1. Introduction
1.1 Importance of Selecting the Right Motor for Industrial Robots
a. Overview of Industrial Robots and Their Applications
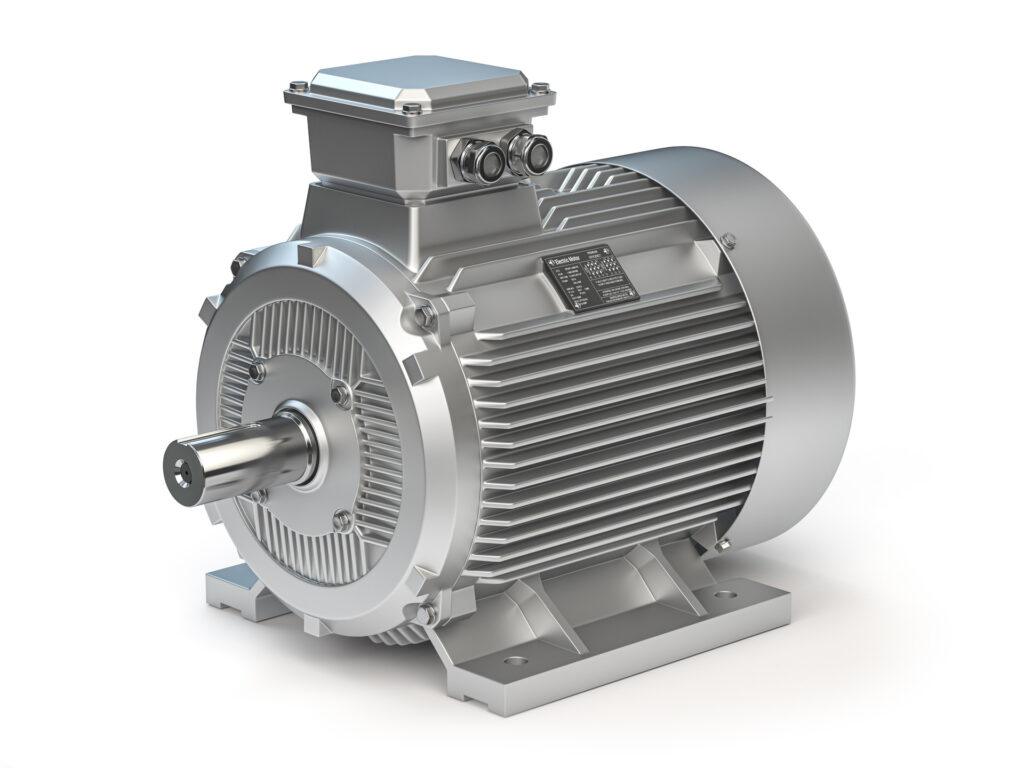
In the rapidly advancing field of industrial automation, selecting the right motor for your robot is crucial for optimal performance. Industrial robots are employed across various sectors, including manufacturing, assembly, and packaging, where they execute tasks with high precision and efficiency. These robots significantly enhance productivity, reduce human error, and operate in environments that may be hazardous to human workers. Common applications include welding, painting, material handling, and quality inspection, where robots perform repetitive tasks with exceptional accuracy and speed.
The motor is the heart of these robots, converting electrical energy into mechanical motion, enabling the robot to perform its designated tasks. The choice of motor directly impacts the robot’s performance characteristics, such as speed, torque, and precision. Therefore, understanding the different types of motors available and their specific advantages is essential for optimizing robot functionality and achieving the desired operational outcomes. By selecting the appropriate motor, you ensure that your industrial robot operates at peak efficiency, meeting the demands of your specific application and contributing to overall productivity and safety.
2. Types of Electric Motors Used in Industrial Robots
2.1 Direct Current (DC) Motors
a. Characteristics and Benefits
Direct Current (DC) motors are a popular choice in the field of industrial robotics due to their straightforward operation and excellent control over speed and torque. DC motors operate on direct current, where electrical energy is converted into mechanical rotation through the interaction of magnetic fields. One of the primary benefits of DC motors is their high starting torque, which is crucial for applications requiring immediate and powerful movements. Additionally, DC motors provide smooth and continuous speed control, making them ideal for precise operations.
b. Common Applications in Industrial Robotics
In industrial robotics, DC motors are often used in applications where fine-tuned control and high torque are necessary. For instance, robotic arms that handle assembly tasks or manipulate small parts benefit from the precise control offered by DC motors. These motors are also used in mobile robots, which require variable speeds and rapid directional changes. The versatility and reliability of DC motors make them a staple in various robotic applications.
2.2 Alternating Current (AC) Motors
a. Characteristics and Benefits
Alternating Current (AC) motors are another widely used type of motor in industrial robots, known for their robustness and efficiency. AC motors operate on alternating current, where the direction of the current changes periodically, allowing for consistent and reliable operation over extended periods. AC motors are favored for their simple and rugged design, which translates to lower maintenance requirements and longer lifespan. They are also highly efficient, especially in applications where continuous operation is necessary.
b. Common Applications in Industrial Robotics
AC motors are typically used in industrial robots that perform tasks requiring sustained power over long durations. For example, conveyor systems and automated guided vehicles (AGVs) commonly use AC motors due to their ability to handle continuous loads efficiently. Additionally, robots involved in heavy-duty tasks, such as material handling and palletizing, benefit from the durability and power of AC motors. The capability of AC motors to maintain consistent performance under varying loads makes them ideal for demanding industrial environments.
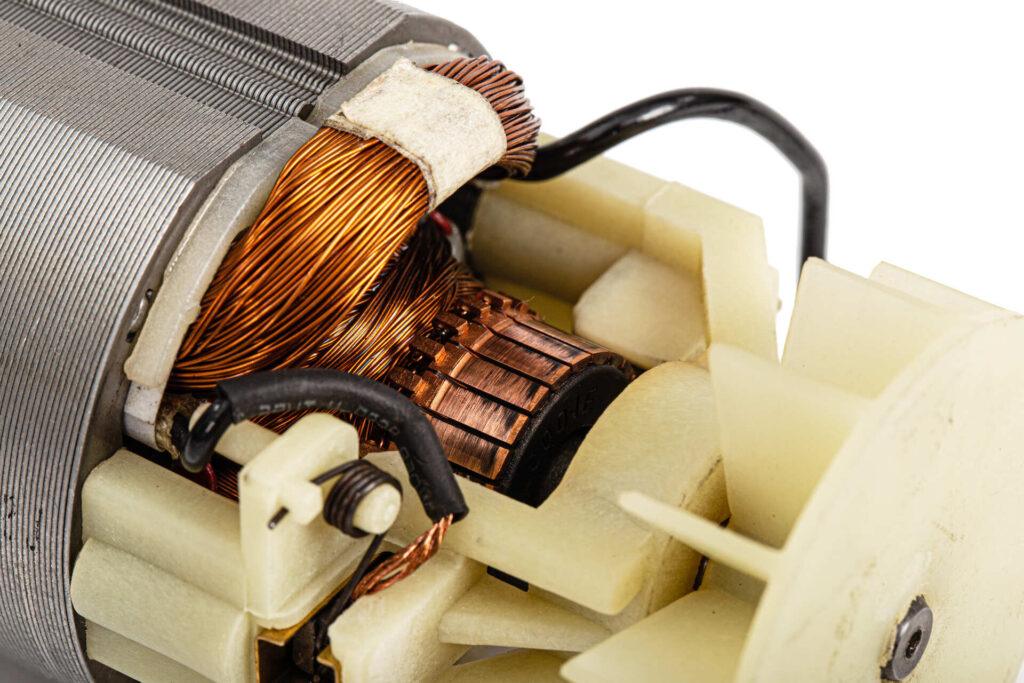
2.3 Brushless DC Motors
a. Characteristics and Benefits
Brushless DC motors (BLDC) represent a significant advancement in motor technology, offering numerous advantages over traditional brushed motors. BLDC motors eliminate the need for brushes, reducing wear and maintenance while improving efficiency and reliability. They operate on a similar principle as DC motors but use electronic commutation instead of mechanical brushes. This results in higher efficiency, reduced heat generation, and longer lifespan. BLDC motors also provide excellent torque and speed control, making them highly suitable for precision applications.
b. Common Applications in Industrial Robotics
In industrial robotics, BLDC motors are favored for applications that demand high efficiency, precision, and low maintenance. They are commonly found in robotic arms used for tasks like assembly, welding, and painting, where precise movements and high reliability are crucial. BLDC motors are also used in drones and other robotic systems requiring lightweight and efficient power sources. Their superior performance and longevity make BLDC motors a preferred choice for advanced robotic applications.
2.4 Comparison of Motor Types
a. Efficiency and Power Consumption
When comparing motor types, efficiency and power consumption are critical factors. BLDC motors generally offer the highest efficiency due to their electronic commutation, followed by AC motors, which are known for their efficient handling of continuous loads. DC motors, while efficient, may consume more power due to their mechanical brushes.
b. Durability and Maintenance
In terms of durability and maintenance, AC motors are typically the most robust and require less maintenance, making them suitable for heavy-duty applications. BLDC motors, with their brushless design, also require minimal maintenance and have a long operational life. DC motors, though reliable, may require more frequent maintenance due to brush wear.
c. Cost Considerations
Cost considerations also play a vital role in motor selection. DC motors are generally more affordable upfront but may incur higher maintenance costs over time. AC motors offer a good balance of cost and durability, making them cost-effective for long-term use. BLDC motors, while initially more expensive, provide superior efficiency and low maintenance, justifying their cost in precision and high-performance applications.
3. The Role of Stator Cores in Motor Performance
3.1 Importance of Stator Cores in Electric Motors
a. Impact on Efficiency and Power Output
Stator cores play a pivotal role in the performance of electric motors, directly influencing both efficiency and power output. The stator core is essentially the stationary part of the motor’s electromagnetic circuit, which works in conjunction with the rotor to create motion. The quality and design of the stator core determine how effectively the motor can convert electrical energy into mechanical energy. High-quality stator cores, typically made from silicon steel laminations, minimize energy losses due to hysteresis and eddy currents, thereby enhancing the overall efficiency of the motor. Efficient energy conversion results in lower operational costs and improved performance, making the selection of the right stator core material and design crucial for any motor application.
3.2 Materials and Manufacturing Processes
a. Common Materials Used for Stator Cores
The materials used in the construction of stator cores significantly affect the motor’s performance. Silicon steel is the most commonly used material due to its excellent magnetic properties and low electrical losses. The silicon content in the steel reduces the electrical conductivity, minimizing eddy current losses. Additionally, the steel is often laminated to further reduce these losses by increasing the electrical resistance between layers. This lamination process is vital as it helps to enhance the motor’s efficiency by reducing core losses.
b. Advanced Manufacturing Techniques
Advanced manufacturing techniques play a crucial role in the production of high-performance stator cores. Techniques such as high-precision stamping and laser cutting are used to create the thin laminations that make up the core. These processes ensure that each lamination is produced with high accuracy, reducing variations and improving the consistency of the motor’s performance. Furthermore, recent advancements in material science have led to the development of new alloys and coating techniques that further enhance the magnetic properties of the stator core. For instance, using nano-crystalline materials can significantly reduce core losses, leading to more efficient motors. These advanced manufacturing techniques ensure that stator cores meet the rigorous demands of modern industrial applications, contributing to the development of more powerful, efficient, and reliable electric motors.
4. Choosing the Right Motor for Your Application
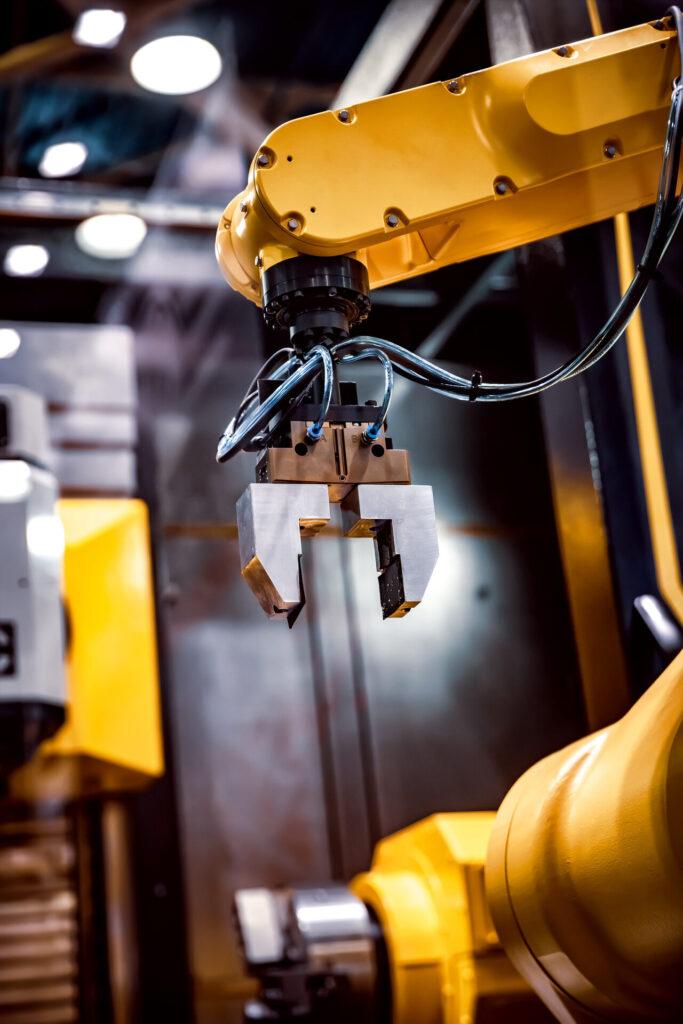
4.1 Assessing Robot Requirements
a. Load Capacity and Torque Needs
When selecting the appropriate motor for an industrial robot, it is essential to first assess the robot’s specific requirements, particularly its load capacity and torque needs. Load capacity refers to the maximum weight the robot can handle, which directly impacts the choice of motor. A motor must provide sufficient torque to move the robot and its load efficiently. High-torque motors are necessary for applications involving heavy loads or requiring significant force, such as material handling or palletizing. Conversely, for lighter loads or precision tasks, a motor with lower torque but higher speed might be more suitable.
b. Speed and Precision Requirements
In addition to load capacity and torque, speed and precision are critical factors in motor selection. Different applications demand varying levels of speed and precision. For instance, assembly line robots that perform repetitive tasks rapidly need motors that can offer high speed and consistent performance. On the other hand, tasks that require fine movements and high accuracy, such as robotic welding or delicate part assembly, necessitate motors with precise control capabilities. Understanding the specific speed and precision requirements of the robot’s application ensures the selection of a motor that can deliver optimal performance.
4.2 Matching Motor Characteristics with Application Needs
a. Selecting Based on Efficiency and Power
After assessing the robot’s requirements, the next step is to match the motor characteristics with the application needs. Efficiency and power are crucial considerations. Motors that offer high efficiency reduce energy consumption and operational costs, which is particularly important for robots that operate continuously or for extended periods. Additionally, the power rating of the motor must align with the demands of the application to ensure reliable and effective performance. For high-power applications, such as heavy-duty lifting or continuous operation, selecting a motor with an appropriate power rating is essential.
b. Considering Long-Term Durability and Maintenance
Long-term durability and maintenance are also key factors in motor selection. Industrial robots often operate in demanding environments, where reliability and minimal downtime are critical. Choosing a motor with robust construction and low maintenance requirements can significantly enhance the robot’s longevity and reduce operational interruptions. Brushless DC motors, for instance, are known for their durability and low maintenance due to the absence of brushes, which reduces wear and tear. AC motors are also preferred for their simple, rugged design that offers long-term reliability with minimal maintenance.
5. Case Studies and Practical Examples
5.1 Case Study of a Manufacturing Robot Using a DC Motor
a. Application Details and Motor Performance
In a leading automotive manufacturing plant, a robotic arm utilized a DC motor to handle the assembly of small parts. This application required precise control and high starting torque, characteristics that DC motors excel in. The robot was tasked with assembling delicate components, requiring smooth and continuous speed control to ensure accuracy and avoid damage to parts. The DC motor’s ability to provide high torque at low speeds was crucial in performing these delicate operations efficiently. Over time, the plant reported increased productivity and reduced error rates, demonstrating the effectiveness of DC motors in high-precision assembly tasks.
5.2 Case Study of a Robotic Arm Using a Brushless DC Motor
a. Application Details and Motor Performance
A robotic arm in an electronics manufacturing facility employed a brushless DC (BLDC) motor for tasks involving soldering and component placement. The application demanded high efficiency, precision, and minimal maintenance, all of which are strengths of BLDC motors. The brushless design eliminated the wear and tear associated with brushes, significantly reducing maintenance downtime. The electronic commutation of the BLDC motor provided precise control over speed and torque, essential for the delicate and accurate placement of electronic components. As a result, the facility experienced improved operational efficiency and product quality, showcasing the advantages of BLDC motors in precision-driven applications.
5.3 Lessons Learned and Best Practices
a. Key Takeaways from Case Studies
From these case studies, several key lessons and best practices emerge. Firstly, matching the motor type to the specific application requirements is crucial. For tasks demanding high starting torque and precise control, DC motors are highly effective. Conversely, for applications requiring high efficiency, precision, and low maintenance, BLDC motors are ideal. It’s also clear that considering the long-term operational costs and maintenance requirements can lead to more sustainable and cost-effective solutions. These case studies highlight the importance of thorough application analysis and informed motor selection to optimize performance and reliability in industrial robotics.
6. Conclusion
6.1 Summary of Key Points
a. Importance of Selecting the Right Motor
In summary, selecting the right motor for industrial robots is paramount to achieving optimal performance, efficiency, and reliability. The motor type directly influences the robot’s capabilities, including load capacity, torque, speed, and precision. Understanding the specific requirements of the application and the characteristics of various motor types—such as DC, AC, and brushless DC (BLDC) motors—enables manufacturers to make informed decisions. DC motors are ideal for applications requiring high starting torque and precise control, while AC motors are suitable for continuous operations with heavy loads. BLDC motors offer high efficiency, low maintenance, and precision, making them perfect for advanced robotic applications.
6.2 Final Recommendations
a. How to Approach Motor Selection for Industrial Robots
When approaching motor selection for industrial robots, it is essential to conduct a thorough analysis of the application’s demands. Start by assessing the load capacity and torque needs, ensuring the selected motor can handle the operational requirements without compromising performance. Next, consider the speed and precision necessary for the tasks the robot will perform. Match these requirements with the motor’s characteristics, balancing efficiency and power to optimize performance. Additionally, consider long-term durability and maintenance to minimize operational downtime and extend the robot’s lifespan.
For manufacturers seeking high-quality motor core lamination products tailored to their specific needs, our company offers a range of solutions designed to enhance motor performance and reliability. Our expertise in providing exceptional stator cores support your motors to operate at peak efficiency. Contact us today to learn more about our products and how we can support your industrial robotic applications with customized motor core solutions.
※Further Reading: 5 Revolutionary Trends in Stator Core Manufacturing Technology: Automated Winding and Smart Factory Innovations
External Links:
Source reference from: