Discover how Frameless Torque Motor Cores are empowering a new wave of Humanoid Robots with enhanced torque density, compact design, and remarkable efficiency. Learn how these cutting-edge components may redefine robotic performance in areas ranging from healthcare to advanced manufacturing.
1. Introduction
1.1 The Rising Demand for Humanoid Robots
Humanoid Robots are steadily gaining traction in fields like manufacturing, healthcare, and hospitality. They promise to handle tasks that require human-like dexterity and decision-making, offering potential solutions for labor shortages and demanding workloads.
Despite this promise, many organizations remain cautious. Ensuring safety, reliability, and return on investment is vital before committing to large-scale deployment of these advanced machines. In healthcare, for instance, some facilities are experimenting with humanoid robots for patient assistance, showcasing real-life applications that blend precision and empathy.
The overall outlook is hopeful yet measured. As research and development continue, engineers and business leaders emphasize robust testing and incremental improvements. This approach ensures that Humanoid Robots not only function effectively but also integrate seamlessly into human environments.
1.2 Understanding Frameless Torque Motor Cores
Central to a humanoid robot’s motion control system is the choice of motor technology. Frameless Torque Motor Cores stand out here due to their compact structure—consisting of only rotor and stator components—and their capability to deliver high torque in tight spaces, such as robotic joints.
Unlike traditional motors that come with extensive housings, Frameless Torque Motor Cores can be embedded directly into the joint assembly. This reduces overall weight and optimizes space utilization, which is critical for maintaining natural movement and balance in Humanoid Robots. Through precise lamination stacking and efficient winding configurations, these motor cores can also exhibit improved thermal performance and lower energy consumption.
Their application, however, requires careful consideration of materials, tolerances, and integration procedures. Optimal results come from matching motor specifications to each joint’s torque and speed requirements. As more industries explore new ways to build reliable and responsive humanoid robots, Frameless Torque Motor Cores are emerging as a key ingredient in achieving consistent, human-like motions.
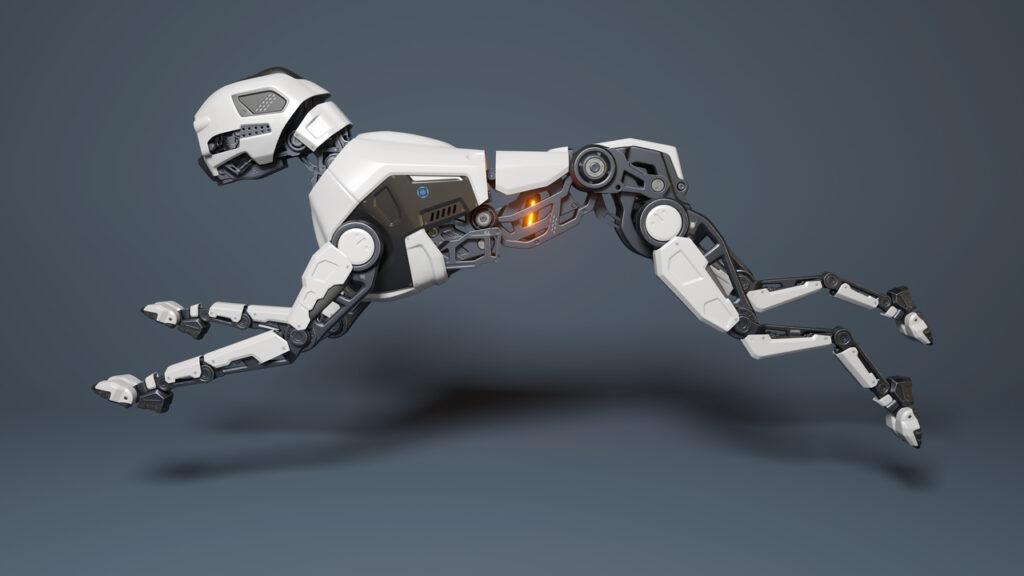
2. Five Astonishing Benefits of Frameless Torque Motor Cores
2.1 Benefit #1: High Torque Density
Frameless Torque Motor Cores offer impressive torque density, which is crucial for Humanoid Robots that need smooth and precise movements. By maximizing the magnetic flux in a tightly stacked lamination design, these motor cores can provide high torque output without requiring a larger footprint. This advantage is particularly evident in robotic joints responsible for lifting or supporting substantial payloads.
2.2 Benefit #2: Compact and Lightweight Design
In many advanced robotics applications, space is limited, and every gram matters. Frameless Torque Motor Cores excel here because they eliminate bulky housings, integrating directly into the joint assembly. For Humanoid Robots, a lower overall mass helps improve balance and agility. Real-life examples include robotic arms that must manage tasks in confined workspaces or deliver delicate, human-like handling.
2.3 Benefit #3: Superior Thermal Management
Effective thermal management can be difficult in dense mechanical systems, but Frameless Torque Motor Cores mitigate heat buildup through strategic lamination stacking and efficient winding configurations. By reducing eddy current losses, these motor cores maintain stable operating temperatures over extended periods. This approach is advantageous for critical applications, such as long-duration manufacturing tasks, where overheating could compromise both safety and performance.
2.4 Benefit #4: Design Flexibility
Because they come without a fixed housing, Frameless Torque Motor Cores can be adapted to various shapes and sizes. Engineers can customize factors like stator diameter or rotor thickness to meet specific torque and speed requirements. In Humanoid Robots, different joints—from shoulders to wrists—often require unique designs. This flexible configuration supports streamlined, compact builds while retaining essential performance metrics.
2.5 Benefit #5: Enhanced Efficiency and Performance
Finally, Frameless Torque Motor Cores can boost the overall efficiency of Humanoid Robots by minimizing mechanical losses and optimizing power usage. With fewer internal components and direct integration into the assembly, they reduce friction and inertia. The outcome is smoother motion, consistent torque delivery, and a lower energy draw—all vital traits in cutting-edge robotic systems.
3. Product Information and Practical Applications
3.1 Key Specifications of Frameless Torque Motor Cores
When evaluating motor cores for advanced robotic applications, engineers often start by examining material properties. Laminations typically use silicon steel or specialized alloys to optimize magnetic permeability and reduce eddy current losses. This choice enhances efficiency while also contributing to lower heat generation during extended operation.
Precision in stacking and winding is another critical factor. Thinner lamination layers can mitigate power losses, but too thin a profile may increase manufacturing complexity. Finding the right balance involves considering overall torque requirements, rotational speed, and desired longevity. Moreover, integrating sensors and encoders directly into the motor core assembly enables real-time monitoring of torque, position, and temperature. Such data proves indispensable for fine-tuning motion control algorithms in complex robotic joints.
3.2 Use Cases in Humanoid Robotics
In the realm of agile automation, carefully chosen motor cores can significantly impact how effectively robotic joints mimic human movements. Although full-scale adoption varies by industry, some manufacturing plants already employ anthropomorphic robots for assembly tasks that demand both dexterity and safety. Compact motor designs allow these robots to navigate narrow production lines without sacrificing torque or precision.
Healthcare represents another promising avenue, especially for rehabilitation devices. Modular exoskeletons, for instance, increasingly rely on compact rotor-stator assemblies to provide controlled assistance for patients undergoing physical therapy. By tailoring torque output to an individual’s needs, these systems can help enhance patient outcomes while maintaining reliability. As research continues and more real-world applications come to light, motor technology will likely evolve to accommodate higher load capacities and further integration with emerging sensor suites.
Though success depends on a host of variables, the common thread remains a focus on efficient, space-saving motor solutions. In many forward-looking projects, a well-chosen lamination stack can mean the difference between a functional prototype and a robust robotic platform suited for evolving demands.
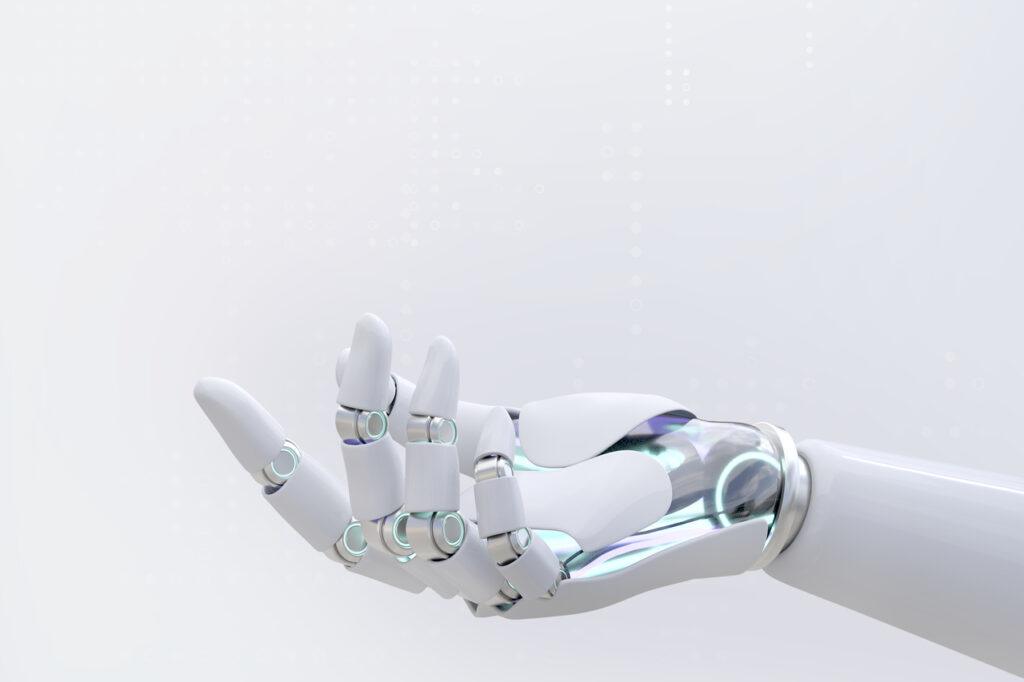
4. Conclusion
4.1 Summary of Key Takeaways
Frameless Torque Motor Cores have demonstrated clear advantages in robotic applications, offering high torque density, compact construction, and improved thermal performance. By tailoring materials, lamination thickness, and winding specifications, engineers can enhance overall efficiency without adding unnecessary bulk. These benefits become especially valuable in Humanoid Robots that must balance agility with precision.
Throughout the discussion, it is evident that design flexibility allows developers to create bespoke motor configurations for various joints, ranging from elbows to ankles. Real-life case studies in industries such as healthcare highlight how controlled torque delivery and smaller system footprints can make specialized tasks more achievable. While no single approach fits every robotic design, well-chosen motor cores can be a reliable foundation for building effective, human-like machines.
4.2 Future Outlook for Humanoid Robots and Frameless Torque Motors
Looking ahead, ongoing research in materials science is poised to refine the capabilities of frameless motors further. Advanced alloys and specialized magnetic laminations may reduce power losses and boost torque output even more. In parallel, evolving sensor technologies and data-driven control algorithms will likely improve the coordination of robotic limbs, enhancing both motion quality and operational safety.
However, broader adoption will also depend on cost-effectiveness, reliability in real-world environments, and regulatory considerations. Some manufacturers are cautiously optimistic, implementing incremental upgrades to observe how these technologies perform under prolonged stress. Meanwhile, collaborative projects between academia and industry continue to explore novel applications of Humanoid Robots, from patient rehabilitation to customer service.
Ultimately, embracing these emerging solutions with a measured approach can yield innovative, long-term benefits. As engineers refine designs and end users gain practical experience, Frameless Torque Motor Cores may prove increasingly crucial for bringing the next generation of humanoid robotics closer to everyday reality.
Further Reading: