Motor core loss is a critical factor affecting efficiency and cost. This article takes an in-depth look at its underlying causes and provides seven strategies to mitigate it. If you’re seeking ways to optimize motor performance, be sure not to miss these expert insights.
1. What Is Motor Core Loss? (What is core loss in motors?)
1.1 The Basic Principles of Motor Core Loss
a. Hysteresis Loss
Hysteresis loss primarily occurs during the process of magnetizing and demagnetizing the material. When the magnetic field inside the motor is continuously changing, the molecules of the core material must frequently switch their magnetic orientation, consuming energy in the process. This phenomenon is closely tied to the magnetic properties of the material itself and becomes more noticeable at high frequencies or when magnetic flux changes significantly. The extent of hysteresis loss depends on the size of the hysteresis loop in the material. Therefore, choosing core materials with low hysteresis and high magnetic permeability helps reduce this portion of the loss.
b. Eddy Current Loss
Eddy current loss results from induced currents generated by the alternating magnetic field within the core, which then dissipate as heat. If the manufacturing process does not include effective insulation layers or proper lamination techniques, larger eddy current loops will form inside the material, increasing energy consumption. Using thin silicon steel sheets and ensuring adequate insulation between each sheet usually helps minimize the path of eddy currents, thereby reducing losses.
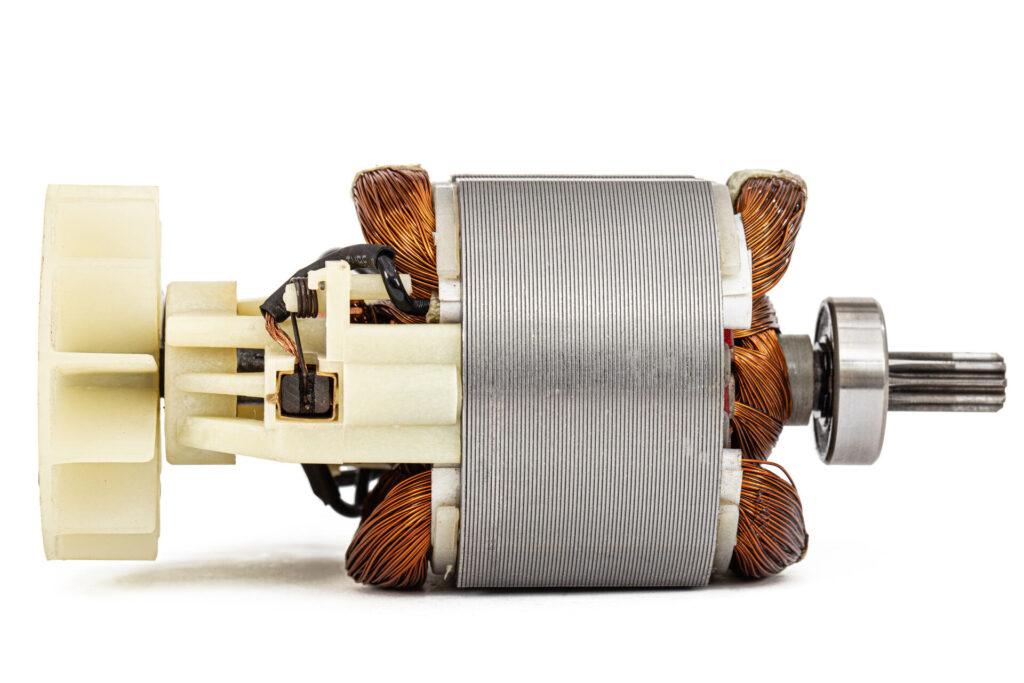
1.2 Why Focus on Core Loss
a. Its Relationship to Motor Efficiency
When people discuss “What is core loss in motors?”, they often note that core loss makes up a considerable portion of a motor’s total losses. Reducing both hysteresis loss and eddy current loss increases overall motor efficiency, thereby cutting down on energy usage.
b. Impact on Energy Costs and the Environment
The higher the core loss, the more electricity the motor requires for operation over time, leading to increased operating costs. From a conservative perspective, controlling loss appropriately not only meets energy-saving and carbon-reduction targets but also mitigates harmful environmental impacts, aligning with the global push for green energy.
c. Product Lifespan and Stability
Excessive loss generates extra heat, which, over the long run, could result in material degradation or motor failure. For users aiming to maintain equipment stability and extend product lifespan, optimizing core design and material selection is particularly crucial. Through appropriate investment and rigorous quality management, one can more effectively ensure reliable motor performance.
2. Golden Rule One: Choose High-Quality Materials
2.1 Differences Between Silicon Steel Sheets and Non-Oriented Silicon Steel
a. Material Characteristics
When exploring What is core loss in motors?, material selection is the first line of defense. A motor core is usually made of silicon steel sheets, which can be divided into non-oriented and grain-oriented types. Non-oriented silicon steel provides stable magnetic permeability in multiple directions and is widely used in various motors. If working conditions demand higher magnetic performance, grain-oriented silicon steel may be considered, though it comes with higher costs and greater processing difficulty.
b. Appropriate Application Scenarios
When choosing materials, businesses often weigh performance against cost. For high-efficiency or long-running motors, the quality of the silicon steel will determine how effectively core loss can be reduced, also influencing the motor’s temperature control and stability during continuous operation.
2.2 How Materials Affect Core Loss
a. Hysteresis Loop Shape and Size
The shape of the hysteresis loop directly affects the magnitude of hysteresis loss. Ensuring consistent silicon content and metallurgical processes typically allows the core to reduce the energy consumed during magnetization and demagnetization in real-world operation. This approach addresses What is core loss in motors? at its source.
b. Resistance to Eddy Currents
High-quality silicon steel sheets usually feature a certain level of electrical resistivity and are processed with enhanced coating treatments to minimize eddy current paths. Once eddy current loss is lowered, the heat and energy consumption produced by high-speed or high-frequency motor operation also decrease. Although actual operating conditions and material costs must be considered, from a long-term perspective, investing more in suitable materials often yields significant improvements in efficiency and lifespan.
By rigorously selecting and testing materials, companies can more effectively control motor core loss while balancing energy costs and equipment longevity. Conservatively, opting for higher-grade silicon steel may not solve every issue 100%, but it does provide a solid foundation for subsequent design and lamination processes.
3. Golden Rule Two: Optimize Lamination Design and Processing
3.1 Lamination Thickness and Manufacturing Precision
a. The Effect of Lamination Thickness on Loss
When discussing What is core loss in motors?, lamination design is a critical factor. A motor core typically consists of multiple stacked sheets of silicon steel. If these sheets are too thick, the path for eddy currents expands, which further increases loss and heat generation. Conversely, using appropriately thinner silicon steel sheets shortens the path for eddy currents, thereby reducing losses.
b. Tightness and Lamination Method
To avoid gaps or misalignment during the stacking process, strict control over alignment and fastening methods is essential. If the lamination is not tight enough, the motor may produce vibration or noise during operation, and large gaps could result in airflow that increases local heating in the core. From a conservative standpoint, while pursuing higher lamination precision raises manufacturing costs, it does help lower failure risks over the motor’s lifetime.
3.2 Processing Procedures and Advanced Techniques
a. Stamping or Laser Cutting
Whether using traditional stamping or laser cutting, it is crucial to minimize the thermal impact and stress on the edges of the silicon steel sheets. If process control is inadequate, edge burrs or crystallographic damage could lead to increased loss under high-frequency usage. Investing in top-quality stamping dies or advanced laser equipment may cost more, but it pays off in greater stability and precision.
b. Advanced Manufacturing Quality Control
Aside from the processing method, quality control plays a pivotal role. For example, during lamination, employing automated detection systems to measure sheet alignment and angles in real time can detect and rectify errors early. This greatly helps mitigate the real-world impact on What is core loss in motors?. Naturally, companies must also balance large-scale production efficiency and costs and make reasonable technological compromises.
In summary, optimizing lamination design and employing high-quality processing methods do help reduce motor core loss. However, one must continuously monitor the actual manufacturing environment to avoid sacrificing overall production efficiency and cost-effectiveness by pursuing extremely high precision.
4. Golden Rule Three: Electromagnetic Design and Winding Configuration
4.1 How Winding Structure Affects Core Loss
a. Coil Arrangement and Relative Position
When exploring What is core loss in motors?, electromagnetic design and winding configuration are indispensable considerations. Poor coil arrangement may cause localized magnetic flux concentrations in the core, leading to elevated loss and higher temperatures. Additionally, the size, shape, and placement of coils affects the distribution of the magnetic field within the core. To reduce losses without significantly increasing costs, designers often balance the number of turns, winding density, and wire gauge.
b. Air Gap Design and Loss Control
A well-planned air gap avoids unnecessary elongation of the magnetic circuit or concentrated magnetic flux. However, if the air gap is too large, torque output and efficiency might suffer; if it is too small, mechanical collision could result from manufacturing tolerances. From a conservative viewpoint, maintaining the air gap within reasonable tolerances ensures safe operation while helping manage core loss.
4.2 Electromagnetic Simulation and Optimization
a. Common Digital Simulation Tools
Today’s digital technologies let developers use electromagnetic simulation tools (for instance, finite element analysis) to preview how the windings and core generate magnetic fields in operation. By identifying regions of high loss early in the design, they can adjust geometric structure or winding configuration. Though total elimination of every loss is impossible, such methods substantially reduce experimental costs and unnecessary rework.
b. Data-Based Decisions and Ongoing Adjustments
Designers frequently iterate on winding structures to meet different application needs, comparing real-world test data with simulation results. For motor manufacturers, this conservative, step-by-step approach can balance cost-effectiveness with product longevity instead of solely chasing extreme performance. It also aids in methodically progressing toward reducing What is core loss in motors?.
Overall, optimizing electromagnetic design and winding configuration is not an overnight success, but by balancing performance, cost, and technical constraints, one can indeed lower core losses and improve operational stability and reliability.
5. Golden Rule Four: Surface Treatment and Insulation Coatings
5.1 The Importance of Insulation Coatings
a. Suppressing Eddy Currents
While studying What is core loss in motors?, insulation coatings are often recognized as a primary means of controlling eddy current loss. By applying a sufficiently thick and uniformly distributed insulation layer on the surface of silicon steel sheets, conductive paths between sheets can be significantly reduced. In doing so, the loop through which eddy currents travel is either cut off or greatly minimized. Though not a complete cure for all core losses, the quality of these coatings strongly affects overall efficiency in mid- to high-frequency applications.
b. Heat Resistance and Durability
Common coating materials include both organic and inorganic types, each offering different levels of thermal and chemical stability. From a conservative viewpoint, choosing coatings designed to withstand higher temperatures could raise initial costs but also enhance long-term insulation, reducing maintenance and failure risks. Material selection should factor in operating conditions and expected lifespan to avoid overspecifying and wasting resources.
5.2 Surface Quality and Burr Control
a. Burrs and Scratches Caused by Processing
Precision stamping or cutting techniques minimize burrs or small cracks on the edges of motor cores. If such issues are overlooked, even an even coating can be compromised by damaged edges that allow eddy currents to “sneak in.” Although eliminating burrs altogether can be challenging, process optimizations and proper post-processing can address most issues early in production.
b. Ensuring Uniformity of the Insulation Layer
When discussing “What is core loss in motors?”, the evenness of the insulation layer is just as critical. If the layer’s thickness is inconsistent, any thinner area might become a hotspot for localized losses. Many in the industry now use automated coating or spraying technology with inline inspection to monitor the distribution of the layer. While these technologies can be expensive, they boost product competitiveness by delivering better stability and higher yields.
In conclusion, careful surface treatment and well-managed insulation coatings can partially mitigate core loss, as well as reduce the risk of overheating or breakdown during long-term operation. It may not permanently solve every issue, but it certainly plays a pivotal role in practical applications.
6. Golden Rule Five: Comprehensive Testing and Quality Control
6.1 Key Areas in Process Monitoring
a. Checking Lamination Misalignment and Structural Tightness
In the deeper exploration of What is core loss in motors?, many people overlook the importance of process checks. Even slight misalignments or poor fastening in the stacking of silicon steel sheets can lead to increased energy consumption. To conservatively yet effectively reduce this risk, it is advisable to conduct periodic checks at every lamination stage—through visual measurements or automated tools—to ensure precise alignment and good structural tightness.
b. Inspecting Core Surface Defects and Coating Integrity
Besides the stacking process, tiny cracks or flaking coatings on the core surface can concentrate eddy currents and increase total loss. From a prudent standpoint, routinely checking and repairing any surface irregularities helps keep motors running reliably for longer. Though unexpected incidents may never be fully prevented, establishing robust inspection procedures greatly lowers risks.
6.2 Finished Product Performance Testing
a. No-Load Loss Testing and Balancing Checks
Upon completion of manufacturing, motors are often subject to no-load loss testing to gauge the proportion of core loss. If the readings are unusually high, a flaw may exist in one of the earlier steps (materials, lamination, or coating). Balancing should also not be overlooked, as misalignment or imbalance can drive up energy usage further. While these tests do not resolve all concerns immediately, they allow manufacturers and users to troubleshoot and act promptly.
b. Actual Operation and Temperature Monitoring
For motors expected to run over prolonged periods, no-load or short-term testing alone is insufficient for a full performance picture under real conditions. Periodic checks of operating temperature and current distribution can uncover early signs of overheating or efficiency drops. Addressing these issues at an early stage prevents further damage or failure and helps refine the understanding of what is core loss in motors? relates to real-world operations.
Overall, meticulous testing and quality control is not a one-time fix. Still, faithfully implementing these measures in a conservative and steady manner helps continually curb core loss and prolong a motor’s operational life.
7. Golden Rule Six: Proper Maintenance and Operational Management
7.1 Daily Usage and Operational Guidelines
a. Avoid Overloading and Overheating
During actual operation, excessive loads and prolonged heavy-duty running may rapidly raise the core temperature. Although certain high-grade silicon steels can tolerate heat to a degree, surpassing design limits makes the issue of What is core loss in motors? more pronounced. For a conservative yet effective approach to reducing losses, keep operating loads within rated levels and monitor motor temperature and current for any irregularities.
b. Keep the Motor Clean and Well-Cooled
Over time, dust, grease, or other debris can accumulate on the motor surface and within cooling channels. While this buildup does not directly cause higher core loss, impeded cooling can raise overall motor temperature, indirectly exacerbating loss. Periodic cleaning—ensuring that cooling fins, fans, or liquid-cooling systems work properly—helps maintain acceptable temperature levels.
7.2 Regular Maintenance and Inspection
a. Periodic Removal of Covers to Inspect the Core
Beyond standard usage, sound maintenance includes periodically opening the motor’s housing for inspection. Checking whether laminations have loosened or if coating has peeled off can spot problems affecting core loss early. Repairing or replacing damaged parts before they worsen can go a long way toward extending motor life and minimizing core loss.
b. Corrosion and Vibration Protection
In harsh or humid environments, the core surface is more prone to corrosion or loosening due to vibrations. Hence, motors should be securely mounted, ideally away from severe vibration sources. Installing shock absorbers or moisture-proof coatings can help mitigate environmental impacts. Although these measures do not guarantee the absolute prevention of all losses, they reduce many potential failures and instill greater confidence when confronted with concerns about What is core loss in motors?.
By integrating practical operational management with regular maintenance, motors can maintain better efficiency, lower failure risk, and last longer, ultimately improving the overall return on investment.
8. Golden Rule Seven: Continuous R&D and Technological Upgrades
8.1 Emerging Materials and Advanced Technologies
a. Research on High-Permeability Materials

As industry demands grow, researchers strive to discover materials with higher permeability and lower loss to further reduce What is core loss in motors?, aiming to enhance magnetic properties while maintaining structural integrity. However, such materials are often expensive or difficult to process, so a careful cost-benefit evaluation is needed. For companies wanting to stand out in an increasingly competitive market, investing in new material R&D poses risks but can yield significant competitive gains if successfully adopted.
b. Thinner Laminations and Next-Generation Coatings
Continuously reducing the thickness of silicon steel sheets and improving insulation coatings has become a major trend. Through more advanced coating materials or application processes, the likelihood of conductive paths between sheets can be further diminished, thus more effectively lowering eddy current loss. Although thinner laminations can be harder to process, with proper control, they often deliver notable efficiency boosts.
8.2 Digitalization and Smart Production
a. Big Data and Automated Production Lines
In exploring “What is core loss in motors?”, digital transformation has become crucial. Big data analytics help manage key parameters throughout the production process, enabling swift corrections of quality deviations. By adopting cutting-edge automated production lines, companies can reduce human error and more accurately control both the lamination process and coating application.
b. AI-Driven Iterative Design and Simulation
During product development, artificial intelligence can speed up design iteration and optimization. For instance, electromagnetic simulation software combined with machine learning algorithms can rapidly screen various design proposals to identify those with lower losses and higher cost-effectiveness. Although still evolving, such techniques have shown promise in certain areas. A measured, incremental approach can manage risks while steadily enhancing motor performance and reliability.
Overall, while sustained R&D and technological upgrades require long-term commitment, they are extremely valuable for reducing motor core loss and maintaining competitiveness. By prudently evaluating the feasibility of each new technology and carrying out its deployment under robust fundamentals, companies can stand a better chance of leading future industry developments.
9. Conclusion: Mastering Core Loss for a More Efficient Future
9.1 Summarizing the Importance of Managing Core Loss
Through an in-depth look at What is core loss in motors?, it’s evident that core loss significantly affects motor performance, energy consumption, and equipment lifespan. Whether from the manufacturer’s or end user’s perspective, taking steps to control hysteresis and eddy current losses ensures more reliable, energy-saving operation. While fully eliminating all losses is challenging, rigorous design, material selection, and process control can keep them within a reasonable range.
9.2 Recommended Actions and Opportunities for Collaboration
For manufacturers, every phase—material selection, lamination, electromagnetic design, and quality inspection—must be carefully coordinated to avoid nullifying the benefits of previous steps. Larger or tech-focused firms might consider partnering with specialized research groups or equipment suppliers to co-develop a new generation of low-loss motors. Such collaborations offer knowledge exchange as well as time and resource savings for equipment implementation and product testing.
9.3 Encouraging Readers to Stay Informed and Share
For a wider audience or end users interested in motor equipment, it’s important to evaluate the manufacturer’s dedication to controlling core loss. Knowing about materials, lamination techniques, and test data can help you save significantly on maintenance and energy bills in the long run. Furthermore, if you encounter abnormalities such as overheating or a steep drop in efficiency, promptly contacting a professional vendor or technician prevents further complications.
Overall, although What is core loss in motors? may appear to be a specialized topic, effectively leveraging high-quality materials, lamination and processing optimization, electromagnetic design, and insulation technologies can indeed deliver tangible benefits. By continually gathering experience, advancing technical know-how, and collaborating with industry peers, we can move toward a more efficient and sustainable future in motor development.
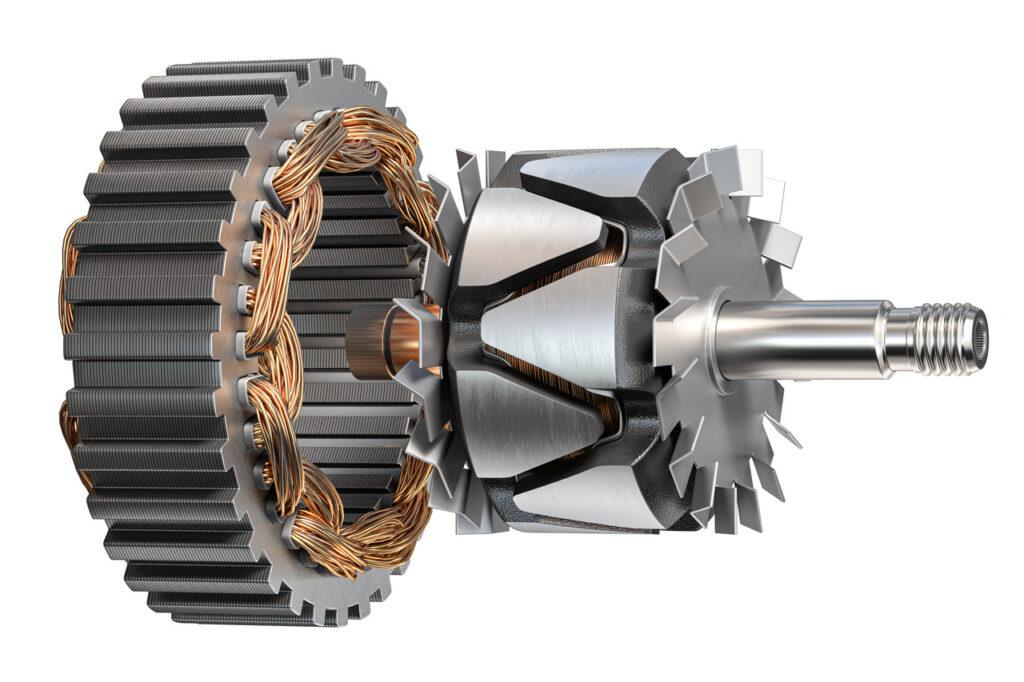
Internal links: 7 Incredible Benefits of Self Bonding Lamination Stack You Can’t Ignore
External resources: https://easa.com/resources/resource-library/the-importance-of-stator-core-loss-testing-before-and-after-burn-off-process-1