1. Introduction
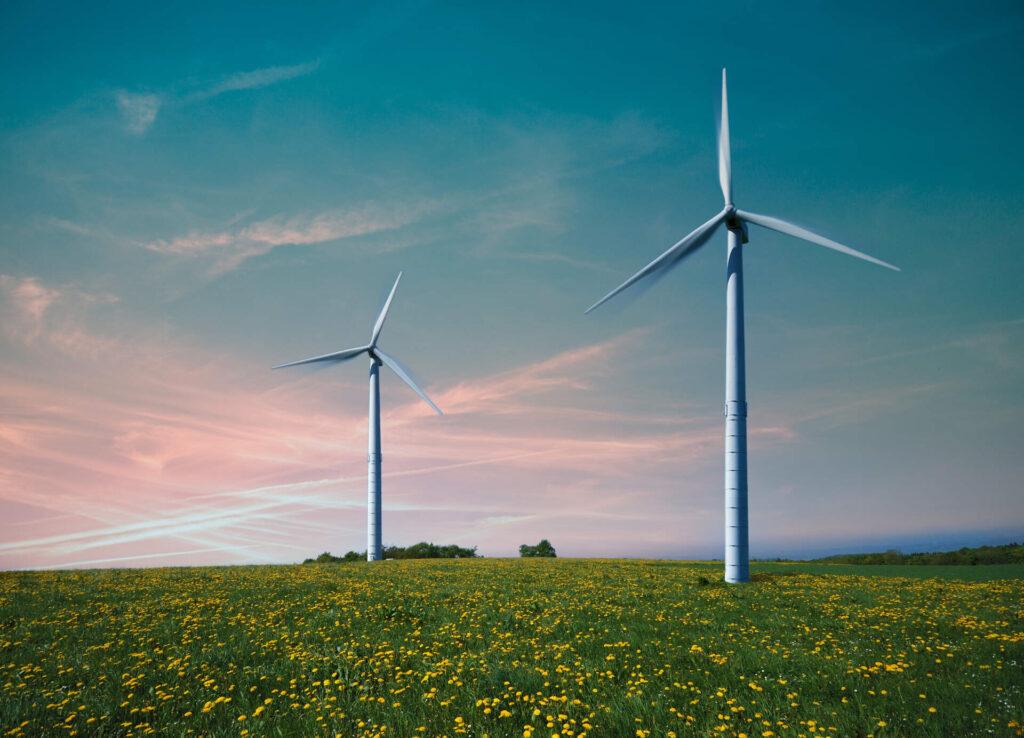
1.1 Overview of Wind Power and Efficiency Challenges
As global demand for reducing carbon emissions and seeking renewable energy sources grows, wind power has become one of the primary green energy sources. However, wind turbines often face challenges in enhancing efficiency during operation. They need to function under varying wind speeds and environmental conditions, which makes the optimization of each component’s design and material selection crucial. Besides wind variability, energy loss and heat generation are also significant factors that reduce power generation efficiency. To address these challenges, adopting advanced technologies and materials has become a core strategy within the wind energy sector.
1.2 The Importance of Lamination Technology in Wind Turbines
Motor Core Laminations are critical components in modern wind turbines, primarily used in the rotor and stator cores. These laminations are made by stacking multiple layers of thin steel sheets, with insulation between each layer to reduce the formation of eddy currents. Eddy currents are small circular currents generated within conductive materials, leading to heat and energy losses. By reducing the generation of eddy currents, lamination technology effectively enhances wind turbine operational efficiency.
Additionally, lamination technology improves the magnetic performance of the rotor and stator, thereby increasing wind turbine stability and power generation capability at various wind speeds. Laminations are typically made from high-performance materials such as silicon steel, known for its excellent resistivity and low hysteresis loss characteristics, which support efficient turbine operation. Under high wind conditions, these materials maintain optimal performance, reducing heat generation and enhancing the turbine’s durability.
Compared to solid core structures, using lamination technology in turbines can increase efficiency by up to 15%. This gain means that turbines can generate more electricity under the same wind conditions, thus improving the return on investment for wind energy projects. Furthermore, lamination structures effectively reduce heat accumulation, minimize mechanical losses, and extend the lifespan of wind turbines while reducing maintenance costs. These performance improvements align with the sustainability goals of the wind energy industry.
High-precision stamping and laser cutting technologies support the precise stacking of laminations, ensuring consistent thickness and shape, which helps maintain uniform magnetic flux and reduce additional energy losses. Through these advanced manufacturing processes, lamination technology fully realizes its potential, allowing wind turbines to operate efficiently and reliably under variable wind conditions.
Motor Core represent a crucial innovation in modern wind turbine design, offering significant advantages in reducing energy losses and enhancing motor performance. As the wind energy sector continues to expand rapidly, lamination technology will play a critical role in optimizing turbine design and meeting the global demand for renewable energy.
2. How Lamination Technology Enhances Efficiency
2.1 Reducing Eddy Currents in Wind Turbine Motors
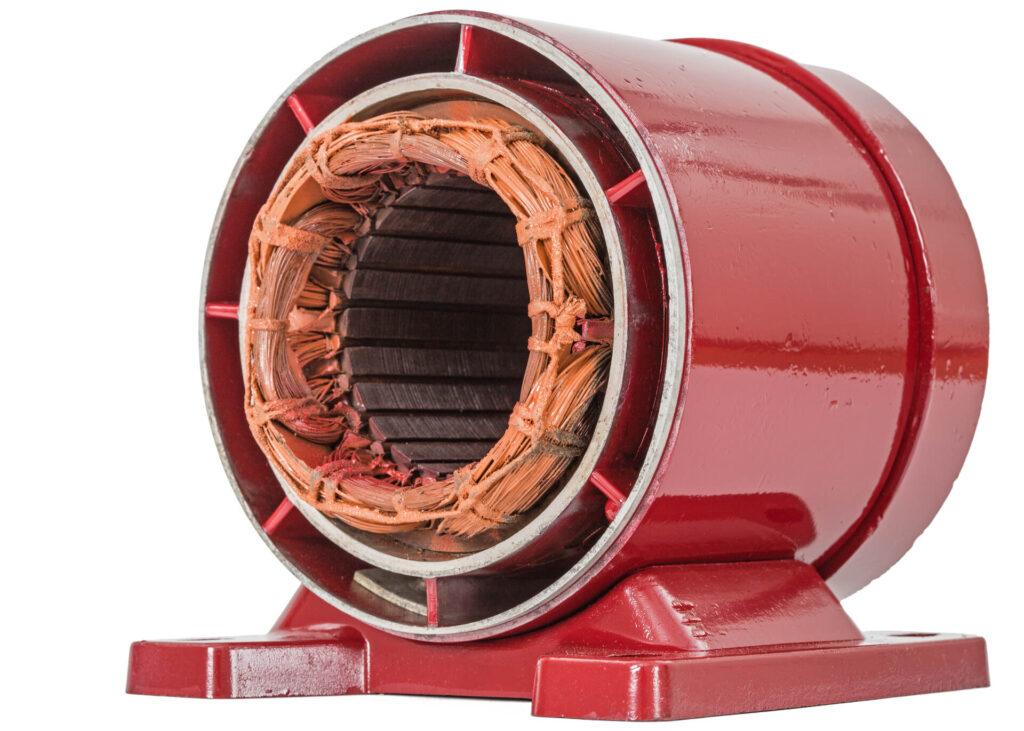
In wind turbines, eddy currents are a major source of energy loss. These currents occur when the magnetic field changes as the rotor turns, creating small circular currents within the conductive material. This results in heat within the material, which reduces overall generator efficiency and affects its lifespan. Lamination technology addresses this issue by utilizing a stacked structure of thin steel sheets, effectively blocking the formation of eddy currents.
Each layer of steel sheets in the lamination has an insulating layer, which prevents the eddy currents from circulating across a larger area and generating excess heat. This technology thus reduces energy loss due to eddy currents, which in turn enhances the power generation efficiency of wind turbines. Additionally, these steel sheets are usually made from high-resistivity silicon steel, known for its outstanding anti-eddy current properties. This material characteristic ensures low hysteresis loss even under high-speed conditions, making it an ideal core material for wind turbine generators.
2.2 Magnetic Flux Optimization for Improved Performance
Magnetic flux refers to the amount of magnetic field passing through a given area, and optimizing it is crucial for wind turbine performance. Lamination technology enhances magnetic flux by layering multiple sheets within the core. The arrangement of each sheet and the presence of insulation prevent unwanted magnetic field interference, resulting in a stable and uniform distribution of magnetic flux within the generator. This ensures continuous and stable operation, while also increasing torque and power output.
Lamination technology not only enhances turbine efficiency but also improves material adaptability under varying wind conditions. For example, the use of precision stamping and laser cutting techniques ensures the exact shape and thickness of each sheet, which helps maintain consistent magnetic flux and reduce energy loss due to misalignment.
Balancing efficiency enhancement and lifespan extension is key in wind turbine design, and lamination technology enables this balance. By precisely controlling the magnetic properties of materials, lamination technology not only increases power generation efficiency but also lowers operating costs and increases power output. As wind power continues to grow as a major renewable energy source, lamination technology will play an essential role in optimizing motor performance and achieving sustainability goals.
3. Materials and Advantages in Lamination Technology
3.1 Silicon Steel and Its Efficiency Benefits
Silicon steel is widely used in lamination technology for wind turbines due to its excellent energy loss reduction capabilities. With high resistivity and low hysteresis loss properties, it’s an ideal material for generators. Its high resistivity helps reduce eddy current formation, thus minimizing heat waste and enhancing power generation efficiency. This characteristic is especially important under fluctuating wind speeds, as it maintains generator stability and provides greater energy conversion efficiency.
Moreover, silicon steel’s resistance to magnetic changes makes it an optimal choice. Its stable magnetic properties ensure that wind turbines perform at their best under varying operational conditions. Silicon steel is also highly wear-resistant, allowing it to withstand prolonged operation and reducing the frequency of maintenance and replacement, which lowers overall operating costs.
The use of advanced alloy materials in lamination technology also allows manufacturers to tailor material combinations based on specific turbine needs. By selecting materials precisely, lamination technology optimizes the balance between generator weight and performance, which is crucial for efficiency, durability, and cost control in wind turbine design.
The choice of materials in lamination technology directly affects the overall performance of wind turbines. Laminations made from silicon steel not only improve magnetic properties and durability but also provide stable energy output under various environmental conditions, which is significant for meeting the growing global demand for renewable energy.
4. Manufacturing Processes for Lamination Stacks
4.1 Precision Stamping and Laser Cutting
The lamination manufacturing process starts with precision stamping and laser cutting, both of which are critical for ensuring the accuracy and consistency of each layer. Precision stamping cuts the metal sheets into the required shapes and sizes, often using high-precision dies to complete this task. For wind turbine needs, the thickness of these laminations must be extremely uniform to effectively reduce energy loss during operation.
Laser cutting further enhances processing precision. This technique uses a focused laser beam to process metal sheets, enabling precise edge cutting and flexibility in cutting complex shapes and designs. Laser cutting is well-suited for small-batch and custom demands, especially when laminations made from high-performance materials like silicon steel are required for turbine production. These precise cutting techniques ensure that the laminations conform to design specifications and maintain consistency throughout manufacturing.
4.2 Heat Treating for Enhanced Performance
After stamping and cutting, laminations usually undergo heat treatment to improve magnetic properties and increase durability. This process is designed to relieve internal stress generated during cutting and processing while enhancing magnetic permeability. The process typically involves heating the laminations to a specific temperature and then cooling them gradually to achieve the desired material properties. Through heat treatment, the internal structure of the laminations is strengthened, which reduces hysteresis losses and eddy current losses.
In wind turbine manufacturing, heat treatment also helps improve corrosion resistance and wear resistance, allowing laminations to operate over extended periods in harsh conditions. This technique optimizes the magnetic properties of the materials, further boosting turbine efficiency and stability during high-frequency operation. Since laminations endure long periods of operational pressure, heat treatment becomes a critical factor in improving overall performance and ensuring generator reliability.
Another advanced stacking technique in lamination manufacturing is the Backlack bonding technique. This technique involves applying a special self-adhesive coating on the lamination surface, which forms a robust bonding layer through heating and curing. Backlack technology avoids the iron losses potentially caused by traditional riveting and welding methods, and it reduces noise generated by vibration. This technique is particularly effective under high-frequency and high-speed operation, helping to lower energy loss in wind turbines.
With precision stamping, laser cutting, and heat treatment processes, lamination technology achieves high-precision and high-performance standards. These processes ensure that wind turbines can maintain stable operational performance across various environments and achieve higher energy conversion efficiency, providing more technical advantages for the wind energy industry.
5. Future Developments in Lamination Technology for Wind Power
5.1 Material Innovation and Advanced Technologies
As wind power technology continues to advance, lamination technology is also progressing toward the use of more efficient and durable materials. Future lamination materials may include a broader selection of alloys, such as rare earth metals, to further improve magnetic permeability and corrosion resistance. These material innovations can not only enhance wind turbine efficiency but also enable longer operation in harsh environmental conditions.
Moreover, emerging material technologies like nano-coatings and composites may significantly reduce eddy current generation, further minimizing energy losses. These new technologies will provide laminations with better magnetic control and increased durability, which will help boost overall turbine performance and reduce operational costs.
5.2 Automated Manufacturing and Smart Production
With the development of automation technology, the lamination manufacturing process is becoming increasingly precise and intelligent. Future lamination manufacturing processes are likely to adopt more robotics and artificial intelligence to ensure precise control over each lamination’s thickness and shape, meeting the highest standards.
Automated production processes can shorten manufacturing time, reduce labor costs, and increase production efficiency. Additionally, through data analysis and machine learning, production lines can detect and correct defects in real-time, ensuring high product quality.
Smart production technologies also allow manufacturers to adjust lamination materials and structures based on the specific requirements of wind turbines, achieving optimal performance. This flexible manufacturing model can adapt to varying wind conditions in different regions, enabling lamination technology to offer the most suitable products for diverse global markets.
5.3 Impact on Renewable Energy Development
Advancements in lamination technology are essential for enhancing wind power’s position in the global energy market. In the future, as global demand for renewable energy continues to grow, the application of lamination technology in wind power will further drive renewable energy development. Notably, as lamination technology improves, the cost of wind power generation will gradually decrease, while efficiency gains will make wind power more attractive, thus promoting its share in the energy mix.
These technological developments will help wind turbines achieve higher energy conversion efficiencies, further supporting global goals for carbon emission reduction. Lamination technology can reduce energy losses and make wind power generation more reliable, all of which align with core principles of sustainable development. Therefore, lamination technology will not only enhance wind turbine performance from a technical perspective but will also contribute to global environmental protection and renewable energy objectives.
6. Practical Applications and Case Studies
6.1 Lamination Technology in Offshore Wind Farms
Offshore wind farms often face harsh environmental conditions, requiring highly durable and efficient technological support. The application of lamination technology in offshore wind farms has proven effective in significantly reducing energy losses and enhancing operational efficiency. By using stacked thin steel sheets, these wind farms can effectively reduce eddy current losses, thereby ensuring stable generator operation in the volatile marine environment.
For example, in an offshore wind farm located in the North Sea, the use of lamination technology has improved wind turbine corrosion resistance under high humidity and high salinity conditions. These laminations, made of corrosion-resistant materials, can withstand long-term exposure to seawater. This case demonstrates that selecting suitable materials and lamination structures can greatly increase wind turbine operation time and reliability.
6.2 Efficient Application in Onshore Wind Farms
Compared to offshore wind farms, the primary challenge for onshore wind farms lies in wind speed variability. Lamination technology is also applicable to onshore wind farms, where it improves the magnetic properties of generators to cope with changes in wind speed. Laminations can be customized based on specific wind farm conditions to enhance turbine power output, achieving higher energy conversion efficiency.
In a successful implementation at an onshore wind farm in the American Midwest, lamination technology has been applied to cope with relatively stable but occasionally strong winds. To avoid energy losses during strong winds, the lamination design uses high-permeability silicon steel, which not only reduces eddy current formation but also improves generator performance under variable speed conditions. This allows the wind farm to maintain efficient operation over a broader range of wind speeds.
6.3 Application of Lamination Technology in Small Wind Turbines
Small wind turbines are suitable for remote areas or home use, where efficiency is critical under low wind speeds. The application of lamination technology in small wind turbines can achieve good power output, ensuring stable power generation even at low wind speeds. These laminations are often made from lighter materials to reduce the overall weight of the equipment, lowering installation and operational costs.
In a small wind power system located in a remote mountainous area, lamination technology and lightweight aluminum alloy materials were employed. This not only improved overall efficiency but also reduced maintenance needs. Since laminations minimize heat generation and energy loss, such small wind turbines can stably supply power even at low wind speeds, meeting the daily needs of local residents.
These examples show the flexibility of lamination technology in adapting to different wind power systems. Whether addressing harsh offshore conditions, enhancing onshore wind farm efficiency, or supporting the high-efficiency operation of small systems, lamination technology provides sustainable solutions, making a significant contribution to the development of the wind energy industry.
7. Cost-Effectiveness Analysis of Lamination Technology
7.1 Initial Costs and Long-Term Savings
Using lamination technology in wind power systems typically involves higher initial costs, primarily due to material and manufacturing process expenses. Laminations consist of multiple thin steel or alloy sheets, which must undergo precision stamping, cutting, and heat treatment to meet high standards of magnetic and electrical properties. Initial costs are also influenced by the materials chosen, such as silicon steel, with high-performance materials often being more expensive than standard steel.
※Further reading: Introduction to Self Bonding Electrical Steel: 5 Applications and Advantages
External Links:https://www.researchgate.net/publication/375570372_Efficiency_improvement_on_wind_turbine_through_bump_up_stepper_motor