1. Understanding Drone Core Lamination
1.1 What is Drone Core Lamination?
a. Defining Core Lamination and Its Purpose in Drone Motors
Drone core lamination refers to the process of creating thin, stacked metal sheets—usually high-grade electrical steels—inside the motor’s stator. These laminated sheets form the foundational structure that helps guide magnetic flux efficiently. Rather than using a single solid piece of metal, lamination involves layering multiple thin sheets, each separated by a non-conductive coating. This design helps limit eddy currents and reduce heat buildup, ultimately contributing to more stable and consistent drone flight performance.
b. Key Materials and Properties of Laminations
High-quality materials are critical in drone core lamination. Typically, non-oriented silicon steel is chosen for its superior magnetic properties and dimensional stability. Its permeability and reduced electrical conductivity help maintain optimal magnetic flux densities, minimizing energy losses. These specialized steels are also carefully coated to ensure effective insulation and corrosion resistance, so the laminations remain dependable over time.
c. How Lamination Reduces Energy Losses
By employing thin laminations, drones benefit from lower eddy current losses. Each layer interrupts the flow of stray currents, reducing heat production and preventing unnecessary energy dissipation. In turn, the motor operates more efficiently, enabling longer flight durations and preserving valuable battery life.
1.2 Importance of High-Quality Lamination
a. Impact on Motor Efficiency and Flight Stability
Carefully executed drone core lamination positively influences overall motor efficiency, which can lead to more stable and reliable drone operations. Drones equipped with well-laminated cores often exhibit smoother rotational performance and improved responsiveness.
b. Reduced Eddy Current Losses for Longer Battery Life
Since lamination lowers energy losses, drones can maintain flight for more extended periods without draining the battery prematurely. This improved energy utilization allows for more mission flexibility.
c. Enhancing Overall Drone Performance and Durability
Investing in high-quality drone core lamination can support better heat management, reduce maintenance needs, and promote long-term operational durability—ultimately ensuring that drones meet their performance requirements and remain competitive in a fast-evolving market.
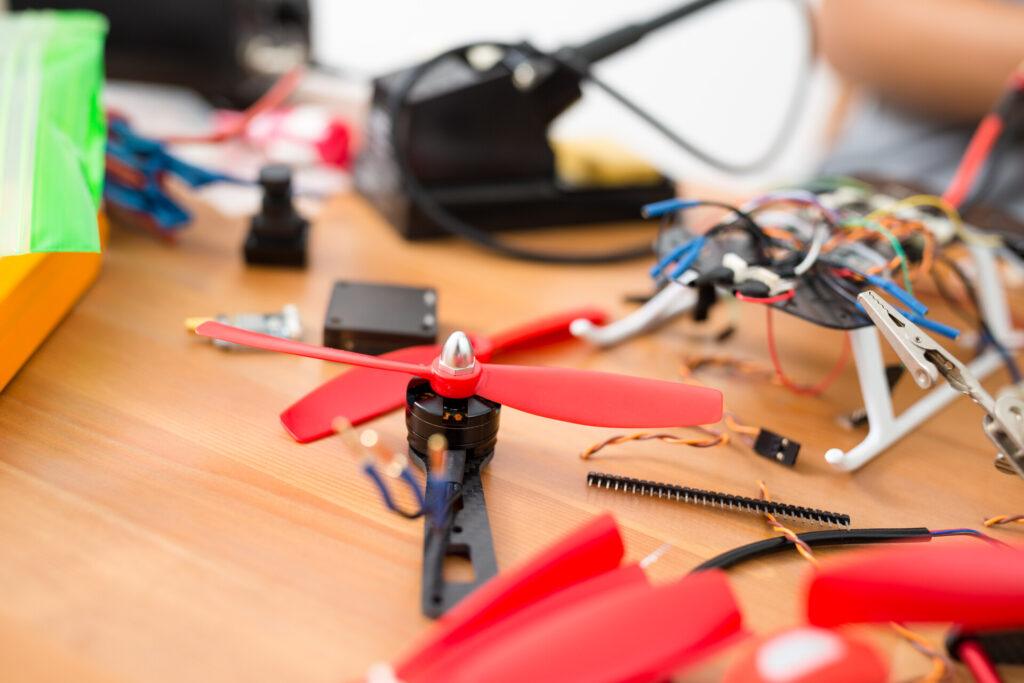
2. The Science Behind Motor Efficiency
2.1 Magnetic Principles in Core Lamination
a. Role of Lamination in Controlling Magnetic Flux
Understanding the role of drone core lamination involves recognizing how these thin, layered sheets influence magnetic flux distribution. When current flows through the motor’s coils, the laminated core guides and concentrates the magnetic field. By doing so, the motor can convert electrical energy into rotational force more effectively, supporting stable flight performance.
b. Minimizing Hysteresis for Optimized Energy Usage
Hysteresis losses occur when the magnetic field within a material lags behind changes in the external magnetic field. In well-executed drone core lamination, high-quality steel materials are selected to minimize these losses. Although no material is entirely immune, choosing metals with lower hysteresis characteristics can support improved motor efficiency over time. This results in drones operating closer to their intended performance levels, with more efficient energy consumption.
c. Balancing Cost and Performance with Proper Materials
It is prudent for manufacturers to balance material costs with the operational demands of a drone. By carefully evaluating various steel grades and lamination techniques, they can select options that deliver sufficient magnetic performance without excessively inflating production costs. This conservative approach can maintain reliable flight characteristics while managing expenses.
2.2 Quality Standards and Testing
a. Industry Benchmarks and Certifications
Industry standards exist to ensure drone core lamination meets consistent quality benchmarks. Adhering to widely recognized certifications and guidelines can help reassure stakeholders that the laminations were developed and tested using established best practices.
b. Non-Destructive Testing Methods for Lamination Stacks
Non-destructive testing methods, such as ultrasonic or eddy current inspections, can provide valuable insights into lamination integrity without harming the product. These techniques allow manufacturers to detect potential weaknesses or defects early.
c. Ensuring Consistency Through Quality Assurance Protocols
By implementing rigorous quality assurance protocols, manufacturers can help ensure that each lamination stack performs reliably. This measured approach reduces performance variability and contributes to steady improvements in the overall efficiency and longevity of drone motors.
3. Introducing the 5 Ultimate Techniques
3.1 Technique 1: Precision Stamping and Laser Cutting
One effective approach in drone core lamination involves the use of precision stamping and advanced laser cutting. By ensuring each lamination layer is formed with careful accuracy, it may help maintain tighter tolerances and more uniform magnetic fields. While not an absolute guarantee, these refined fabrication methods could contribute to improved motor consistency and operational stability.
3.2 Technique 2: Progressive Die Lamination Stacking
Progressive die lamination stacking allows for continuous, automated production of lamination sheets, potentially lowering unit costs without greatly impacting quality. With a measured application of this method, drone core lamination projects can gain greater efficiency and consistency. Over time, such an approach can facilitate stable manufacturing volumes and help maintain reliable product performance standards.
3.3 Technique 3: High-Grade Silicon Steel Selection
Selecting the right grade of silicon steel is crucial for optimizing the magnetic properties of a drone motor’s core. While not all drone applications demand the highest-end materials, choosing suitably refined steel can reduce energy losses and minimize hysteresis. By carefully weighing cost against potential gains, manufacturers can better ensure their lamination stacks meet targeted performance goals.
3.4 Technique 4: Advanced Bonding and Welding Methods
Refined bonding and welding techniques, including laser welding and adhesive bonding, may improve the structural integrity of the lamination stack. Proper application of these methods can lower vibration and noise, potentially prolonging the motor’s lifespan. Although results can vary, maintaining appropriate bonding standards might lead to improved reliability over the long term.
3.5 Technique 5: Precision Heat Treatment and Coatings
Controlled heat treatments and specialized coatings can further enhance the durability and magnetic characteristics of drone core lamination. Properly treated laminations are less prone to corrosion and can maintain stable performance under varying operational conditions. Although it’s impossible to eliminate all wear and tear, thoughtful heat treatment and protective coatings may support more consistent motor efficiency.
4. Implementing Core Lamination Techniques in Your Supply Chain
4.1 Collaborating with Reputable Manufacturers
When considering drone core lamination solutions, selecting a manufacturing partner with an established track record may contribute to a more reliable supply chain. Rather than relying solely on claims, it might be wise to review references, certifications, and documented quality assurance measures. Manufacturers who adhere to recognized industry standards can help ensure that their materials and lamination processes meet expected requirements. Although this does not guarantee flawless performance in every situation, partnering with experienced suppliers can reduce variability and support more consistent outcomes.
4.2 Cost-Benefit Analysis for Drone Manufacturers
Balancing cost and quality is an important consideration. While investing in advanced drone core lamination techniques and materials might present a higher initial expense, it may lead to improved motor efficiency and longevity. Over the long term, these enhancements could translate into reduced maintenance costs, better operational stability, and potentially fewer product returns. It may be helpful to evaluate total lifecycle value rather than focusing solely on upfront spending. Although results can vary, many companies find that a modest increase in manufacturing costs can yield a noticeable benefit in drone performance, contributing to a more favorable reputation in the marketplace.
4.3 Compliance and Sustainability
Incorporating drone core lamination into a supply chain also involves attention to regulatory compliance and environmental considerations. Sourcing laminations that meet relevant standards and implementing sustainable production methods could assist in fostering a responsible corporate image. Ensuring proper disposal or recycling of materials and using steels produced under environmentally conscious guidelines may help mitigate long-term liabilities. While there are no absolute guarantees of improved brand perception, manufacturers often find that demonstrating compliance and a commitment to sustainability resonates positively with customers and industry observers. Over time, these measured steps toward responsible sourcing and production can help create a more enduring and credible market presence.
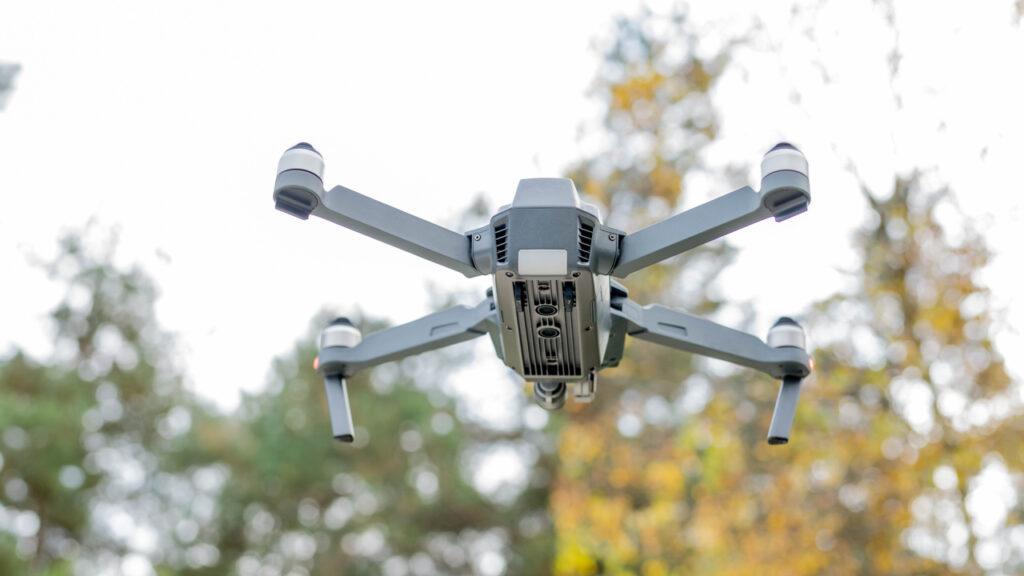
5. Real-World Success Stories and Case Studies
5.1 Racing Drones Pushing the Limits
In competitive racing scenarios, even minor improvements in efficiency and stability can influence outcomes. While no single factor guarantees victory, some teams have benefited from careful attention to drone core lamination. By utilizing high-quality materials and refined production methods, it appears possible to reduce energy losses and support more stable flight characteristics, potentially giving pilots a subtle edge. Although results may vary between different drone designs and racing conditions, investing in well-implemented lamination techniques might help maintain smooth motor performance, contributing to consistent lap times and less strain on power sources.
5.2 Commercial Delivery Drones
Commercial delivery drones, which often operate under tight schedules and frequently changing weather conditions, have reportedly shown signs of improved durability and flight efficiency through selective use of drone core lamination techniques. While there are many factors that influence a drone’s reliability, some logistics companies have noted that motors incorporating well-crafted lamination stacks seem to deliver steady thrust over longer periods. This may enable more precise route planning and reduced maintenance intervals. Although direct causation can be difficult to establish, the outcome is often a more predictable, cost-effective delivery process, potentially leading to better customer satisfaction.
6. Conclusion: Elevating Drone Performance Through Quality Lamination
6.1 Summarizing the 5 Techniques
A careful approach to Drone Core lamination may help optimize motor performance without making overly ambitious claims. The five techniques discussed—precision stamping and laser cutting, progressive die lamination stacking, high-grade silicon steel selection, advanced bonding and welding methods, and precision heat treatment with protective coatings—collectively represent strategies that could incrementally improve drone motor efficiency. Each technique, thoughtfully implemented, might contribute to more stable flight, reduced energy losses, and a potentially longer operational lifespan.
6.2 Emphasizing the Importance of Investing in Quality
While Drone Core lamination is not a standalone solution that guarantees peak performance, it is a foundational aspect worth serious consideration. By evaluating each method’s benefits and aligning them with specific operational requirements, drone manufacturers and operators can make informed decisions that may deliver incremental improvements over time. This measured approach acknowledges that outcomes vary depending on factors such as materials, manufacturing precision, and operational conditions.
Opting for high-quality lamination does not have to be cost-prohibitive. Although premium materials or advanced production methods might initially seem more expensive, a longer-term view suggests that such investments could help reduce maintenance costs, minimize downtime, and support more consistent performance. This balanced perspective may foster more sustainable business operations and gradually build trust among customers, regulators, and industry peers.
Ultimately, focusing on careful Drone Core lamination can serve as one of several prudent steps toward enhancing drone performance. While it may not be the sole determinant of success, attention to lamination quality can encourage more reliable results, allowing drone systems to better meet the demands placed upon them. As manufacturers and users continue to refine their understanding of these techniques, the industry may discover evolving best practices that steadily advance the standard of drone efficiency and competitiveness.
7. Additional Resources and Next Steps
7.1 Technical Whitepapers and Research Materials
Those interested in pursuing a deeper understanding of Drone Core lamination might consider reviewing technical whitepapers or relevant industry research. While some documents offer limited insights, carefully selected publications, conference proceedings, and academic journal articles can provide useful information. Such resources may help readers evaluate different steel grades, lamination techniques, and test methods. By doing so, it becomes possible to form a more comprehensive view of how lamination quality can influence motor efficiency.
7.2 Trusted Manufacturer Directories and Guides
In addition to scholarly sources, it may be worthwhile to consult reputable manufacturer directories and buying guides. These lists can offer insights into producers who have experience with Drone Core lamination. While a listing does not guarantee superior quality or precise adherence to best practices, examining a range of reputable suppliers allows potential buyers to compare products, services, and quality control standards. Some directories also include feedback from past clients, providing additional reassurance that can help support more informed decision-making.
7.3 Contacting Experts for Tailored Lamination Solutions
For those with specific requirements or unique project constraints, reaching out to experts may be a practical step. Engaging with engineers, consultants, or technical sales representatives who specialize in Drone Core lamination could clarify uncertainties and highlight tailored solutions. Although individual consultations do not promise guaranteed improvements, they can assist in aligning lamination strategies with particular operational goals.
7.4 Looking Ahead: Ongoing Refinements and Industry Developments
As drone technology continues to evolve, so too may the techniques and materials associated with Drone Core lamination. Staying informed about emerging industry trends, regulatory changes, and new fabrication methods can help maintain a balanced perspective. By periodically reviewing updated research, assessing feedback from trusted manufacturers, and consulting with knowledgeable professionals, stakeholders may identify incremental steps toward enhancing motor reliability and sustaining competitive performance in a rapidly changing marketplace.
Further Readings and Sources: