1. Introduction to Linear Motor Lamination
1.1 Understanding the Concept and Importance
Linear motor lamination refers to the process of stacking thin, carefully cut electrical steel sheets—also known as laminations—into a precise configuration that forms the core structure of a linear motor. Unlike traditional rotary motors, which rely on rotational movement, linear motors generate straight-line motion directly. The quality of these laminations plays a critical role in controlling magnetic fields, reducing energy losses, and ensuring smooth, accurate motion.
In practical terms, a well-executed linear motor lamination provides a foundation for improved efficiency and stability. When each layer is meticulously produced and aligned, the resulting motor core can operate with reduced heat buildup, lower eddy current losses, and more consistent torque. These subtle yet impactful advantages help manufacturers achieve higher productivity without necessarily increasing resource consumption.
1.2 How Linear Motor Lamination Impacts Modern Manufacturing
Today’s manufacturing landscape is evolving rapidly, and linear motor lamination serves as a key element in meeting the industry’s growing demands. For one, employing higher-quality lamination can help minimize operational costs through improved energy efficiency. By ensuring that motors draw less power over time, companies can effectively reduce their environmental footprint while managing expenses more responsibly.
Moreover, precise lamination supports advanced automation trends. When production lines incorporate motors that deliver stable, uniform performance, it becomes easier to integrate sophisticated robotic systems, sensor-driven quality checks, and other modern technologies. Linear motor lamination thus aligns well with cutting-edge manufacturing processes and emerging applications that require pinpoint accuracy and repeatability.
1.3 Introducing the Top Three Transformative Reasons
In the following sections, we will explore three core reasons why selecting high-quality linear motor lamination can significantly enhance production outcomes. By delving deeper into energy efficiency, durability, and precision, we aim to provide a balanced understanding of how careful lamination choices can positively influence overall manufacturing performance. Ultimately, the goal is to help decision-makers better evaluate their motor solutions and consider adjustments that may improve their competitive edge.
2. Reason #1: Enhanced Energy Efficiency
2.1 Lowering Operational Energy Costs
One of the most notable benefits of investing in high-quality linear motor lamination is its potential to reduce operational energy costs over time. When laminations are produced and assembled with great care, the internal magnetic flux paths of the motor can flow more efficiently, leading to fewer eddy current losses and less wasted energy. As a result, the motor tends to operate at a more stable temperature and draw less current, helping manufacturers maintain or even improve output while lowering overall power consumption.
In many cases, incremental improvements in energy use may not seem dramatic at first glance. However, when aggregated across multiple units and extended over long production cycles, these energy savings can translate into meaningful cost reductions. The payoff may be gradual, yet its cumulative impact on the bottom line can be quite substantial.
2.2 Environmental and Sustainability Benefits
High-quality linear motor lamination can also serve as a subtle, yet valuable, contributor to a company’s sustainability initiatives. By utilizing less energy, linear motors inherently reduce carbon emissions associated with electricity generation. This aligns with growing expectations for responsible resource management in manufacturing and can help businesses meet environmental compliance targets. While it is not a sole solution for sustainability challenges, careful lamination choices represent a small but important step toward more eco-conscious production.
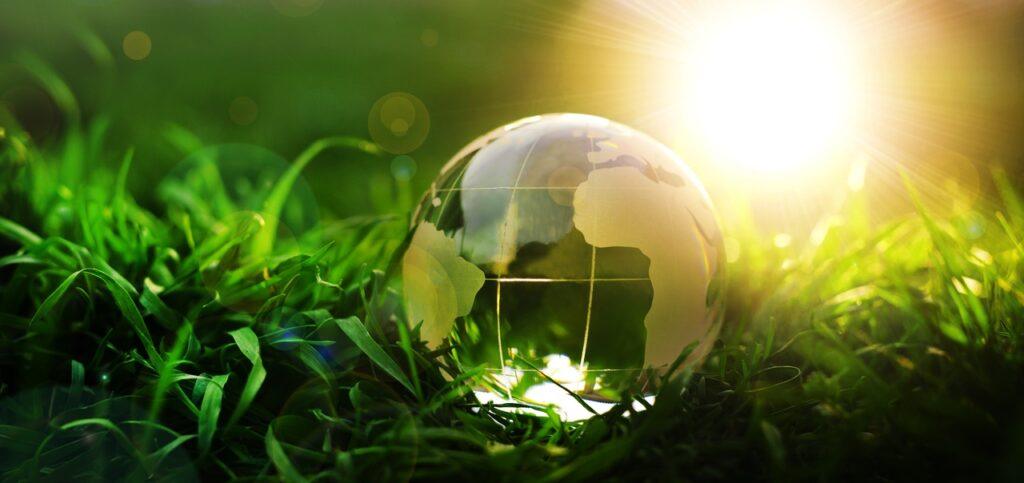
2.3 Real-World Efficiency Gains
In practice, efficiency gains often manifest as improved uptime, consistent performance, and greater operational predictability. For instance, a facility that integrates more efficient linear motor lamination into its equipment may notice smoother operation under variable loads, or less need for cooling systems and maintenance interventions. Although it is always wise to remain cautious in projecting outcomes, many companies find that investing in quality lamination can contribute positively to the performance of their systems over time, ultimately helping them better manage both energy usage and production costs.
3. Reason #2: Improved Durability and Reliability
3.1 Structural Integrity and Heat Management
A well-crafted linear motor lamination can significantly influence the structural integrity of a motor. By ensuring that each layer of electrical steel is cut, shaped, and stacked with precise alignment, manufacturers create a core that can withstand the mechanical stresses common in industrial environments. This attention to detail helps maintain stable performance, particularly under high loads or extended operational cycles.
In addition, careful lamination techniques contribute to more effective heat management. When layers are consistently arranged, the motor’s internal temperature can be better regulated, potentially reducing the risk of thermal distortion or excessive wear. Although it may not completely eliminate temperature challenges, achieving more uniform heat dissipation can help prolong equipment life and lower maintenance requirements over time.
3.2 Reducing Vibrations and Noise
Beyond structural benefits, high-quality linear motor lamination can help mitigate vibrations and noise during operation. Slight inconsistencies in lamination thickness or alignment may cause minor imbalances that, over prolonged periods, contribute to unnecessary resonance within the motor. By maintaining tighter tolerances, it becomes possible to achieve a steadier operational state, which in turn can lead to a quieter work environment.
While no motor runs entirely free of noise or vibration, improved lamination design and assembly can keep these factors within manageable limits. This can be advantageous for facilities seeking to comply with occupational safety standards or aiming to provide a more comfortable atmosphere for technicians and operators.
3.3 Extending Motor Life and Minimizing Downtime
Durability and reliability are also closely tied to reducing the frequency of breakdowns and unexpected downtime. When a linear motor lamination is engineered for quality and consistency, the core structure is inherently more resistant to wear and tear. Over time, this improved resilience may extend the service life of the motor, potentially lowering total cost of ownership.
By investing in careful lamination procedures, companies may gain greater confidence in their equipment’s day-to-day performance. While no one factor guarantees absolute reliability, a strong lamination foundation can contribute meaningfully to long-term stability and operational predictability.
4. Reason #3: Superior Precision and Performance
4.1 Consistency in Magnetic Properties
A crucial aspect of achieving superior performance lies in maintaining consistent magnetic properties within the motor. High-quality linear motor lamination can help ensure that the magnetic flux remains evenly distributed along the entire motion path. By precisely controlling lamination thickness, material quality, and alignment, it becomes possible to achieve a more uniform magnetic field. Although no single measure guarantees absolute perfection, careful lamination practices set the groundwork for motors that deliver steady torque and smoother transitions between speed profiles. Such consistency plays a key role in processes where precision and repeatability are essential for meeting quality standards.
4.2 Enhanced Motion Control and Accuracy
The benefits of reliable linear motor lamination extend into more refined motion control. When each lamination layer works in harmony, the resulting motor experiences less interference from variables that can otherwise compromise accuracy. This may include more predictable positioning, minimal deviation from set points, and greater responsiveness to real-time control adjustments. While it is important to acknowledge that other factors—such as controller design, feedback systems, and application-specific conditions—also influence performance, improved lamination quality can serve as a valuable supporting element. Over time, enhanced motion accuracy can help reduce defects, optimize cycle times, and support the integration of advanced automation tools.
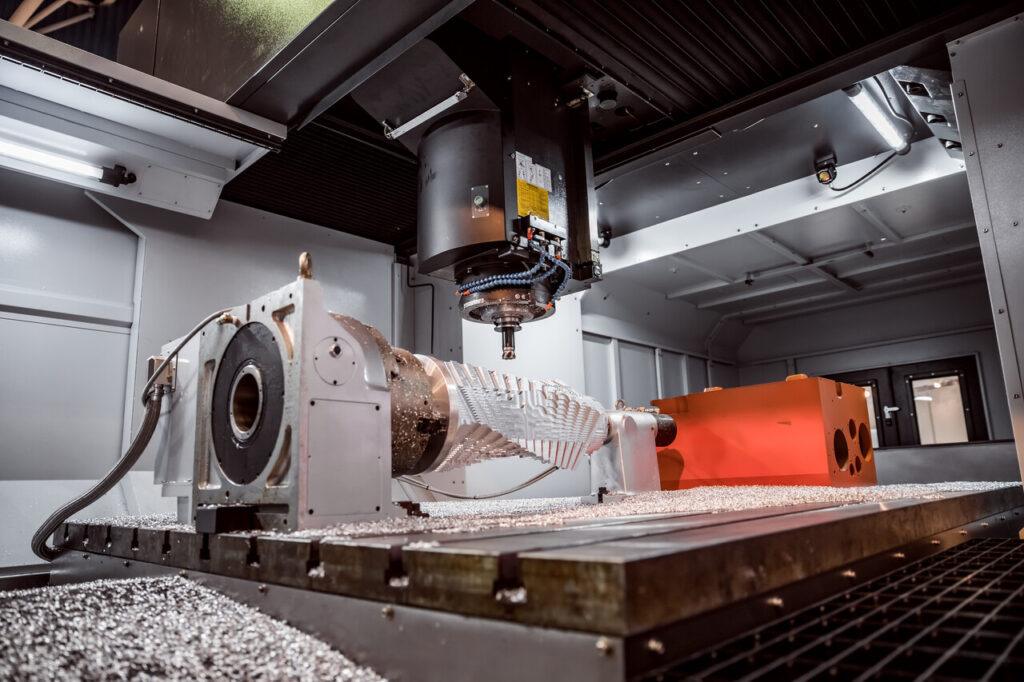
4.3 Impact on Overall Production Throughput
Better precision ultimately has the potential to influence overall production throughput. With improved linear motor lamination, manufacturers may realize steadier, more consistent operation that contributes to faster product cycles and fewer errors. Although outcomes vary based on individual use cases, many facilities find that incremental gains in quality and control can lead to a more efficient workflow. By helping motors work closer to their ideal parameters, strategic lamination choices offer a subtle but meaningful edge. While it may not solve every production challenge, investing in higher lamination quality stands as a prudent approach for those aiming to support long-term stability and capability within their processes.
5. Selecting the Right Linear Motor Lamination Supplier
5.1 Quality Standards and Certifications
When seeking a supplier for linear motor lamination, it can be worthwhile to verify their adherence to recognized quality standards. Certifications such as ISO ensure consistent production practices, reliable material sourcing, and adherence to stringent performance benchmarks. While no certification guarantees flawless results, it does provide reassurance that the supplier operates under a structured framework aimed at maintaining quality over time. Reviewing audit reports and testing methodologies can further confirm that their lamination processes align with your own operational goals.
5.2 Customization and Engineering Support
Another factor to consider involves the supplier’s willingness and ability to accommodate specific project requirements. Some linear motor lamination needs may call for unique geometries, tighter tolerances, or specialized alloys. A supplier equipped to offer tailored engineering support and collaborative design services can help address these details. Although it may require more up-front planning, working closely with an experienced partner can result in laminations that support more efficient and stable motor performance in the long run.
5.3 Advanced Manufacturing Capabilities
Modern production methods have evolved significantly, and suppliers who stay current with technology trends often bring added value. For instance, employing laser cutting or state-of-the-art stamping techniques can yield more precise laminations and reduce waste. While innovation does not automatically guarantee superior results, it does suggest that the supplier is invested in advancing their manufacturing capabilities. Staying informed about their equipment, software, and quality control systems can offer insights into their commitment to meeting complex specifications.
5.4 Long-Term Partnerships and After-Sales Service
Building a relationship with a reliable linear motor lamination supplier goes beyond initial product delivery. Consider how they handle after-sales support, such as assisting with potential adjustments, offering replacement parts, or providing ongoing consultation. Establishing a long-term partnership can enhance supply chain stability, improve response times, and ultimately encourage more consistent production outcomes. Although no single metric ensures the perfect supplier match, carefully evaluating these factors can guide decision-makers toward a provider capable of supporting sustainable, high-quality manufacturing.
Further Reading about Linear Motor Knowledge:
https://ieeexplore.ieee.org/document/8433682