Explore the differences between linear and rotary actuators in humanoid robotics, understanding their roles in transforming robot movement, efficiency, and responsiveness.
1. Introduction
In the rapidly advancing field of robotics, actuators are the fundamental components that bring robots to life, enabling movement and interaction with the environment. As artificial intelligence (AI) continues to evolve, there is an increasing demand for humanoid robots that can perform complex tasks with agility and precision. The type of actuators used—whether linear or rotary—plays a critical role in determining the efficiency, responsiveness, and overall capability of these robots.
1.1. The Role of Actuators in Robotics
a. Importance in Humanoid Robots in the Age of AI
In the age of AI, humanoid robots are expected not just to mimic human appearance but also to replicate human-like movements and behaviors. Actuators serve as the muscles of these robots, converting energy into mechanical motion. The choice between linear and rotary actuators affects the robot’s ability to perform tasks ranging from simple gestures to complex manipulations. High-performance actuators enable robots to navigate dynamic environments, interact safely with humans, and adapt to new challenges—all essential features for AI-driven applications like personal assistance, healthcare, and industrial automation.
b. Evolution of Actuator Technology
Actuator technology has evolved significantly over the years, driven by the need for more efficient, compact, and powerful motion control solutions. Early robots relied on basic mechanical systems with limited functionality. Advances in materials science, electronics, and control algorithms have led to the development of sophisticated actuators capable of precise movements and feedback control. Innovations such as electric linear actuators and improved rotary actuators have expanded the possibilities for robot design, allowing for more human-like dexterity and responsiveness. This evolution has been instrumental in pushing the boundaries of what humanoid robots can achieve, bridging the gap between mechanical engineering and intelligent automation.
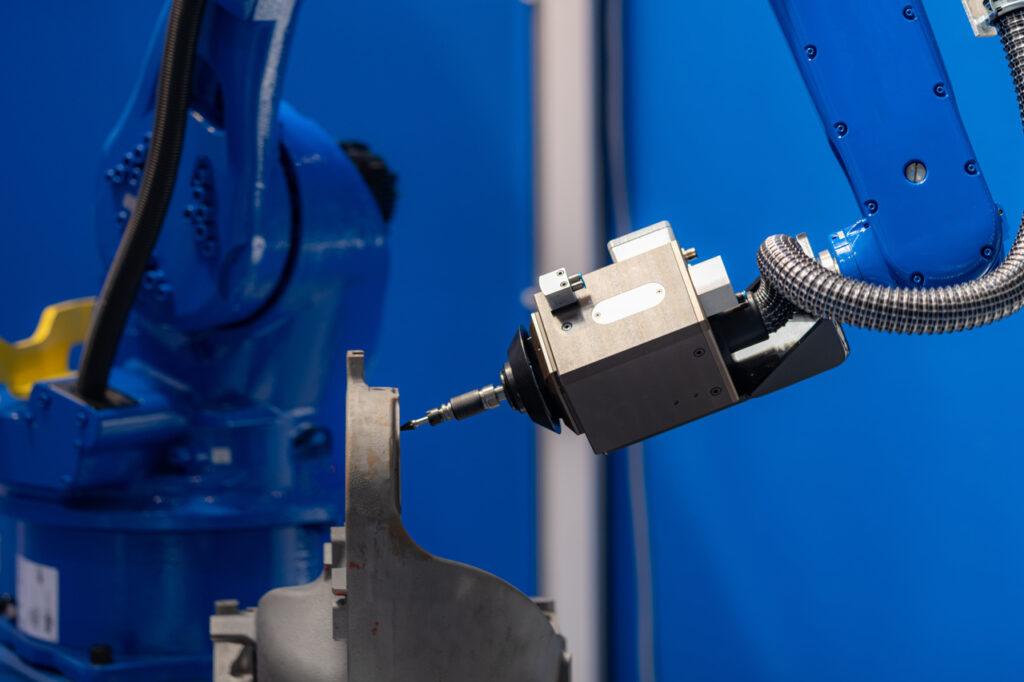
2. Understanding Rotary Actuators
2.1. Mechanism of Rotary Actuators
a. How They Work
Rotary actuators are devices that produce rotational motion, converting energy—typically electrical, hydraulic, or pneumatic—into torque to drive the rotation of a shaft. In robotics, they function much like muscles in the human body, enabling joints to move with precision and control. The core mechanism involves an input energy source causing a rotor to turn around its axis, which in turn moves the connected robotic components.
The operation begins when the actuator receives a control signal, prompting the motor to generate rotational force. This force is transmitted through gears or belts to achieve the desired speed and torque. Feedback systems, such as encoders or potentiometers, are often integrated to monitor the position and velocity, allowing for precise adjustments and synchronization with other robotic movements.
b. Common Types Used in Robotics
Several types of rotary actuators are prevalent in robotics:
- Electric Servo Motors: Widely used due to their accuracy and responsiveness. They offer excellent control over position, speed, and torque, making them ideal for applications requiring precise movements.
- Stepper Motors: Operate by dividing a full rotation into equal steps, allowing for controlled positioning without feedback systems. They’re cost-effective and simple but may lack the smooth motion of servo motors.
- Brushless DC Motors: Known for their high efficiency and longevity. They provide smooth rotational motion and are suitable for continuous or high-speed applications.
- Harmonic Drive Actuators: Utilize a strain wave gearing mechanism to achieve high torque in a compact size. They’re essential for joints requiring significant force within limited space.
2.2. Applications in Humanoid Robots
a. Joint Movements
In humanoid robots, rotary actuators are crucial for replicating the rotational movements of human joints. They enable the robot to perform actions such as rotating the shoulder, bending the elbow, or twisting the wrist. By precisely controlling the angle and speed of rotation, these actuators allow robots to execute complex tasks like lifting objects, gesturing, or manipulating tools with a high degree of accuracy.
b. Advantages and Limitations
Advantages:
- Precision and Control: Rotary actuators offer fine control over rotational movements, essential for tasks requiring exact positioning and smooth motion trajectories.
- Compactness: Many rotary actuators are designed to fit within the confined spaces of robotic joints, aiding in creating more human-like proportions in humanoid robots.
- Versatility: They can be powered by various energy sources and adapted for different torque and speed requirements, making them suitable for multiple applications.
Limitations:
- Mechanical Complexity: Achieving multi-axis movement may require complex assemblies of gears and linkages, which can increase mechanical wear and the need for maintenance.
- Energy Consumption: Continuous power may be needed to maintain certain positions, leading to higher energy usage compared to actuators that can hold positions without power.
- Limited Force Output: Compared to some linear actuators, rotary actuators might produce less force, potentially limiting their effectiveness in tasks requiring high torque unless supplemented with gear reductions.
In essence, rotary actuators are integral to the functional movement of humanoid robots, providing the rotational capabilities necessary for emulating human motion. Understanding their mechanics, applications, and inherent trade-offs is vital for engineers and designers aiming to optimize robotic performance in an ever-evolving technological landscape.
3. Exploring Linear Actuators
3.1. Mechanism of Linear Actuators
a. Operational Principles (Hydraulic and Electric)
Linear actuators are devices that convert energy into linear motion, providing straight-line movement essential for various robotic functions. The two primary types of linear actuators used in robotics are hydraulic and electric.
Hydraulic Linear Actuators operate using fluid pressure. They consist of a cylinder and a piston; when hydraulic fluid is pumped into the cylinder, it pushes the piston, creating linear motion. This type of actuator is known for delivering high force and is often used in applications requiring substantial power. The smooth and controlled movements are ideal for heavy-duty tasks, but the complexity of hydraulic systems can add weight and maintenance requirements to the robot.
Electric Linear Actuators use electric motors to drive a screw, belt, or gear mechanism that produces linear displacement. Common mechanisms include lead screws, ball screws, and rack and pinion systems. Electric actuators are favored for their precision, efficiency, and ease of integration with electronic control systems. They offer excellent control over speed, position, and force, making them suitable for applications where precise movements are critical.
b. Variants and Configurations
Linear actuators come in various configurations to meet specific needs:
- Lead Screw Actuators: Utilize a threaded screw and nut; as the screw rotates, the nut moves linearly along the screw’s axis. They are simple and cost-effective but may have higher friction and lower efficiency.
- Ball Screw Actuators: Similar to lead screws but incorporate ball bearings between the screw and nut to reduce friction, increasing efficiency and load capacity.
- Belt-Driven Actuators: Use a belt and pulley system to convert rotary motion into linear motion. They are ideal for applications requiring high speed over longer distances but may sacrifice some precision.
- Linear Motors: Produce direct linear motion without mechanical contact by using electromagnetic forces. They offer high speeds and acceleration with exceptional positioning accuracy.
- Telescopic Actuators: Feature multiple stages that extend or retract, allowing for a longer stroke in a compact form when retracted.
3.2. Applications in Humanoid Robots
a. Movement Efficiency
In humanoid robots, linear actuators are crucial for replicating human-like movements that require linear motion, such as extending limbs, bending knees, or opening and closing hands. By directly producing linear displacement, these actuators enhance movement efficiency by eliminating the need for complex mechanisms to convert rotational motion into linear motion. This leads to smoother and more natural movements, improving the robot’s ability to interact with its environment in a human-like manner.
b. Advantages and Limitations
Advantages:
- High Force Output: Linear actuators can deliver significant force directly along their axis, making them suitable for tasks that require strong pushing or pulling actions.
- Precision and Control: Electric linear actuators offer excellent control over position and speed, enabling precise and repeatable movements essential for delicate tasks.
- Space Utilization: They can be designed to fit into compact spaces within the robot’s structure, optimizing the overall design and allowing for more complex mechanisms in a smaller footprint.
- Self-Locking Capabilities: Some linear actuators can maintain their position without continuous power, enhancing energy efficiency and stability during stationary periods.
Limitations:
- Complexity and Weight: Hydraulic actuators, while powerful, add complexity and weight due to the need for pumps, fluid reservoirs, and additional components, which can affect the robot’s agility.
- Speed Limitations: Certain types of linear actuators may not achieve the high speeds possible with rotary actuators, potentially limiting the robot’s responsiveness in fast-paced applications.
- Cost: High-precision linear actuators, especially those with advanced features like feedback sensors, can be more expensive than standard rotary actuators.
- Maintenance Requirements: Hydraulic systems require regular maintenance to prevent leaks and ensure proper functioning, which can increase operational costs and downtime.
In conclusion, linear actuators are vital components in humanoid robotics, offering distinct advantages in terms of force application, precision, and efficient space utilization. Understanding their mechanisms and applications allows for better integration into robotic designs, enhancing performance while considering the inherent trade-offs.
4. Impact on Humanoid Robot Movement
4.1. Case Study: Tesla Optimus Robot
a. Use of Linear Actuators
Tesla’s Optimus robot represents a significant advancement in humanoid robotics through its innovative use of linear actuators. By integrating linear actuators into critical joints such as the knees, hips, and ankles, Optimus achieves a high degree of movement efficiency and strength. These actuators provide substantial force output and self-locking capabilities, allowing the robot to maintain positions without continuous power consumption. The strategic placement of linear actuators enhances the robot’s ability to perform tasks that require lifting and carrying heavy loads, showcasing the potential of this type of robot actuator in industrial and service applications.
Learn more about Tesla’s Optimus robot actuators
b. Performance Outcomes
The implementation of linear actuators in Optimus results in smoother and more natural movements that closely mimic human motion. The self-locking feature contributes to energy efficiency, enabling longer operational periods without the need for frequent recharging. Additionally, the powerful force output allows the robot to handle substantial weights, expanding its functionality in various environments. Overall, the use of linear actuators in Tesla’s Optimus has demonstrated improved performance outcomes in terms of strength, stability, and energy conservation, highlighting the impact of actuator selection on humanoid robot capabilities.
4.2. Other Notable Robots (Boston Dynamics)
a. Rotary Actuator Implementations
Boston Dynamics, known for its cutting-edge robotics, primarily utilizes rotary actuators in robots like Atlas. These rotary actuators are designed to deliver high torque and rapid response times, enabling the robots to perform dynamic movements such as running, jumping, and complex navigation over uneven terrain. The precision and speed afforded by rotary actuators make them ideal for applications requiring agility and quick reflexes, underscoring their effectiveness as a robot actuator choice for high-performance tasks.
b. Comparative Performance
When comparing the performance of robots like Tesla’s Optimus and Boston Dynamics’ Atlas, the type of robot actuator used plays a pivotal role. While Optimus leverages linear actuators for strength and energy efficiency, Atlas’s rotary actuators provide superior speed and agility. This difference illustrates how actuator selection influences a robot’s abilities: linear actuators enhance lifting and stability, whereas rotary actuators excel in dynamic movement and responsiveness. Both approaches have their advantages and limitations, but together they showcase the diverse possibilities in humanoid robot movement enabled by different actuator technologies.
5. Conclusion
5.1 Summary of Key Findings
The exploration of linear and rotary actuators has highlighted their profound influence on humanoid robot movement. Rotary actuators are celebrated for their precision and agility, making them indispensable for tasks requiring rapid rotational motion and dynamic responsiveness. They enable robots to perform complex joint movements with high degrees of freedom, closely mimicking human articulation.
Conversely, linear actuators offer significant advantages in terms of force output and energy efficiency. Their ability to provide direct linear motion with substantial force makes them ideal for applications involving lifting, pushing, or maintaining stable positions. The self-locking capabilities of certain linear actuators contribute to reduced energy consumption, as they can hold positions without continuous power.
The case studies of Tesla’s Optimus robot and Boston Dynamics’ creations illustrate how the choice of robot actuator impacts performance outcomes. Tesla’s use of linear actuators results in powerful, efficient movements suitable for industrial tasks, while Boston Dynamics’ reliance on rotary actuators enables agile and dynamic motion. The comparative analysis underscores that the optimal actuator selection depends on the specific functional requirements of the humanoid robot.
5.3 Final Thoughts
In conclusion, the choice and implementation of actuators are critical factors in the development of effective humanoid robots. Understanding the distinct advantages and limitations of linear and rotary actuators allows engineers to tailor robotic systems to specific applications. The evolution of robot actuator technology continues to push the boundaries of what humanoid robots can achieve, bringing us closer to a future where they seamlessly integrate into various aspects of daily life.
The ongoing advancements promise not only to enhance robot performance but also to contribute positively to society by taking on tasks that are dangerous, repetitive, or require precision beyond human capability. As we move forward, the synergy between actuator technology and intelligent control systems will be the cornerstone of the next generation of humanoid robots, transforming the way we live and work.