Explore how self bonding lamination is revolutionizing manufacturing by offering superior efficiency over traditional lamination methods. This comprehensive analysis highlights the benefits and considerations for manufacturers adopting self bonding lamination.
1. Introduction
1.1. Background of Lamination in Manufacturing
a. Importance of lamination in motors and transformers
Lamination is a critical process in the manufacturing of electric motors and transformers. It involves stacking thin sheets of electrical steel to form the core of these devices. This technique reduces energy losses caused by eddy currents, thereby improving efficiency. The quality of lamination directly impacts the performance, reliability, and lifespan of electrical equipment.
b. Evolution of lamination techniques over time
Over the years, lamination methods have evolved significantly. Traditional techniques like adhesive bonding, welding, and mechanical fastening have been the mainstay in the industry. However, as technology advances and the demand for more efficient manufacturing processes grows, new methods such as self bonding lamination have emerged, offering promising alternatives.
1.2. Purpose of the Comparative Analysis
a. Highlighting the need for efficient manufacturing methods
In an increasingly competitive market, manufacturers seek ways to enhance efficiency, reduce costs, and improve product quality. This comparative analysis aims to examine how self bonding lamination stands against traditional methods, highlighting its potential benefits for the industry.
b. Overview of what the article will cover
This article will explore traditional lamination methods, delve into the concept of self bonding lamination, and provide a detailed comparison between the two approaches. It will also discuss applications in modern industries, challenges, and considerations for manufacturers contemplating a transition.
2. Overview of Traditional Lamination Methods
2.1. Adhesive Bonding
a. Process description
Adhesive bonding involves applying a bonding agent between layers of electrical steel sheets to hold them together. The adhesives are usually thermosetting resins cured under heat and pressure to form a strong bond.
b. Advantages and disadvantages
Advantages:
- Provides good insulation between layers.
- Can be effective in reducing vibrations.
Disadvantages:
- Adds extra weight due to adhesive material.
- Curing time increases production cycle.
- Potential for delamination under thermal stress.
2.2. Welding Techniques
a. Types of welding used in lamination
Common welding methods include spot welding and laser welding. These techniques fuse the layers at specific points or along seams to create a solid core.
b. Pros and cons
Pros:
- Creates a strong mechanical bond.
- Suitable for high-volume production.
Cons:
- Localized heating can cause distortions.
- Welding spots may introduce electrical losses.
- Requires precise control to avoid damaging thin sheets.
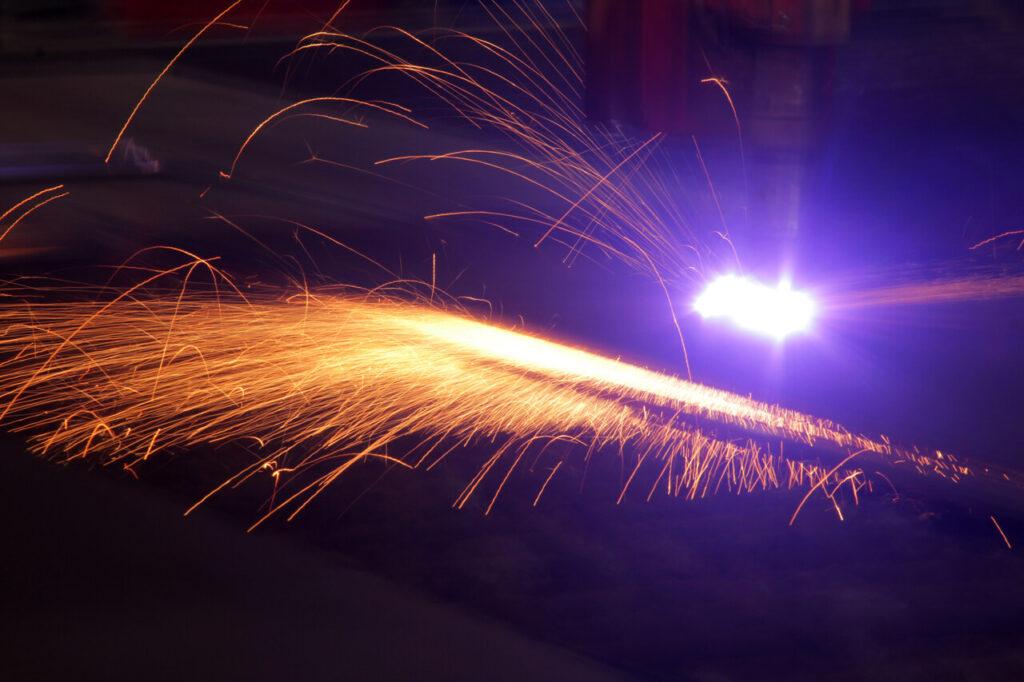
2.3. Mechanical Fastening
a. Methods like riveting and bolting
Mechanical fastening uses rivets, bolts, or clamps to hold the lamination layers together. This method relies on physical hardware rather than bonding agents or welding.
b. Benefits and limitations
Benefits:
- Simple and straightforward process.
- Easy to disassemble for maintenance.
Limitations:
- Adds weight and bulk to the assembly.
- Potential for loosening over time due to vibrations.
- Not ideal for high-speed applications where balance is critical.
3. Understanding Self Bonding Lamination
3.1. What is Self Bonding Electrical Steel?
a. Material composition
Self bonding electrical steel is a specialized material coated with a resin or insulating layer that activates under heat. The steel itself maintains high magnetic permeability and low core losses, essential for efficient electrical performance.
b. Self-bonding properties explained
When heated, the coating on the electrical steel sheets melts and bonds to adjacent layers without the need for additional adhesives. Upon cooling, it forms a solid, cohesive core with enhanced structural integrity.
3.2. The Self Bonding Process
a. How it works without adhesives or welding
The process involves stacking the coated steel sheets and applying heat (and sometimes pressure) to activate the bonding layer. This eliminates the need for separate adhesive application or welding operations, streamlining production.
b. Technological requirements
Manufacturers need equipment capable of precise temperature control to ensure proper bonding. The process may require ovens or induction heating systems designed for this specific application.
4. Comparative Analysis
4.1. Production Efficiency
a. Time savings with self bonding
Self bonding lamination reduces production steps by eliminating the need for adhesive application or welding setup. The bonding occurs during a single heat treatment, significantly cutting down manufacturing time.
b. Simplification of manufacturing processes
With fewer materials and steps involved, the process becomes more straightforward. This simplification reduces the likelihood of errors and improves overall workflow efficiency.
4.2. Cost Effectiveness
a. Reduction in labor and material costs
By removing the need for adhesives, welding consumables, and mechanical fasteners, material costs decrease. Labor costs are also reduced due to shorter production cycles and less complex procedures.
b. Long-term financial benefits for manufacturers
Over time, the savings in production costs and increased throughput can lead to a substantial return on investment. Manufacturers can allocate resources more effectively, enhancing profitability.
4.3. Performance and Reliability
a. Improved magnetic properties
Self bonding lamination maintains tight contact between layers, enhancing magnetic flux and reducing core losses. This results in better performance of motors and transformers.
b. Enhanced durability of final products
The uniform bonding minimizes vibrations and mechanical stress within the core, leading to longer-lasting equipment with fewer maintenance requirements.
4.4. Quality Control
a. Consistency in product output
The automated nature of the self bonding process ensures consistent results across production batches. This reliability is crucial for meeting stringent industry standards.
b. Reduction of defects and failures
Fewer production steps mean fewer opportunities for errors. The strong, uniform bond reduces the risk of delamination and mechanical failures in the field.
4.5. Environmental Impact
a. Less waste generation
Eliminating adhesives and welding consumables reduces waste materials. Additionally, the streamlined process consumes less energy, contributing to a smaller environmental footprint.
b. Energy savings during production
The self bonding process can be more energy-efficient than traditional methods, particularly when using advanced heating technologies. This efficiency aligns with global efforts to reduce industrial energy consumption.
5. Applications in Modern Industries
5.1. Electric Vehicle Manufacturing
a. Boosting motor efficiency
In electric vehicles (EVs), motor efficiency directly affects performance and range. Self bonding lamination enhances magnetic properties, leading to more efficient motors that maximize battery usage.
b. Meeting industry standards for sustainability
As the EV industry focuses on sustainability, adopting manufacturing processes like self bonding lamination supports environmental goals by reducing waste and energy consumption.
5.2. Renewable Energy Sector
a. Advancements in wind turbine generators
Wind turbines rely on efficient generators to convert kinetic energy into electricity. Self bonding lamination improves generator performance, increasing energy output from renewable sources.
b. Contribution to greener energy solutions
By enhancing the efficiency of renewable energy technologies, self bonding lamination plays a role in reducing reliance on fossil fuels and lowering greenhouse gas emissions.
6. Challenges and Considerations
6.1. Initial Implementation Costs
a. Investment in new materials and equipment
Transitioning to self bonding lamination requires purchasing specialized materials and possibly new equipment. This upfront investment can be significant.
b. ROI analysis
Manufacturers must conduct thorough return on investment analyses to determine the long-term financial benefits compared to the initial costs.
6.2. Technical Training
a. Need for workforce upskilling
Introducing new processes necessitates training employees. Staff must learn how to handle self bonding materials and operate new equipment effectively.
b. Learning curve associated with new technology
There may be an adjustment period as the workforce adapts to the new methods. Proper training programs can mitigate potential productivity dips during this transition.
6.3. Material Availability
a. Sourcing high-quality self bonding steel
Not all self bonding steels are created equal. Selecting the right grade and quality impacts the performance and reliability of the final product.
7. Conclusion
7.1. Summary of Key Findings
a. Recap of benefits over traditional methods
Self bonding lamination offers significant advantages in production efficiency, cost-effectiveness, performance, and environmental impact. It streamlines manufacturing processes while enhancing the quality of electrical equipment.
In conclusion, self bonding lamination presents an alternative to traditional lamination methods. By offering improvements in efficiency, cost savings, and product performance, it addresses many of the challenges faced by modern manufacturers. While there are hurdles to overcome, such as initial investment and training, the long-term benefits make it a worthy consideration.