“Dive deep into the application of PMSM motor cores in high-precision humanoid robots and grasp the key aspects of their efficiency and future development. Through a comprehensive selection guide and case studies, you can create a stable, efficient, and forward-looking robotic solution.”
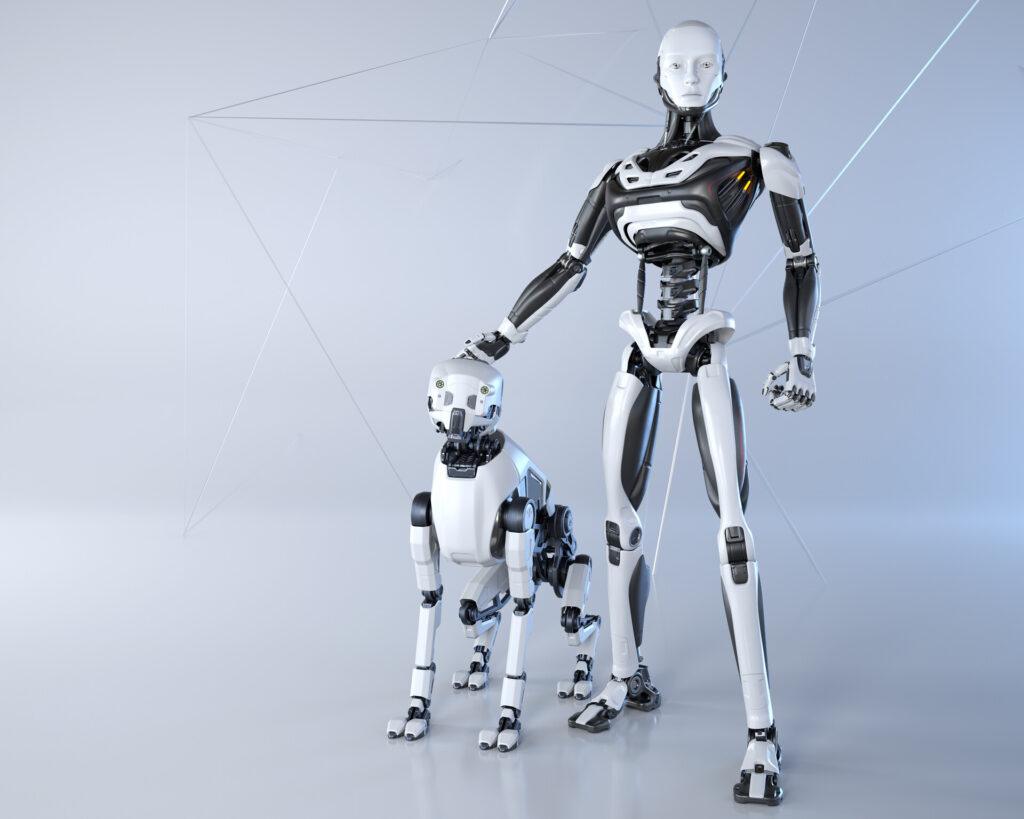
1. Introduction to PMSM Motor Cores
1.1 What is a PMSM Motor Core
A PMSM motor core (Permanent Magnet Synchronous Motor Core) is a key component in permanent magnet synchronous motors, consisting mainly of laminated sheets in both the stator and rotor. These laminations are typically made of specially processed high-silicon steel sheets to reduce eddy current losses and enhance overall performance. Because the PMSM motor core provides high efficiency and high power density while effectively reducing heat generation and noise during operation, it plays a pivotal role in many precise application fields.
1.2 The Basic Principles and Characteristics of PMSM Motor Cores
A PMSM motor core can produce stable and continuous torque primarily due to the electromagnetic interaction between the permanent magnets in the rotor and the windings in the stator. When current passes through the stator windings, a rotating magnetic field is generated in the PMSM motor core, driving the rotor to rotate in sync. Its key characteristics include high efficiency, robust torque output, and excellent dynamic response. This means that in the same or smaller size, the PMSM motor core can provide more powerful output and quickly adjust motor speed and torque under varying loads.
1.3 Why PMSM Motor Cores Are Suitable for Humanoid Robots
Humanoid robots need to mimic complex movements such as walking, balancing, and grasping objects, which demand extremely high precision and dynamic response from their motors. Thanks to its rapid response and high efficiency, the PMSM motor core can deliver smooth and highly accurate motion control in joint drives. In addition, its relatively low noise and vibration levels help ensure comfort and stability during robot operation. However, despite the clear advantages of PMSM motor cores, factors such as heat dissipation, cost, and system integration should still be considered when evaluating their use in humanoid robots to achieve the best balance in real-world applications. By carefully selecting and customizing designs, a PMSM motor core can truly leverage its strengths, enhancing both the motion performance and overall reliability of humanoid robots.
2. Principles and Characteristics of PMSM Motor Cores
2.1 Basic Structure and Electromagnetic Interaction
A PMSM motor core plays a critical role in transmitting electromagnetic energy within a permanent magnet synchronous motor. Essentially, when the stator windings are energized, they create a rotating magnetic field that interacts with the permanent magnets arranged on the rotor, producing attractive or repulsive forces that drive the rotor to rotate in sync. Throughout this process, the structure, materials, and manufacturing quality of the motor core directly affect both the torque output of the rotor and the stability of operation.
2.2 Materials and Lamination Thickness
To optimize the overall efficiency of a PMSM motor core, many manufacturers choose high-silicon steel sheets as the primary material and use precision stamping or laser cutting techniques to produce laminations of specific shapes and thicknesses. Thinner laminations help reduce eddy current losses but can lead to higher processing complexity and cost. Therefore, design and material selection must strike a balance among efficiency, stability, and budget considerations.
2.3 Efficiency and Power Density
PMSM motor cores offer high power density and low losses, often delivering robust power in a relatively compact form factor. This is especially crucial for humanoid robots that must perform various complex movements. Higher efficiency means they can maintain steady output over longer periods, reducing energy consumption and minimizing heat buildup. However, actual performance in operation can still be limited by factors such as motor cooling design and the degree of system integration.
2.4 Potential Limitations and Considerations
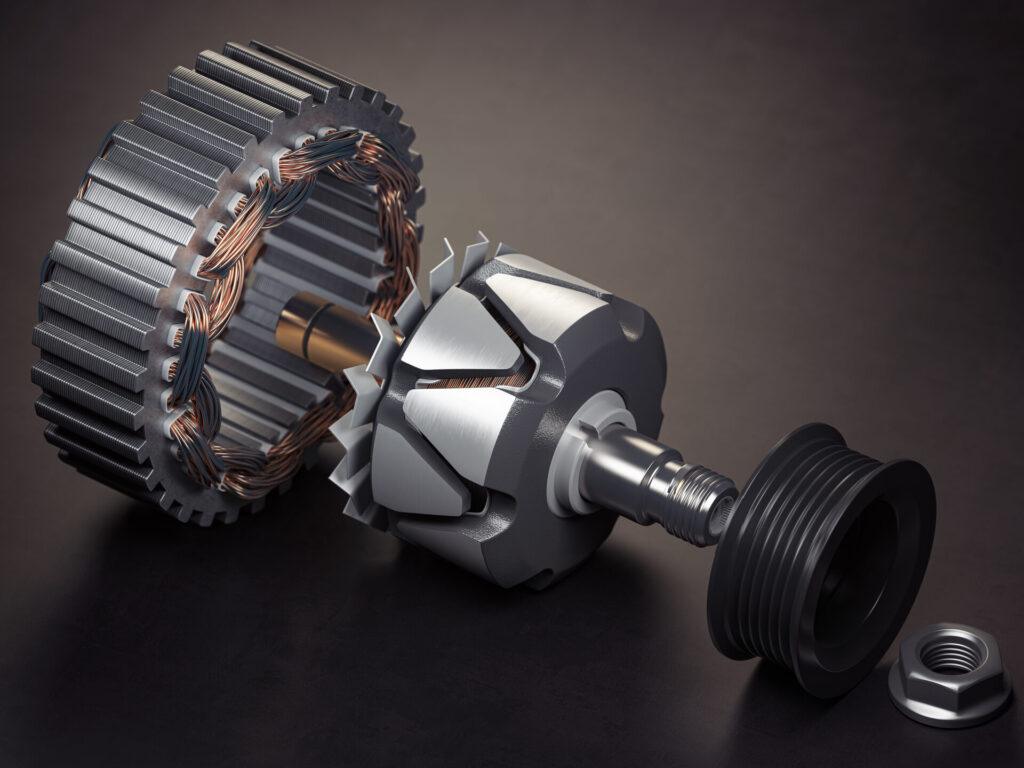
Although PMSM motor cores come with many advantages, several constraints may arise depending on specific applications—such as higher costs, complex manufacturing, and potential heat dissipation requirements. For humanoid robots, it is equally important to sustain long-term operation and achieve precise control. When evaluating a PMSM motor core, it is essential to carefully review aspects like durability, material stability, and ongoing maintenance costs to achieve the optimal balance of performance and reliability.
3. Key Factors Influencing Humanoid Robot Performance
3.1 High Dynamic Response and Torque Output
In humanoid robots, the ability to move joints rapidly and accurately is critical, as they must simulate subtle human movements such as walking, balancing, and grasping. If a PMSM motor core can instantly deliver sufficient torque while maintaining smooth operation, it will contribute to the overall stability of the robot. The primary advantages of such motors lie in their high power density and outstanding torque control. However, in practical applications, advanced control strategies and high-precision sensors are still needed to ensure that humanoid robots can swiftly receive feedback and adjust when switching between movements.
3.2 Weight and Space Considerations
Humanoid robots have multiple joints arranged throughout the torso and limbs. If the motor components are overly heavy or bulky, they can negatively impact the system’s agility and energy consumption. During the design phase, a PMSM motor core typically focuses on balancing lightweight construction and high efficiency, striving to reduce system weight while providing sufficient power. However, lightweight materials often come with higher manufacturing costs and additional requirements for machining precision and cooling mechanisms. Consequently, development teams must select the most suitable solution that balances budget constraints with reliability.
3.3 Control Precision and Reliability
For humanoid robots, accurately executing complex movements and maintaining stability during extended operation are both crucial benchmarks of system maturity. If a PMSM motor core can operate with low vibration and noise, it becomes easier for the controller to obtain precise feedback signals, thus improving overall motion accuracy and safety. However, the higher the degree of system integration, the more rigorous the demands on design and testing. Factors such as heat dissipation, insulation strength, and compatibility between the motor and controller must all be considered. Only when every aspect is well-balanced can a humanoid robot achieve the high precision and reliability it requires.
4. Five Essential Keys to Choosing the Most Powerful PMSM Motor Core
4.1 Power Density and Efficiency
When selecting a PMSM motor core, power density and efficiency are often top priorities. Higher power density indicates stronger output within the same volume, aiding humanoid robots in performing complex tasks while minimizing system footprint. In terms of efficiency, operating with lower energy consumption while maintaining high output can positively impact overall running costs and reduce heat accumulation. However, despite the allure of high-efficiency designs, it remains important to assess various load conditions and usage scenarios to ensure performance aligns with real-world demands.
4.2 Reliability and Durability
Humanoid robots frequently endure long periods of operation and numerous repetitive movements, so they place rigorous demands on the reliability and durability of a PMSM motor core. If the motor core’s materials and manufacturing processes are substandard, it can lead to overheating or performance degradation. It is recommended to check whether the product has passed fatigue testing or meets relevant quality standards during the initial selection phase to ensure long-term stability.
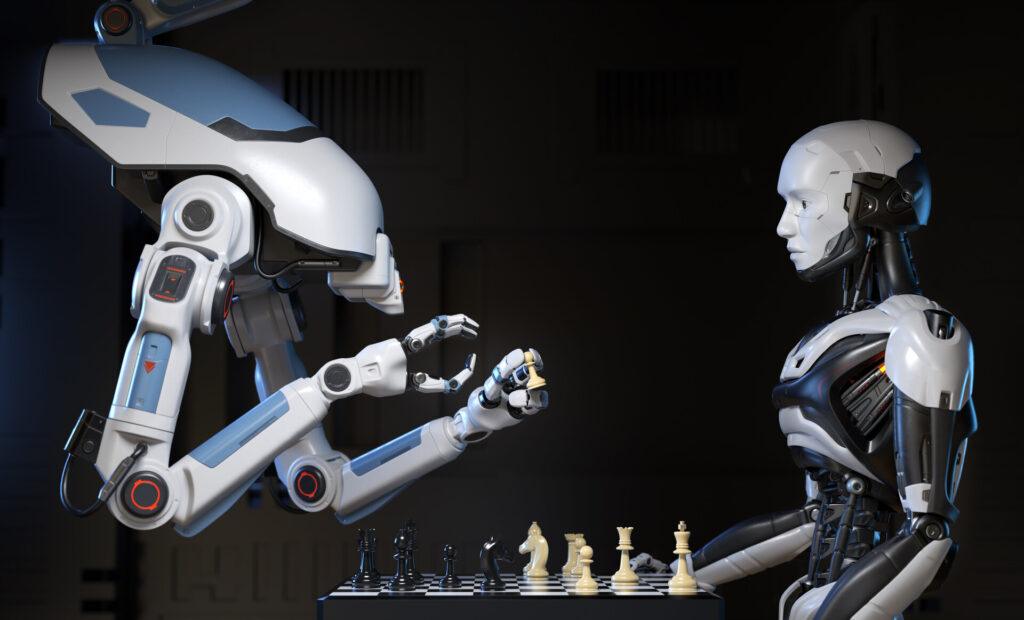
4.3 Cost and Integration
While a high-quality PMSM motor core may deliver superior performance, it can also escalate overall costs in both development and mass production. Additionally, the degree of integration between the motor core and the robot’s controller and sensors should not be overlooked. If the product fails to blend seamlessly with the existing system, additional tuning and maintenance costs may arise. Hence, when evaluating expenses, it is crucial to factor in the costs of integration and maintenance.
4.4 Manufacturer and Technical Support
Choosing a manufacturer with extensive research and development experience and robust after-sales service is essential for ensuring the quality of the PMSM motor core. In the field of humanoid robots, if the manufacturer can offer customized designs for various joints and movement requirements, it will help the development team achieve a balance between performance and reliability. Furthermore, comprehensive after-sales and technical support can shorten the product’s adoption period and reduce operational risks.
4.5 Future Upgrades and Scalability
Humanoid robot technology advances rapidly, and if a PMSM motor core has room for future upgrades, it will hold stronger long-term potential. For instance, after optimizing control algorithms or making breakthroughs in materials, the motor core could be upgraded or expanded via modular design to meet higher precision or more complex application requirements. Not only does this approach help maintain system competitiveness, but it also offers greater flexibility over the product’s lifecycle.
5. Successful Application Cases and Future Trends
5.1 Successful Application Cases
Many leading industries have already adopted PMSM motor cores for humanoid robots, showing promising results across different domains. For instance, some manufacturing plants employ humanoid robots equipped with high-efficiency PMSM motor cores for assembly and inspection tasks that require precision and repetitive motion. Because these motor cores provide stable torque output and low energy consumption, the robots can maintain reliability even during extended operation, minimizing downtime losses. In service sectors such as hospitals, hotels, and shopping malls, humanoid robots are used for guidance or simple interactions; the low noise and high stability offered by PMSM motor cores further enhance comfort and user experience.
5.2 Technology Integration and Innovation
With ongoing advancements in control algorithms, sensors, and AI, PMSM motor cores are also continuously evolving. Research institutions and companies are actively integrating AI systems into motor controls, enabling humanoid robots not only to sense their environment but also to learn and adjust movements in real time, significantly improving agility and interactivity. Meanwhile, the development of new materials and manufacturing techniques is enhancing the cooling efficiency, strength, and weight optimization of motor cores, providing a more stable foundation for humanoid robots facing complex tasks.
5.3 Future Outlook
Looking ahead, humanoid robots are expected to shine in an even broader range of applications—from assisting high-precision operations in factories to delivering services in communities and public spaces. This growth in demand implies that PMSM motor cores will continue to surge in popularity, driving further technological breakthroughs. However, diverse usage scenarios also bring about simultaneous design and integration challenges. If reliability, cost, and scalability can all be balanced, along with continually updated AI algorithms, humanoid robots will progress toward greater intelligence and stability, generating more potential value for various industries.
6. Conclusion
6.1 Summary of Benefits
From the discussions above, it is evident that PMSM motor cores possess high efficiency, high precision, and superior cooling capabilities when applied to humanoid robots. These characteristics enable long-term stable operation in a variety of complex work environments while maintaining relatively low energy consumption and maintenance costs. However, despite the many advantages of PMSM motor cores, comprehensive system design and integration—including choosing suitable controllers, sensors, and mechanical structures—remain essential. Only by creating a sound balance among these critical factors can a PMSM motor core truly reach its full potential.
6.2 Suggested Actions
For developers or enterprises evaluating humanoid robot projects, the first step is to carefully analyze requirements such as system load, precision, and budget, then select the appropriate motor core specifications. If funding allows, high-end materials or customized designs often deliver better performance, though the return on investment and real-world applications should also be weighed. Moreover, collaborating with manufacturers who possess extensive R&D experience and technical support can prevent many potential risks and ensure the necessary resources and after-sales services are available during later project phases.
6.3 Future Collaboration Opportunities
As humanoid robots become more prevalent across industries and daily life, demand for PMSM motor cores will naturally increase. In the future, combining AI, smart sensors, and new material technologies may enable humanoid robots to achieve even greater agility and intelligence. For businesses and development teams, partnering with motor core suppliers who hold forward-looking perspectives is key to staying ahead in the market. Through mutual commitment to research and innovation, PMSM motor cores are expected to remain indispensable in a diverse range of applications, providing a strong and reliable technological foundation for the continued evolution of humanoid robots.
Internal links: 5 Incredible Benefits of Using Silicon Steel in AI Robot Electric Motors
external links: https://ieeexplore.ieee.org/document/7465636