Discover how a meticulously engineered drone motor core can significantly elevate UAV performance by reducing energy loss, improving heat dissipation, and maintaining structural integrity. Learn how cutting-edge materials and precise manufacturing processes help drones achieve longer flight times and enhanced reliability.
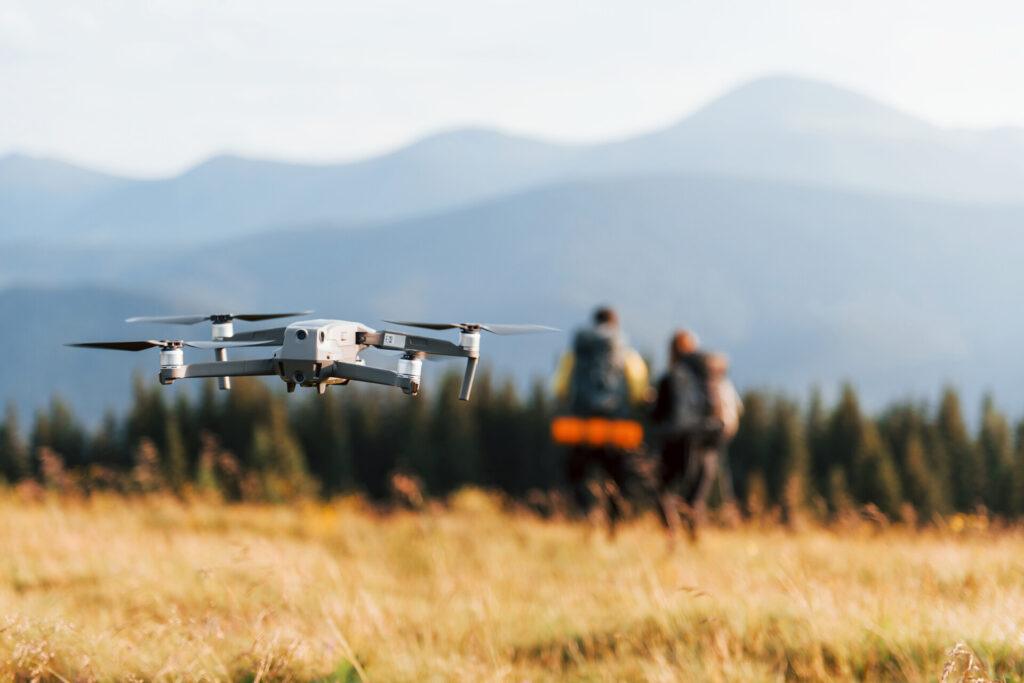
1. Introduction
1.1 Overview of the UAV Industry
a. The Multifaceted Applications and Development Trend of Drones
With continuous technological advancements, drones are being applied more and more widely across various fields. From consumer-grade aerial photography and agricultural spraying to military and commercial logistics, different types of drones are rapidly growing in the market. This diverse development has prompted manufacturers to focus increasingly on efficiency and stability in power systems to meet different payload, environmental, and endurance requirements.
b. Why Drone Motor Core Plays a Key Role in Drone Performance
The power system has always been the core of a drone, and the drone motor core is a crucial factor determining motor efficiency. If the motor core materials and manufacturing processes are not of high quality, issues like increased energy loss, reduced flight time, or motor overheating may arise. Conversely, a meticulously designed drone motor core can balance both lightweight and high performance, ensuring stable operation during extended, long-distance, or harsh-condition flights. Consequently, how to select and design an appropriate drone motor core has become a focal point for many drone manufacturers.
1.2 Purpose of the Article and Target Audience
a. Key Insights and Recommendations to be Shared
In this article, we’ll delve into five “surprising secrets” to examine how drone motor core comprehensively enhances a drone’s efficiency and durability, covering aspects such as material selection, lamination design, and coating techniques. Through these insights, readers can better understand what factors to consider when purchasing or developing core drone components to optimize flight performance.
b. Suitable Reader Groups
This content is especially well-suited for engineers, R&D teams interested in drone technology, as well as buyers and managers who need to choose a high-quality drone motor core. It also welcomes drone enthusiasts concerned about the future of UAV development, helping everyone maintain rational judgment about technology and product quality in a highly competitive market.
2. Secret One: Material Purity and Alloy Composition
2.1 The Impact of High-Purity Alloys on Performance
When building a top-notch drone motor core, the purity of the material and the alloy composition often play pivotal roles in efficiency and reliability. High-purity silicon steel or other low-loss alloys can significantly reduce eddy current losses during high-speed operations while maintaining stable magnetic flux density. If the material contains excessive impurities, such as trace amounts of aluminum or copper, it may result in decreased magnetic permeability, reducing the motor’s energy conversion efficiency during flight. Furthermore, appropriate heat treatment and annealing can effectively enhance the alloy’s structural stability, preventing characteristic degradation under prolonged high-load conditions. Overall, through rigorous metallurgy and quality control, a solid foundation can be laid for the drone motor core, ensuring it meets performance expectations across various environmental conditions.
2.2 Balancing Material Selection: Lightweight and Toughness
For drones, lightweight design and toughness are equally important factors determining flight efficiency and service life. Although high-purity alloys help boost drone motor core efficiency, using heavier materials can increase the overall flight burden and shorten endurance. Therefore, when choosing an alloy formulation, two key factors must be weighed: reducing weight and maintaining structural strength. Although thinner laminations can reduce weight and suppress eddy current losses, they may face challenges in processing difficulty and increased costs. To strike a balance, some manufacturers employ advanced composite materials or rare metal alloys to achieve higher motor efficiency without significantly increasing the overall mass of the drone.
2.3 Practical Tips for Production and Quality Control
Regardless of which alloy is used, strict production processes and quality control form the core of ensuring a premium drone motor core. Every step, from raw material inspection to casting and subsequent processing, can influence the magnetic and mechanical properties of the final product. This is particularly crucial in high-speed, long-duration drone motor operations, where even minor material defects may cause flight instability or performance loss. If companies exercise caution in selecting materials and planning production, and verify a material’s real-world performance through test reports and certification standards, they can more confidently release competitive drone motor core products and maintain a stable reputation in the rapidly changing drone market.
3. Secret Two: Lamination Design and Insulation Techniques
3.1 Thin-Layer Design and Controlling Eddy Current Loss
Laminations are a critical part of the drone motor core, with lamination thickness and configuration directly affecting the motor’s performance and flight endurance. Generally, thinner laminations help reduce eddy current losses, thereby improving overall efficiency. However, an excessive pursuit of ultra-thin laminations can lead to increased manufacturing difficulty and costs, and may even pose structural strength risks under high-speed operation. To ensure reliability, design teams often assess the optimal thickness range based on different load and speed requirements, employing precision cutting and multi-layer fastening technologies to maintain a balance between weight and durability in the drone motor core.
3.2 Insulation Coatings and Preventing Inter-Laminar Short Circuits
During high-frequency vibrations and extended operations, inter-laminar short circuits can significantly affect the performance of a drone motor core. If there is inadequate insulation protection between laminations, additional losses can occur, leading to heat buildup. Insulation coatings generally fall into two main categories: organic and inorganic. Organic coatings are easier to apply and offer a certain level of flexibility, but have limited heat resistance. Inorganic coatings boast better temperature tolerance and flame resistance but require more complex application processes. Given drones operate in various challenging environments, choosing the proper type and thickness of coating becomes critical. Moreover, regular inspections and maintenance help prevent aging or peeling of the coating, ensuring the drone motor core consistently delivers stable performance over time.
3.3 Key Details and Holistic Coordination
While striving for high efficiency and light weight, lamination design and insulation technology do not function independently; they must integrate with factors such as material composition, processing precision, and cooling structures. Enterprises or R&D units that develop comprehensive design processes early in projects—and use thorough testing and data analysis to refine parameters—are more likely to precisely determine the best combination of laminations and insulation. In this way, the drone motor core can balance both stability and performance in the fast-evolving UAV market, providing users with long endurance and high efficiency, while also ensuring flexibility for future maintenance and upgrades.
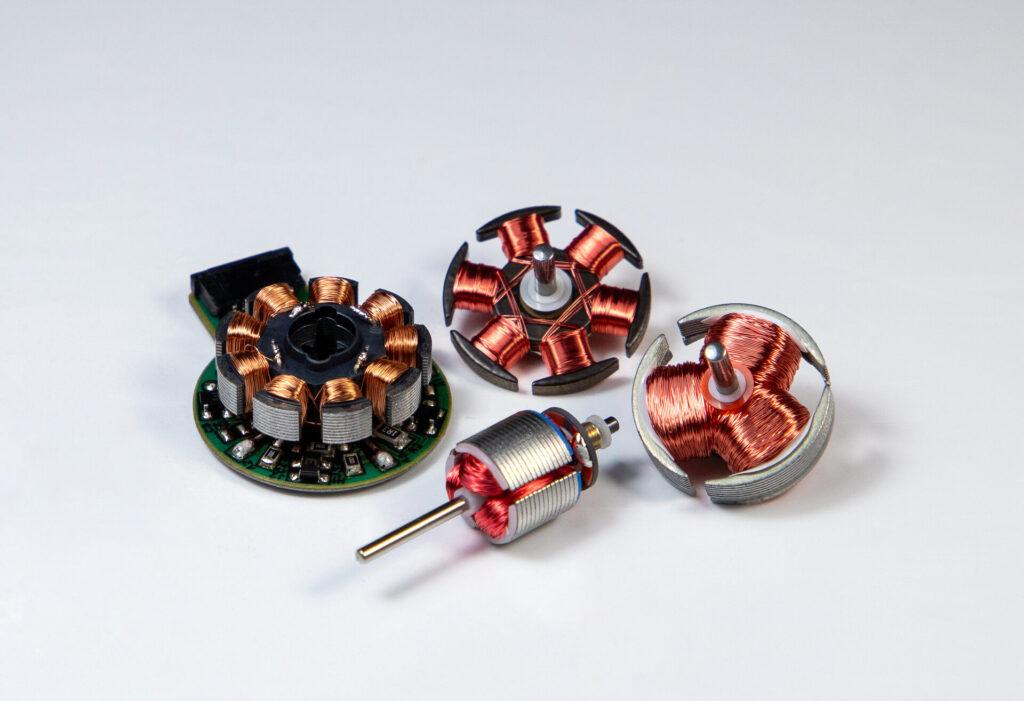
4. Secret Three: High-Precision Manufacturing and Assembly Quality
4.1 The Importance of Cutting and Stamping Precision
During the production of drone motor core, cutting and stamping precision is of paramount importance to overall performance. If strict controls are not implemented at the mold design and processing stages, lamination edges may develop burrs or micro-cracks, leading to uneven surfaces that increase losses. Moreover, mold materials and stamping speed must be finely matched to accommodate both large-scale production and quality. For drones that demand high operational efficiency, even minimal deformation or dimensional errors will manifest during drone motor core operation, resulting in energy losses or instability. Therefore, ensuring precision stamping and cutting at the production stage not only helps maintain stability under high-speed conditions but also prolongs the product’s lifespan.
4.2 Automated Assembly and Tolerance Control
After cutting, the assembly phase plays an equally critical role. When a large volume of laminations is stacked in a high-speed automated fashion, lax tolerance control can lead to uneven gaps, incomplete fastening, or localized misalignment. Though these issues might be hard to spot visually, they can degrade drone motor core performance during real-world operation. Automation reduces human error but requires a precise detection system and real-time feedback mechanism. Any anomaly or assembly error discovered in tolerance measurements must be swiftly addressed or defective units removed. Only then can every batch of core motor parts meet the drone’s rigorous requirements for high efficiency and stability.
4.3 Comprehensive Evaluation and Quality Management
In these two crucial steps—high-precision manufacturing and assembly quality—the advantages of drone motor core can be fully realized. Companies or R&D teams that set up strict quality control procedures—such as regular checks on cutting precision, stamping speed calibration, and dynamic balance tests—can more effectively reduce future maintenance or customer complaints. In sum, the collaboration between process details and assembly quality forms the foundation of high-efficiency drone motors, while a professional and prudent approach remains a key to sustaining trust in drone motor cores in the marketplace.
5. Secret Four: The Dual Challenge of Cooling and Mechanical Strength
5.1 Cooling System Design and Thermal Management
During high-speed operations or long-duration flights, the motor temperature can rise sharply. If the drone motor core cannot effectively dissipate heat, an overly hot environment accelerates material aging and can lead to performance instability. To address this challenge, many R&D teams pay special attention to thermal conductivity and the layout of cooling channels when designing a drone motor core. If the core structure incorporates suitable air vents or heat exchange mechanisms, efficiency can be increased while the motor’s temperature remains in a safe range. In terms of material selection, alloys or composites with excellent thermal stability are often considered first. When cooling is well-managed, overall flight endurance and motor lifespan see corresponding improvements.
5.2 Mechanical Strength and Vibration Considerations
On the other hand, mechanical strength is also essential in drone motor core design. During takeoff, landing, and high-speed flight, drones are exposed to vibration, wind resistance, or sudden load shifts. If the laminations or fastening structures lack sufficient strength, prolonged vibration can lead to loosening or metal fatigue, significantly undermining motor performance. To reduce this risk, manufacturers often invest heavily in stack tolerances and fastening methods (such as welding, riveting, or resin bonding). They may also conduct dynamic balancing tests and centrifugal force experiments to verify that the drone motor core remains stable under high-speed rotation.
Overall, cooling and mechanical strength are not opposing factors but rather elements of an integrated design. If every aspect— from material selection and lamination arrangement to the overall structure—is considered collectively, supplemented by proper quality control and testing procedures, drone motor cores can achieve both high efficiency and long-term stability in demanding UAV applications. Although these methods require additional R&D investment and production costs, they undeniably enhance product competitiveness and ensure flight safety in a rapidly changing market.
6. Secret Five: Future Trends and Customization
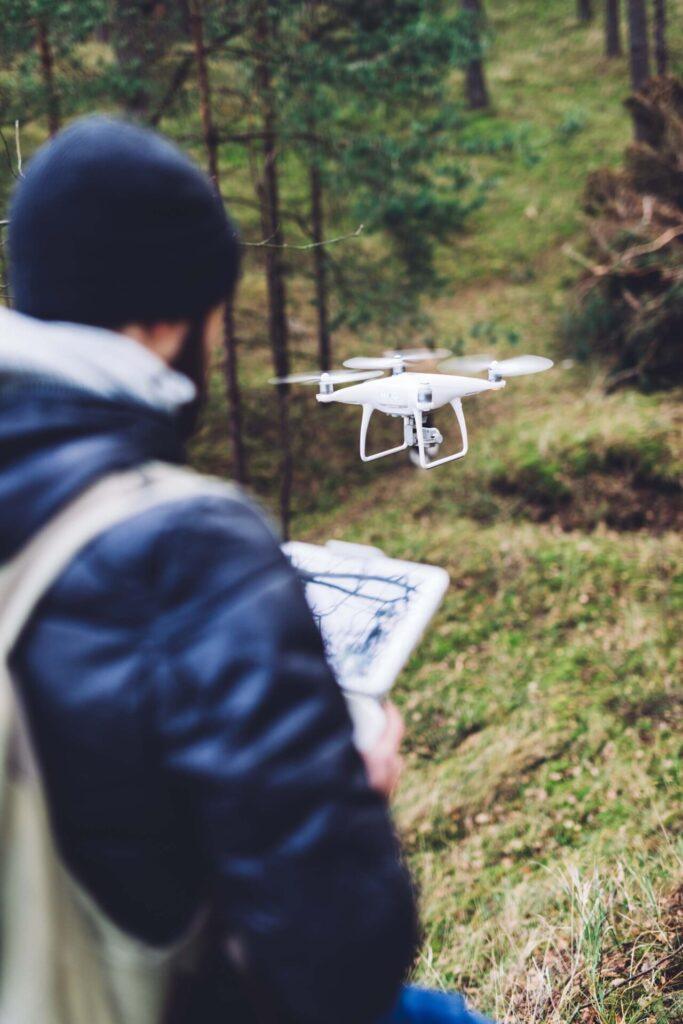
6.1 Research and Development for Lightweight Materials
As the UAV market continues to grow and expand into new applications, lightweight design has become one of the primary trends in drone motor core development. This is particularly true for long-distance flights or scenarios that require more sensors. How to reduce the mass of the core component while maintaining mechanical strength and cooling efficiency has become a key challenge for R&D teams. In recent years, amorphous alloys, composites, and high-performance rare metals have been gradually gaining attention. These advanced materials can mitigate eddy current losses while offering superior heat and vibration resistance. However, it’s important to note that breakthroughs in material technology often come with higher costs and manufacturing complexities. As a result, companies typically undertake in-depth market analysis and small-scale tests before moving to full-scale production, ensuring their investment reaps adequate returns in the continuously evolving UAV market.
6.2 Customization and Market Applications
In the face of diverse flight task requirements, standardized drone motor core designs are no longer sufficient to meet all needs. Some industries—like agricultural spraying or forest inspection—may emphasize longer endurance and wear resistance, while logistics and delivery applications require relatively stable output power under high loads. To meet these differing needs, customized motor core designs have emerged, tailoring lamination thickness, insulation grades, and cooling structures. Of course, not all customized solutions can immediately be mass-produced; they also need to undergo multiple rounds of testing and validation to ensure the drone motor core remains reliable in different environments. Meanwhile, partnering with suppliers who possess extensive expertise and R&D experience is vital for increasing the success rate of customization.
Overall, the UAV market is poised to keep expanding and evolving, creating greater innovation demands on lightweight, high-efficiency drone motor cores. Only through professional evaluation and safety risk management—and by gradually introducing new technologies and customized solutions—can businesses progress steadily in a highly competitive field and create more real-world value for users and the industry.
7. Conclusion and Recommendations
7.1 Reviewing Five Core Takeaways
Based on the breakdown of the “secrets” above, we see that the drone motor core plays a critical role in UAV performance. From material purity and alloy composition, lamination design and insulation techniques, high-precision manufacturing and assembly, to cooling and mechanical strength, as well as the trend toward customization, each factor can influence ultimate flight stability and endurance. While each stage poses different technical challenges, an integrated approach—investing sufficient time and resources early in product development—often yields higher efficiency returns.
7.2 Guide to Selection and Evaluation
For companies and R&D teams currently selecting or developing a drone motor core, the following considerations are recommended:
- Clarify Requirements: Identify your operational scenarios, including flight duration, payload capacity, and environmental conditions (such as high temperature or heavy vibration).
- Materials and Process: Choose materials that balance performance and cost, and ensure lamination and insulation techniques are suitably robust.
- Precision Management: Strictly control cutting and assembly tolerances, incorporating automated detection systems to reduce defect rates in mass production.
- Cooling and Mechanical Strength: Plan an appropriate cooling pathway based on flight characteristics, and ensure the structure is adequately protected against vibration and impact.
- Continuous Innovation and Testing: Continuously monitor emerging materials and customization demands; validate R&D results with repeated testing before integrating them into production.
7.3 Long-Term Outlook and Risk Management
While new lightweight materials and customization services have promising prospects for drone motor core applications, each technological upgrade entails higher costs and risks. In the pursuit of market leadership, companies shouldn’t overlook subsequent maintenance and safety issues. Adopting a relatively cautious approach and incrementally integrating R&D results into mass production can solidify technical strength and satisfy market needs. In a drone industry growing ever more competitive, stable product quality and a scientific development model form the key cornerstones for ensuring ongoing improvements in efficiency and reliability of the drone motor core. By collaborating with professional teams and advanced supply chains, there may be further opportunities to demonstrate tangible value in emerging industries, thereby broadening the possibilities for drone applications.
External resources: https://www.researchgate.net/publication/339639377_Increasing_the_efficiency_of_a_drone_motor_by_arranging_magnetic_sheets_to_windings
Internal links: 3 Crucial Reasons Your Drone Motor Assembly Demands Top-Quality Laminations