Discover 5 key benefits of Self Bonding Electrical Steel, from energy efficiency and high performance to its critical role in electric vehicles and wind power generation.
Self Bonding Electrical Steel is a cutting-edge material that has revolutionized the manufacturing of high-performance motors and transformers. Known for its self-bonding properties, this material eliminates the need for additional adhesives or welding, simplifying the production process while enhancing efficiency and reliability. To learn more about the advantages of Self Bonding Electrical Steel, you can explore its detailed applications here.
In this article, we explore five key benefits of Self Bonding Electrical Steel that make it a must-have material in modern industrial applications.
1. High Magnetic Permeability for Efficient Flux Conduction
High magnetic permeability is one of the key reasons why Self Bonding Electrical Steel stands out in motor and transformer applications. Magnetic permeability refers to how effectively a material conducts magnetic flux, which is essential for motors and transformers to operate efficiently. The higher the magnetic permeability, the better the material can channel magnetic fields, which improves the motor’s overall efficiency and performance.
For industries that rely on precision and high output, such as electric vehicles and wind turbines, using materials with high magnetic permeability is critical. It allows motors to perform more effectively, improving energy conversion and power output.
2. Low Core Loss for Higher Energy Efficiency
Another significant benefit of Self Bonding Electrical Steel is its low core loss, meaning it minimizes the energy lost during the magnetization and demagnetization processes. Core loss is a key factor in determining the energy efficiency of motors and transformers. The lower the core loss, the less energy is wasted, which directly improves the overall efficiency of the system.
In industries where energy efficiency is a priority, such as electric vehicles or renewable energy, reducing energy loss is crucial for lowering operating costs and maximizing performance. Self Bonding Electrical Steel helps achieve this by reducing unnecessary energy loss, making it a top choice for motors and transformers.
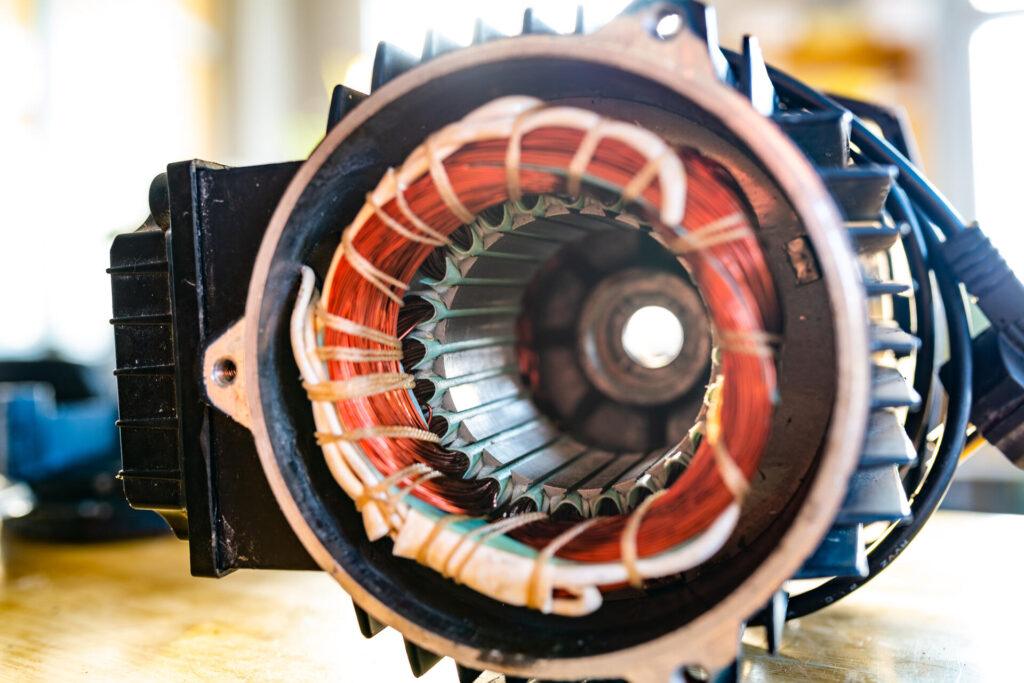
3. Simplified Production Process with Self-Bonding Properties
The self-bonding properties of this steel eliminate the need for adhesives or welding during the production of motor cores and transformer laminations. This greatly simplifies the manufacturing process, reducing both production time and costs. It also enhances the reliability of the final products since fewer bonding materials mean fewer potential points of failure in the system.
By streamlining the production process, manufacturers can achieve higher efficiency without compromising on product quality. The ability to create reliable motor cores and transformer laminations without the added complexity of adhesives or welding makes Self Bonding Electrical Steel an attractive choice for manufacturers looking to optimize their production lines.
4. Application in Electric Vehicles and Wind Power Generation
Electric Vehicle Drive Motors
The electric vehicle (EV) industry is rapidly growing, and the demand for efficient, high-performing motors is increasing. Self Bonding Electrical Steel offers the ideal solution for electric vehicle drive motor cores. Its high magnetic permeability and low core loss make it possible for motors to run more efficiently, which helps extend battery life and increase the driving range of electric vehicles.
In a study published in the Journal of the Brazilian Society of Mechanical Sciences and Engineering, researchers explore how new materials, such as self-bonding electrical steel, enhance the performance of EV drive motors. They found that bonding technologies improve motor efficiency by reducing energy loss and weight, aligning well with the goals of the EV industry to optimize battery life and reduce emissions(SpringerLink).
Using Self Bonding Electrical Steel also simplifies the manufacturing of electric vehicle motors, allowing producers to meet the rising demand for EVs more cost-effectively. The steel’s self-bonding characteristics streamline production, reducing manufacturing complexity while maintaining the high-quality standards required in electric vehicle motors.
Wind Power Applications
Wind turbines, which are an essential component of renewable energy, also benefit from the use of Self Bonding Electrical Steel. In wind turbines, motor cores made from this material can significantly reduce energy loss, allowing the turbines to generate more power from the same amount of wind. The result is more efficient electricity generation, making wind turbines more productive and cost-effective.
By improving energy efficiency in wind power generation, Self Bonding Electrical Steel supports the transition to cleaner energy sources. It helps reduce reliance on fossil fuels and contributes to a more sustainable future by increasing the viability of renewable energy solutions like wind power.
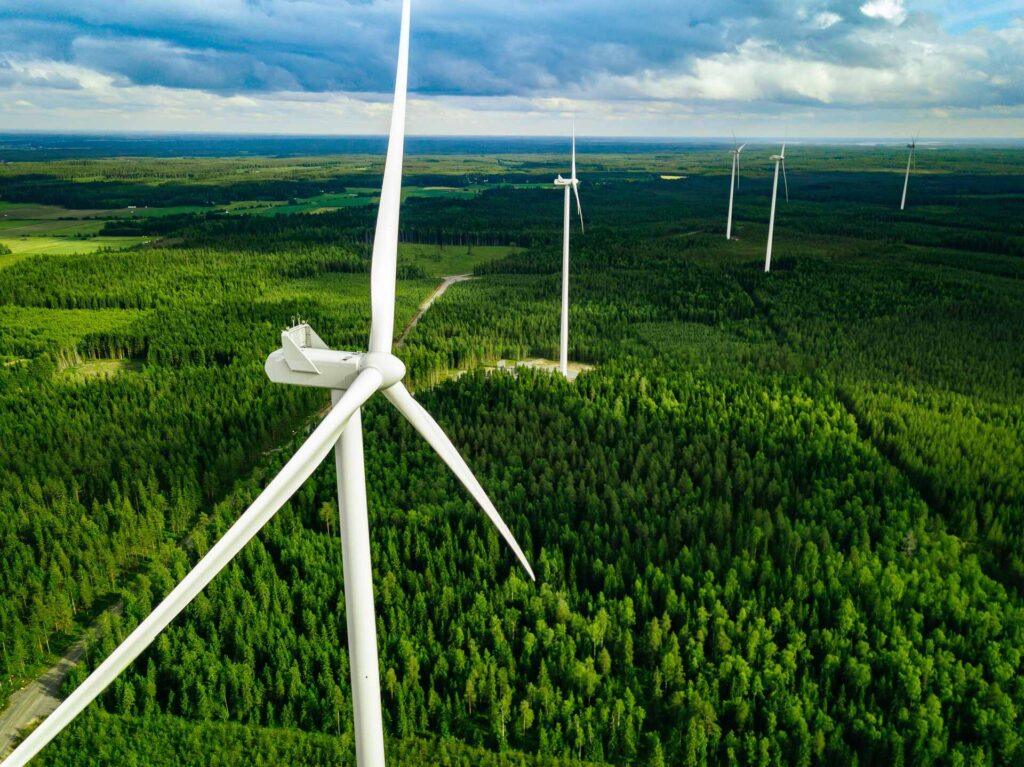
5. Environmental and Sustainability Benefits
The application of Self Bonding Electrical Steel not only improves energy efficiency but also offers significant environmental benefits. By enhancing the efficiency of motors and transformers, it reduces energy consumption and lowers carbon emissions. As companies and industries increasingly focus on sustainability, using materials that contribute to reducing the environmental impact is becoming more important.
By minimizing energy loss and improving overall efficiency, Self Bonding Electrical Steel helps companies reduce their carbon footprints. This makes it an ideal choice for businesses aiming to meet stricter environmental standards and adopt more eco-friendly practices.
For example, the increased energy efficiency in electric vehicle motors and wind turbines means that less energy is wasted during operation. This reduces the overall environmental impact of these technologies, helping industries transition to greener, more sustainable energy solutions. By choosing Self Bonding Electrical Steel, companies can also demonstrate their commitment to sustainability, which can be an essential factor in gaining a competitive edge in today’s market.
Conclusion
The future of Self Bonding Electrical Steel is bright as its applications expand across various industries that prioritize performance and energy efficiency. From electric vehicles and wind power to industrial motors and transformers, this material plays a crucial role in improving energy utilization and reducing environmental impact.
Self Bonding Electrical Steel offers several key benefits, including high magnetic permeability, low core loss, a simplified production process, and significant environmental advantages. These features make it an indispensable material in modern manufacturing, particularly in industries that value efficiency and sustainability.
By adopting Self Bonding Electrical Steel in your production processes, you can enhance product performance, reduce production complexity, and contribute to environmental sustainability. This material represents a critical advancement in the pursuit of more efficient and eco-friendly manufacturing practices, making it a cornerstone of future industrial growth and innovation.