Discover DC motor core and how avoiding common pitfalls in material selection, lamination stacking, insulation, and quality control can significantly improve efficiency. Learn practical steps and best practices to enhance efficiency, reliability, and product longevity.
1. Introduction to DC Motor Cores
1.1 Understanding the Role of the DC Motor Core
a. Overview of DC motor operation
In a typical direct current (DC) motor, electrical energy is converted into mechanical rotation through the interaction of magnetic fields and current-carrying conductors. The DC motor core sits at the heart of this process. It provides the magnetic circuit path, helping guide magnetic flux efficiently around the motor’s internal structure. While other components, such as windings, brushes, and commutators, play essential roles, the DC motor core establishes a solid foundation for reliable performance.
b. Importance of lamination stacks
Modern DC motor cores typically consist of carefully stacked, thin steel laminations. These layers are designed to reduce eddy currents and associated losses that can lead to unwanted heat generation. By minimizing energy dissipation, well-constructed lamination stacks help maintain stable torque outputs and contribute to the motor’s overall longevity. Choosing quality laminations for the DC motor core is not merely a preference; it is widely regarded as a crucial step toward achieving consistent efficiency.
c. Core quality and overall motor efficiency
Even small deviations in the core’s composition, geometry, or lamination integrity can influence the entire motor’s performance. A high-quality DC motor core supports optimal magnetic flux distribution, thereby improving torque, reducing vibrations, and maintaining stable speed. While perfection may be challenging, maintaining close adherence to established standards and best practices can result in more reliable and predictable motor behavior.
1.2 Defining Core Quality Standards
a. Material selection criteria
When determining suitable materials for a DC motor core, engineers often consider factors like magnetic permeability, conductivity, and mechanical durability. Silicon steel, for example, is commonly chosen due to its favorable properties and proven track record.
b. Manufacturing tolerances and precision
Consistency in lamination thickness, smooth edges, and accurate punching tolerances helps ensure uniform magnetic properties. Careful attention to dimensional control minimizes losses and preserves the intended motor characteristics.
c. Industry benchmarks and certifications
Recognized quality standards, supported by certifications and independent testing, guide manufacturers and end-users toward improved DC motor core reliability. Meeting these benchmarks is not a guarantee of success, but it provides valuable reassurance that established best practices have been followed.
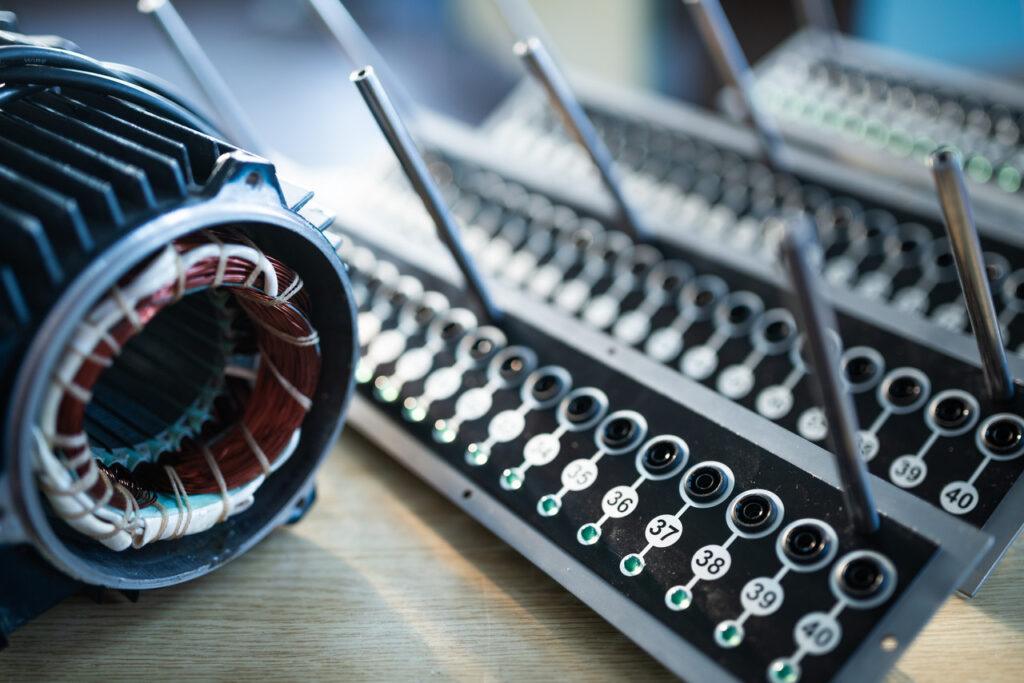
2. Disappointing Mistake #1: Using Substandard Lamination Materials
2.1 Impact of Low-Quality Steel on Performance
a. Increased Magnetic Losses
When manufacturers opt for lower-grade steel in their DC motor core construction, the result can be an overall rise in magnetic losses. Inferior materials tend to have higher levels of impurities and inconsistent grain structures, which cause excess eddy currents and hysteresis. This, in turn, leads to heat buildup and energy waste. Although not always immediately evident, these incremental losses gradually diminish the motor’s efficiency and reliability.
b. Reduced Torque and Output Power
Substandard lamination materials may fail to deliver the magnetic permeability required for efficient flux distribution. As a result, the DC motor core may not achieve the intended torque output, causing a dip in overall motor performance. While some motors may still function, the subtle drop in power and responsiveness can affect long-term customer satisfaction, especially in demanding applications.
2.2 Identifying and Avoiding Inferior Materials
a. Supplier Vetting and Audits
Ensuring that chosen steel suppliers meet established quality standards is key to maintaining a dependable DC motor core. Before committing to a particular source, it may be prudent to conduct supplier audits, inspect their production processes, and verify adherence to industry benchmarks. Engaging in regular material testing can also help identify hidden defects early.
b. Specifying Correct Steel Grades
A deliberate approach to steel grade selection can prevent unwanted fluctuations in motor performance. Opting for high-quality silicon steel or other proven alloys can result in more stable magnetic properties. Moreover, working closely with material experts allows for better-informed decisions about thickness, coating, and composition tailored to the specific requirements of a given DC motor core design.
2.3 Long-Term Consequences
a. Decreased Product Lifespan
Over time, the use of substandard laminations can significantly shorten the motor’s operational life. This could mean more frequent servicing, repairs, or replacements—factors that ultimately raise costs and inconvenience end-users.
b. Damaged Brand Reputation
Repeated reliability issues traced back to poor lamination quality can erode a company’s credibility. Investing in high-grade materials for each DC motor core helps maintain a consistent track record and preserves the brand’s long-term market position.
3. Disappointing Mistake #2: Poor Lamination Stacking Techniques
3.1 The Importance of Precision Stacking
a. Even Stacking vs. Misalignment
Precision in lamination stacking is integral to the overall functionality of the DC motor core. When laminations are arranged evenly, the magnetic flux follows a well-defined path, ensuring stable torque and smoother operation. By contrast, even slight misalignment between laminations can create distortions in the magnetic field. This may not immediately halt the motor, but it can gradually reduce its efficiency and consistency over time.
b. Minimizing Air Gaps
Effective stacking also means minimizing any unintended air gaps between lamination layers. These gaps can significantly hinder magnetic permeability, leading to losses in power and reduced operational smoothness. While small discrepancies might seem negligible, collectively they can undermine the motor’s ability to reach its expected performance benchmarks.
3.2 Common Errors in Assembly
a. Using Outdated Tools and Machinery
When assembly processes rely on outdated tools, manual methods, or poorly maintained machinery, inconsistencies in the lamination stack can easily occur. Slight deviations in thickness or alignment can contribute to an underperforming DC motor core, ultimately affecting the product’s perceived quality and durability.
b. Improper Handling and Storage of Laminations
Lamination materials are often delicate, and rough handling during transit, storage, or pre-assembly stages can lead to warping or contamination. When these flawed laminations are subsequently stacked, the motor core may fail to achieve its intended magnetic properties. Conservative handling and careful inventory management are thus crucial to ensure reliable stacking results.
3.3 Implementing Best Practices
a. Automated Stacking Solutions
Modern manufacturing equipment can provide greater precision and consistency in lamination stacking. Automation helps ensure that each layer is placed accurately, reducing the risk of human error.
b. Quality Control Checks Throughout Assembly
Regular inspection points, from initial stacking trials to final assembly checks, help catch deviations early. By identifying issues before they escalate, manufacturers can maintain a more stable, reliable DC motor core, leading to motors that better meet customer expectations over the long run.
4. Disappointing Mistake #3: Inadequate Insulation and Coatings
4.1 Significance of Insulation Layers
a. Preventing Inter-Laminar Currents
Insulation layers play a critical role in preserving the integrity of the DC motor core. By acting as a barrier between individual steel laminations, proper insulation reduces the chance of inter-laminar currents—small, unwanted electrical flows that can generate excess heat. Although these currents might not lead to immediate failure, the resulting energy loss can gradually undermine motor efficiency and stability.
b. Enhancing Safety and Longevity
A well-insulated DC motor core is often more resilient under demanding conditions. Appropriate coatings protect the laminations from short circuits and other electrical hazards, helping maintain consistent motor performance over time. While no single method can guarantee absolute immunity from all potential issues, adhering to recognized insulation standards is often considered a prudent step toward improving motor longevity.
4.2 Common Failures in Insulation
a. Using Low-Grade Insulation Coatings
Coatings that peel, crack, or fail prematurely may render the motor vulnerable to internal electrical faults. Selecting subpar insulation materials—or applying them in a hasty manner—can contribute to unwanted gaps in the motor’s protective layers. Although cost-saving measures may seem tempting, they can lead to complications that outweigh any initial financial benefit.
b. Improper Application Thickness
Applying insulation that is too thin may not provide sufficient protection, while overly thick layers can restrict lamination stacking density. Achieving the right balance, guided by industry standards, is considered an essential step in maximizing the DC motor core’s magnetic efficiency and mechanical stability.
4.3 Best Practices for Optimal Coating
a. Choosing the Right Insulation Material
Selecting a coating material suited to the motor’s operating conditions can help ensure effective insulation. Although no single material is universally perfect, careful evaluation of temperature, voltage, and environmental demands can guide a better-informed choice.
b. Strict Adherence to Application Standards
Consistently following recommended curing times, application methods, and quality checks can support a more durable DC motor core design. Over time, adherence to these practices may lead to improved customer satisfaction and a stronger reputation for long-term reliability.
5. Disappointing Mistake #4: Neglecting Rigorous Quality Control and Testing
5.1 The Need for Ongoing Quality Assurance
a. Early Defect Detection
A consistent, well-structured testing regimen helps identify underlying issues with the DC motor core at early stages of production. Without routine checks, hidden defects—such as uneven lamination thickness, suboptimal insulation layers, or slight misalignments—might remain undetected. Even small deviations, if not addressed, can gradually erode the motor’s reliability and efficiency.
b. Building a Culture of Continuous Improvement
Some manufacturers may forgo rigorous quality control measures in an effort to reduce costs or streamline production. While understandable, this approach can be short-sighted. Implementing robust inspection protocols encourages a culture centered on continuous improvement. Rather than solely reacting to problems, a proactive stance can help ensure that the final product meets both the manufacturer’s and the end-user’s expectations.
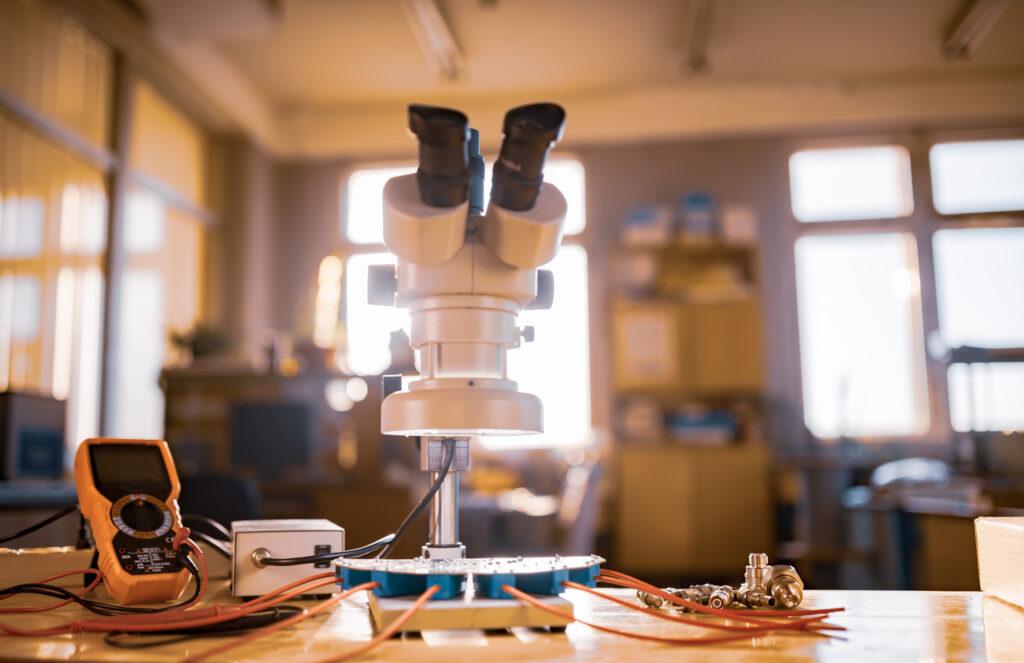
5.2 Common Oversights in Quality Control
a. Skipping Non-Destructive Testing
Non-destructive testing methods—such as magnetic flux measurements, electrical conductivity checks, and visual inspections—provide valuable insights without risking damage to the DC motor core. Ignoring these assessments may mean that subtle weaknesses remain hidden until the motor is already in service, potentially affecting long-term performance.
b. Limited Sample-Based Testing
Relying solely on selective sampling can create blind spots. While random checks are sometimes necessary, they may not always represent the full spectrum of products. A more comprehensive testing strategy, covering a larger portion of production, can yield a clearer picture of overall quality.
5.3 Strategies for Enhanced Testing
a. Implementing Advanced Measurement Tools
Advanced inspection equipment, ranging from laser measurement devices to precision coordinate measuring machines, offers better detection capabilities. These technologies help ensure that each DC motor core meets the intended specifications and quality standards.
b. Leveraging Data and Analytics
Adopting data-driven methods—such as statistical process control—allows manufacturers to identify trends and prevent recurring issues. While no method can promise absolute perfection, taking a measured, systematic approach generally leads to more consistent and reliable core quality.
6. How to Choose a Reliable DC Motor Core Partner
6.1 Evaluating Supplier Capabilities
a. Technical Expertise and Experience
Selecting the right partner for producing a DC motor core typically begins with evaluating the supplier’s technical background. A reputable provider often demonstrates a history of consistent performance and understanding of relevant industry standards. While experience does not guarantee flawless outcomes, it does suggest a familiarity with the materials, processes, and potential challenges involved.
b. Comprehensive Material Sourcing and Testing
A competent supplier should have a transparent approach to material sourcing. This might mean working with established steel mills known for their quality, as well as conducting periodic audits and inspections. The ability to verify each step of the supply chain can help ensure that the DC motor core benefits from high-grade materials and uniform production conditions.
6.2 Customization and Engineering Support
a. Tailored Solutions to Specific Motor Designs
Each motor project has unique requirements, whether it involves speed, torque, energy efficiency, or operational conditions. Opting for a supplier who can customize the DC motor core design—fine-tuning lamination thickness, insulation coatings, or stacking techniques—may lead to improved outcomes. While no single solution fits all applications, engineering support can help bridge the gap between initial specifications and practical results.
b. Collaborative Product Development
A productive relationship often involves open communication and iterative development. Engaging in dialogue with a supplier’s engineering team, sharing detailed performance goals, and reviewing prototypes can foster mutual understanding. Although perfection is rarely guaranteed, a collaborative approach generally increases the likelihood of achieving targeted motor characteristics.
6.3 Cost and Sustainability Considerations
a. Balancing Price, Quality, and Performance
Simply choosing the lowest-cost option does not always yield long-term value. Considering the entire lifecycle of the DC motor core—from initial build quality to eventual maintenance costs—can offer a more balanced perspective.
b. Environmental Responsibility and Compliance
In today’s market, an environmentally conscious supplier can be an asset. Confirming that the partner follows relevant environmental guidelines and waste-reduction initiatives may help ensure that your DC motor core aligns with broader organizational sustainability goals.
7. Conclusion and Next Steps
7.1 Recap of the Four Major Mistakes
Reflecting on the key points outlined in previous sections, four common pitfalls often stand in the way of maximizing DC motor core quality. First, using substandard lamination materials introduces inefficiencies and reduces motor longevity. Second, poor stacking techniques can create subtle misalignments that lead to uneven magnetic flux distribution. Third, inadequate insulation and coatings can accelerate wear and reduce safety margins. Finally, neglecting rigorous quality control and testing exposes the motor core to hidden faults that may emerge later in the motor’s operational life.
7.2 The Path to Excellence in DC Motor Core Production
Striving for improvement in these areas does not require an unattainable level of perfection. Instead, focusing on incremental, well-informed changes can have a meaningful impact. Investing in higher-grade materials, adopting precision stacking methods, and applying reliable insulation can help maintain stable performance. Furthermore, implementing thorough quality assurance measures—such as regular testing, data-driven decision-making, and continual staff training—can facilitate early detection of potential issues, thereby supporting more consistent product reliability. Although challenges inevitably arise, conscious efforts to follow established best practices often lead to more predictable and satisfactory outcomes.
7.3 Inspiring Confidence in Customers and End-Users
Ultimately, attention to detail in the DC motor core design and manufacturing process reflects directly on the final product’s reputation. By openly communicating quality standards, demonstrating adherence to recognized benchmarks, and responding promptly to customer feedback, manufacturers can inspire greater confidence among both clients and end-users. While absolute guarantees are rare in engineering, a measured, thoughtful approach to continuous improvement reduces the likelihood of future failures. As the market evolves, staying current with technological advancements and industry guidelines may help ensure that these vital components continue to meet the evolving needs of various applications, benefiting everyone involved in the supply chain.
Further Reading About DC motors:
https://www.electrical4u.com/dc-motor-drives/