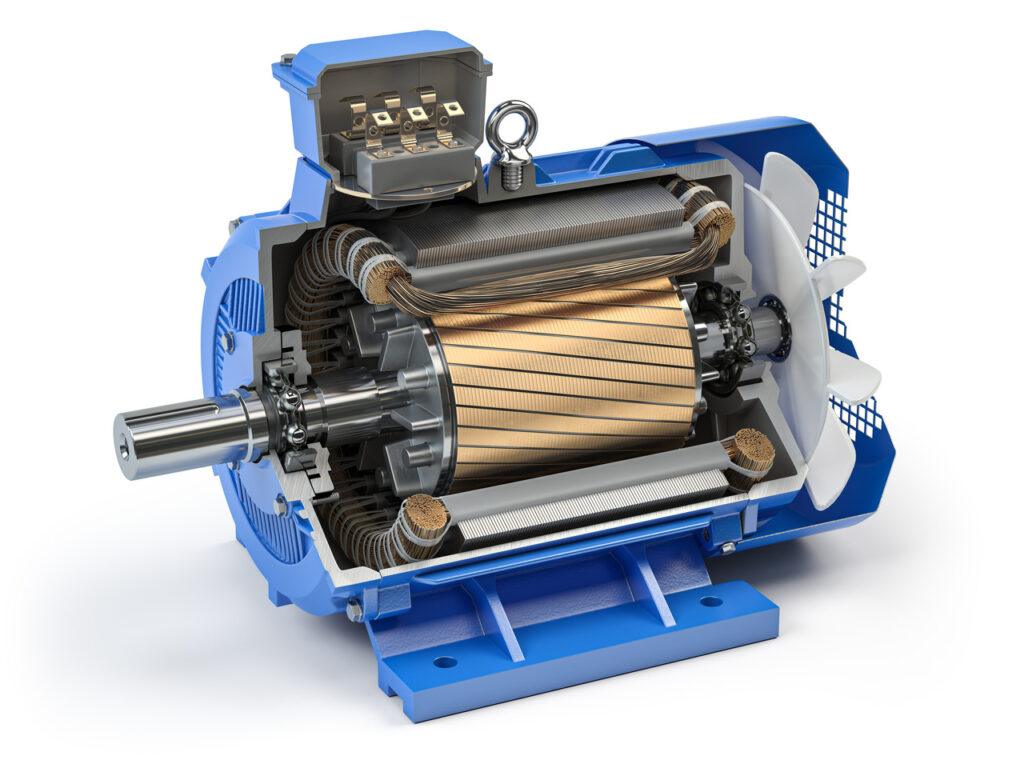
4. Benefit 3: Cost-Effectiveness and Economical Operation
4.1 Lower Maintenance Costs
Precision lamination stacking of induction stator and rotor cores directly translates into significant cost savings, particularly through lower maintenance requirements. Accurately stacked laminations reduce mechanical vibrations, operational heat, and internal friction, all of which typically accelerate wear and shorten motor lifespan. Minimizing these issues means motors require less frequent inspection, maintenance, and part replacements—ultimately resulting in substantial cost savings over time.
For instance, in industries such as manufacturing and automation, induction motors often run continuously under high loads. Here, motors with precisely-stacked laminations demonstrate reduced wear on bearings and winding insulation due to minimized vibrations and improved thermal performance. Consequently, companies can lower their spending on maintenance personnel, spare parts, and production downtime, creating a more economical and reliable operational framework.
4.2 Efficient Energy Utilization and Reduced Waste
Another critical economic advantage provided by precision-stacked laminations is improved energy efficiency during motor operation. When lamination stacks are precisely aligned and tightly fitted, the resulting optimized magnetic flux paths and minimized eddy currents significantly reduce energy losses. As a result, induction motors equipped with precision-stacked induction stators and rotors consistently deliver higher performance at lower operational energy costs.
A real-world example can be seen in commercial refrigeration systems. Businesses upgrading to motors built with high-quality, precision lamination stacks frequently report measurable reductions in energy consumption—sometimes by as much as 10% to 15% annually. These reductions in electricity costs not only lower operational expenses but also align companies with increasingly strict efficiency regulations and sustainability targets.
In summary, selecting induction motors featuring precision-stacked laminated cores offers meaningful financial benefits. Lower maintenance expenses and reduced energy consumption directly translate into improved profitability and long-term value, making precision-stacked laminations an economically advantageous choice for businesses focused on operational efficiency.
5. Benefit 4: Customization and Flexible Design Options
5.1 Tailored Solutions for Specific Applications
Precision-stacked laminations offer substantial advantages in customizing induction stator and rotor cores for various specialized applications. Unlike standardized cores, precision stacking enables manufacturers to meet specific motor performance requirements, such as unique torque characteristics, compact sizes, or enhanced thermal performance. This flexibility makes precision lamination stacking particularly beneficial for industries with stringent requirements, such as automotive, aerospace, or medical equipment.
For example, in electric vehicle (EV) applications, tailored induction motors require precisely aligned stator and rotor laminations to meet rigorous torque density and energy efficiency standards. Customized lamination stacks facilitate optimal magnetic flux distribution tailored explicitly to the motor’s intended operating conditions, thus enabling EV manufacturers to achieve performance targets without compromising vehicle range or battery life.
5.2 Scalability and Small-Batch Production Capabilities
Another key benefit of precision lamination stacking is its suitability for scalable and small-batch production. Precision techniques allow flexibility in manufacturing processes, enabling companies to quickly adjust induction stator and rotor designs and specifications according to changing market demands or specific client requests.
Consider specialized industrial automation companies, which often require induction motors customized in smaller quantities for niche applications, such as robotics or CNC machinery. Precision-stacking methods facilitate cost-effective production even at lower volumes, eliminating traditional constraints linked to minimum order quantities. This capability helps businesses respond swiftly to market changes and client specifications, maintaining competitiveness and customer satisfaction.
In summary, precision-stacked laminated cores significantly expand possibilities for customization and flexible design of induction motors, supporting diverse applications and accommodating dynamic production demands.
6. Conclusion
Precision-stacked laminations significantly enhance the performance and reliability of the induction stator and rotor. This method effectively reduces eddy current losses, optimizes magnetic flux distribution, and minimizes vibrations and operational noise. As a result, motors achieve greater energy efficiency, lower heat generation, and prolonged service life, directly translating to cost savings through reduced maintenance and downtime.
Additionally, precision stacking improves structural integrity, enhancing durability even under demanding operating conditions. Customized and scalable lamination stacks further allow manufacturers to meet specific performance criteria, especially beneficial in industries such as automotive, industrial automation, and HVAC systems. Real-world applications consistently show measurable efficiency improvements, increased reliability, and notable reductions in long-term operational expenses when utilizing precision-stacked laminations for induction motor components.
Overall, selecting precision-stacked laminated cores provides manufacturers and users with dependable, cost-effective, and versatile solutions for their induction stator and rotor applications.
Further Reading: